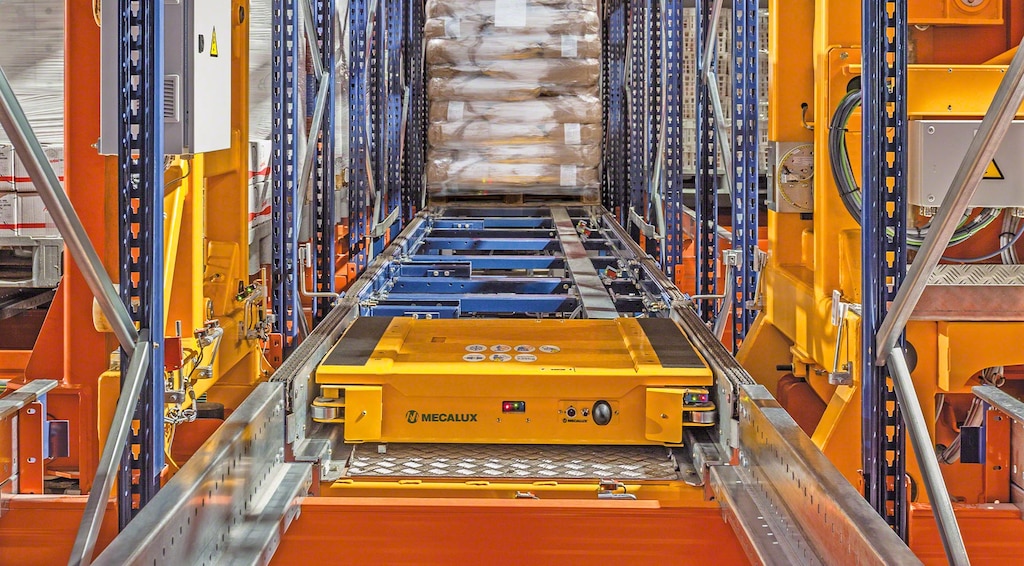
Automated Pallet Shuttle
The automated Pallet Shuttle is a compact pallet storage system that uses an electric shuttle and automated handling systems to boost capacity and productivity in the warehouse.
Product
Automated Pallet Shuttle: combining benefits to give you the edge
This system combines automatic handling equipment with compact storage systems. It enables companies to cut costs, enhance their supply-chain performance and, thus, differentiate their product and service offerings.
With this storage solution, forklifts are replaced by stacker cranes or transfer cars, which transport the motorised shuttle and the load in their cradles. The shuttle is inserted into the storage channels, placing each of the pallets in the deepest available position. This is all done by following orders generated by the Easy WMS Warehouse Management System.
In short, the automated Pallet Shuttle optimises the storage capacity of compact systems while reducing the times used in each operation of an automated system.
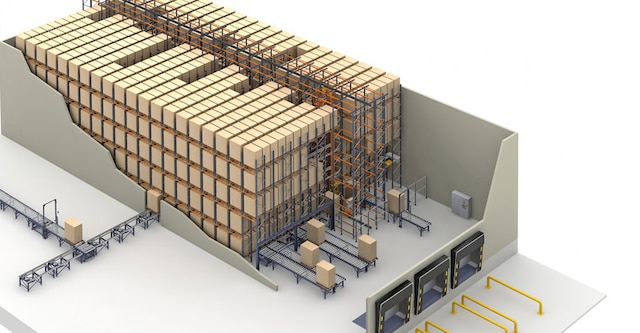
Applications
Automated Pallet Shuttle: perfect solution for mass movement of product
The installation of a high-density AS/RS with the Pallet Shuttle is especially suitable in cases requiring a marked increase in productivity and, hence, that need to move a high number of pallets/hour.
