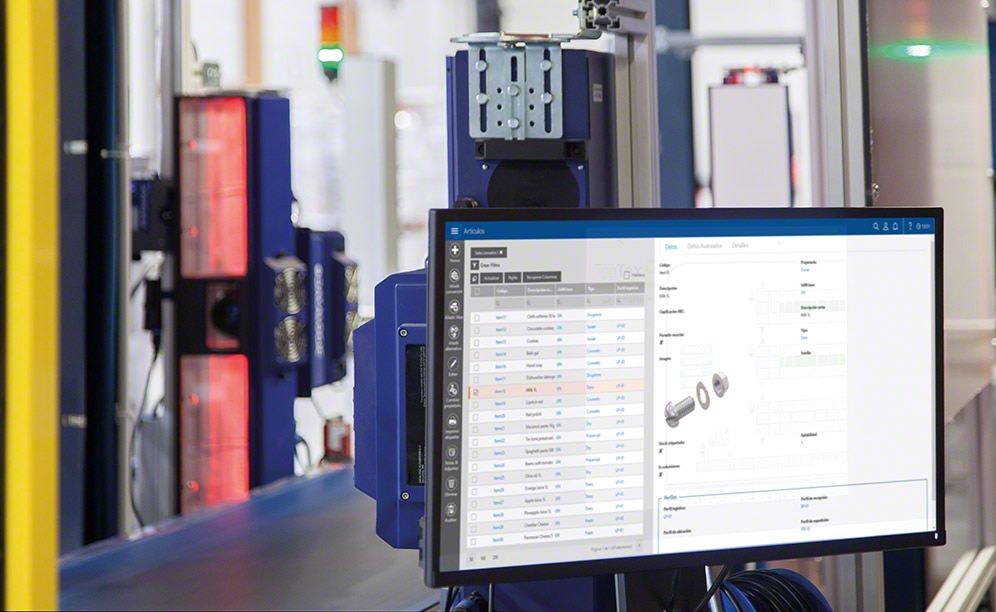
Easy WMS increases the order picking workflows of Spax by 21%
Easy WMS of Mecalux was set up in Spax's bolt warehouse to improve picking workflows
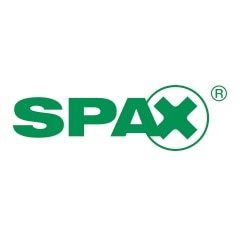
Picking is one of the main operations at this German bolt manufacturer’s storage facility. The distribution centre Spax runs in Leganés, close to Madrid, is where it prepares close to 21 orders a day. For maximum throughput of this operation and all other in-warehouse processes, the company has installed the Easy WMS warehouse management system. Through this system’s assistance, with thirteen radiofrequency (RF) devices and eleven pick-to-light (PTL) devices, storage and picking tasks are done faster and more accurately.
Who is Spax?
Spax is a German company that opened in 1823 as Altenloh, Brinck & Co (ABC). From its beginnings, it specialised in making and distributing bolts on a national level. However, these days, the group is breaking new ground and selling its products globally. Spax manufactures all its bolts in the Ennepetal production centre (Germany) and, from there, distributes worldwide.
Warehouse features
The bolt maker Spax has installed the Easy WMS by Mecalux in its 5,000 m2 distribution centre in Madrid. This facility contains more than 12,000 locations, letting the company store all its SKUs. The WMS organises all in-warehouse workflow movements, processes and operations, which promotes cost savings and better-quality customer care.
A daily inflow of 17 pallets of a single SKU is routine. Afterwards, the operators set these boxes into the corresponding shelf locations. Easy WMS uses algorithms and parametrised rules to assign a location to the more than 1,000 different products that Spax carries, bearing their characteristics and demand level in mind.
Getting orders ready
When picking items, operators sweep through the warehouse taking products directly off the racks, as per the instructions sent to them on the radiofrequency devices.
The RF terminals provide top-notch communication between the WMS and the workers, in addition to making product IDing a snap. Operators are invariably guided by the WMS that traces out the routes that must be followed up and down the warehouse, pinpointing the position worker must go to and how many products must be taken. Last but not least, operators confirm they have fulfilled the preset orders.
Following that, items that comprise each order are sorted on the live racking. Put-to-light devices on the racks signal the delivery position and the stock amount the operators must slot into each channel. Easy WMS allocates an order to each slot on the live storage for picking.
The use of put-to-light devices assists multi-order prep. Plus, it eliminates any errors due to its precision in classifying the products. Finished orders are stored and, when requested, Easy WMS creates commands to get them moved to the dock zone. The warehouse has 20 loading docks. Each day 160 exit orders are managed with an average of 14 product lines per order.
Advantages for Spax
- High productivity: by including the Mecalux Easy WMS, operations that are carried out in the Spax distribution centre are faster and more reliable.
- Potent picking: the radiofrequency and the put-to-light devices oversee the workers constantly and stop picking errors from happening.
- Stock control: Easy WMS is always aware of stock levels and efficiently organises the movements of the merchandise and the fulfilment of the different operations.
Gallery
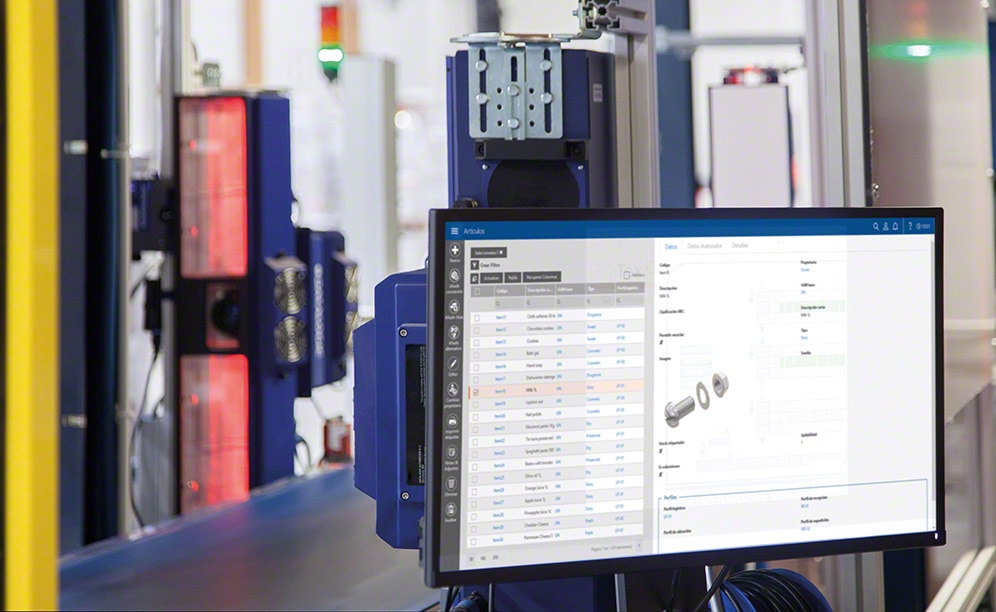
Order picking in the bolt warehouse of Spax
Ask an expert