In general, this solution is appropriate in the following cases:
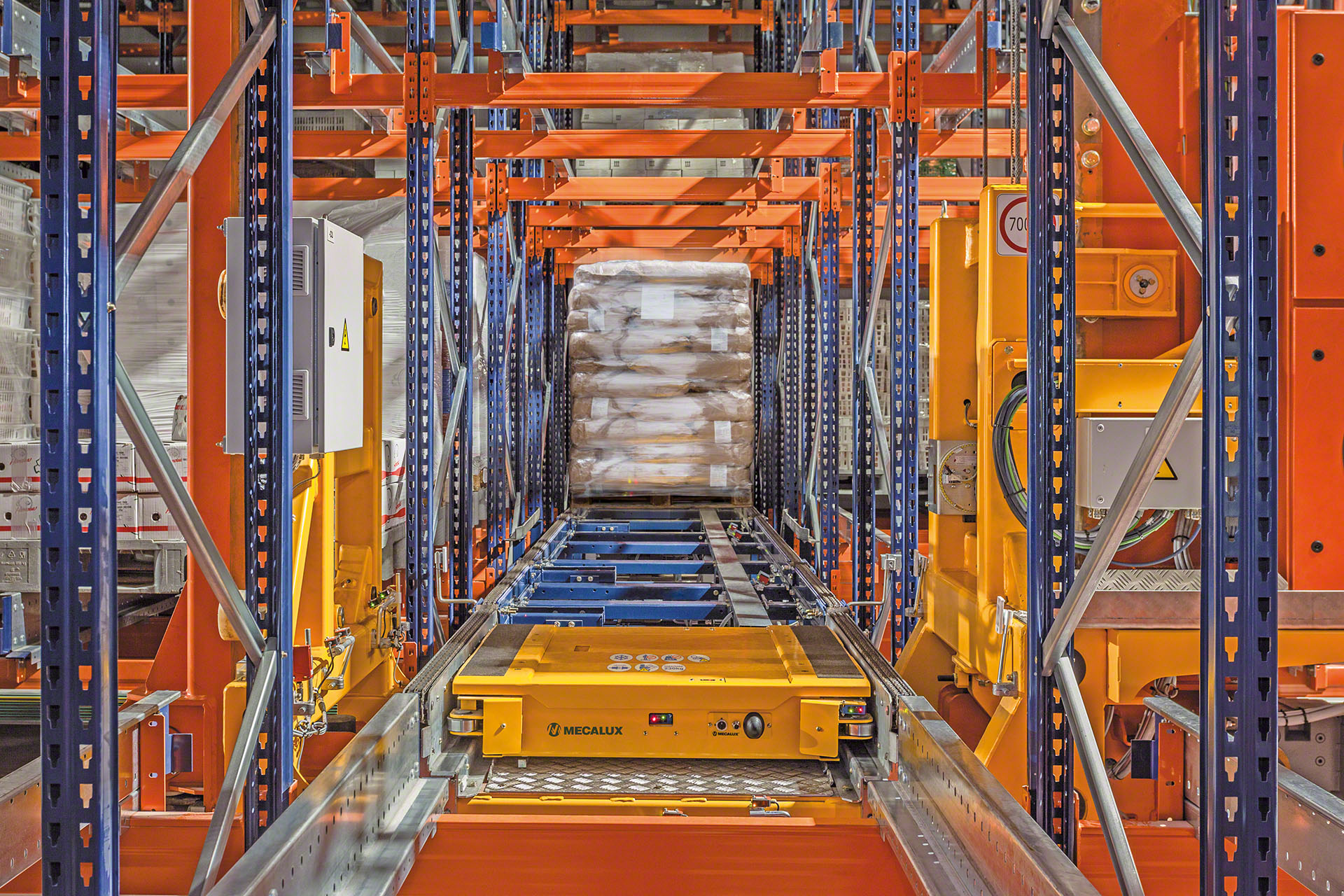
Advantages
Bringing together the benefits of compact storage and automation
- Maximum space savings in compact systems with storage channels up to 40 m deep and racking over 40 m tall.
- Rapid movement of the electric shuttle, which reduces goods entries and exits.
- Major increase in the number of cycles/hour compared to other storage systems.
- Goods-to-person system, whereby the load is moved to the pick stations automatically.
- Shuttle supercapacitors are charged automatically while onboard the stacker crane or transfer car, so the shuttle is always ready to go.
- Cost savings in handling equipment, warehouse surface area, staff and energy (especially in freezer warehouses).
- System that allows for different configurations depending on the number of SKUs, quantity of pallets and movements required in each case.
- Compact automated storage and retrieval systems (AS/RS) operating with the Pallet Shuttle ensure the utmost safety of the operators, the load and the AS/RS itself.
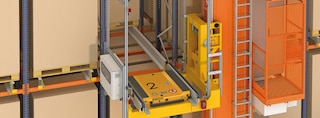
Variants
Compact AS/RS with Pallet Shuttle
In automated storage and retrieval systems (AS/RS) with the Pallet Shuttle, forklifts are replaced with automatic handling equipment, stacker cranes or transfer cars. This considerably reduces the time used for each operation.
The choice of handling equipment will depend on the number of entry and exit movements, the number of SKUs and the quantity of pallets per SKU or batch. The key difference between the two systems lies in the potential number of pallets that can be moved by a solution with transfer cars compared to one with stacker cranes, as this quantity is multiplied by the number of levels the system has.
Technical data
Pallet width | 1,200 mm |
---|---|
Pallet depth | 800/1,000/1,200 mm |
Load capacity | Up to 1,500 kg |
Wheels | 8 |
Travel speed without load | Ambient: 110 m/min; cold: 76 m/min |
Travel speed with load | 70 m/min |
Lift time | 2 s |
Operating temperature | Ambient: from 5 to 45 °C; cold: from -30 to 5 °C |
Battery | Supercapacitors |
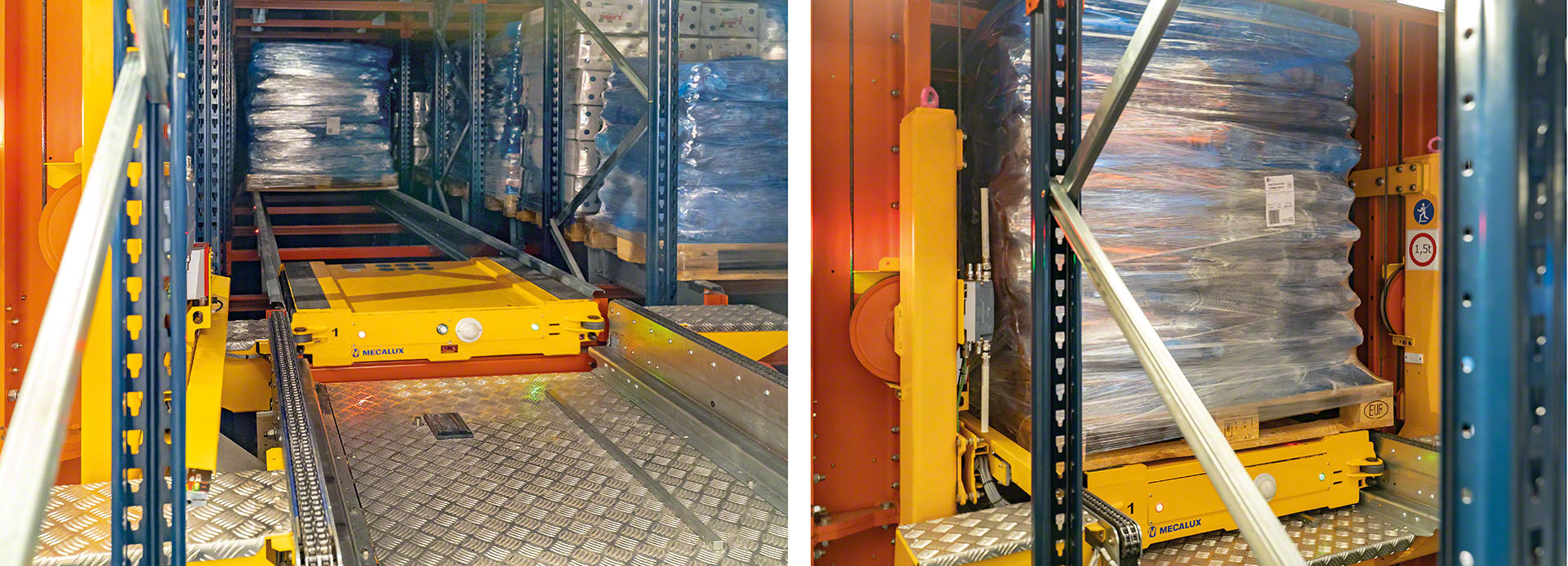
Downloads
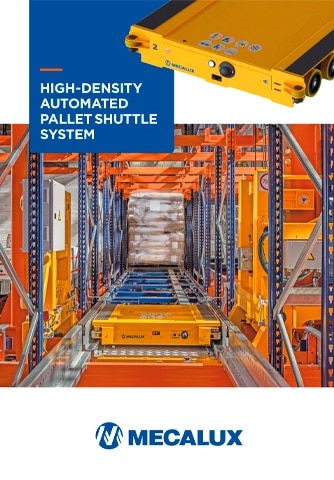
Download catalogue
DownloadAsk an expert