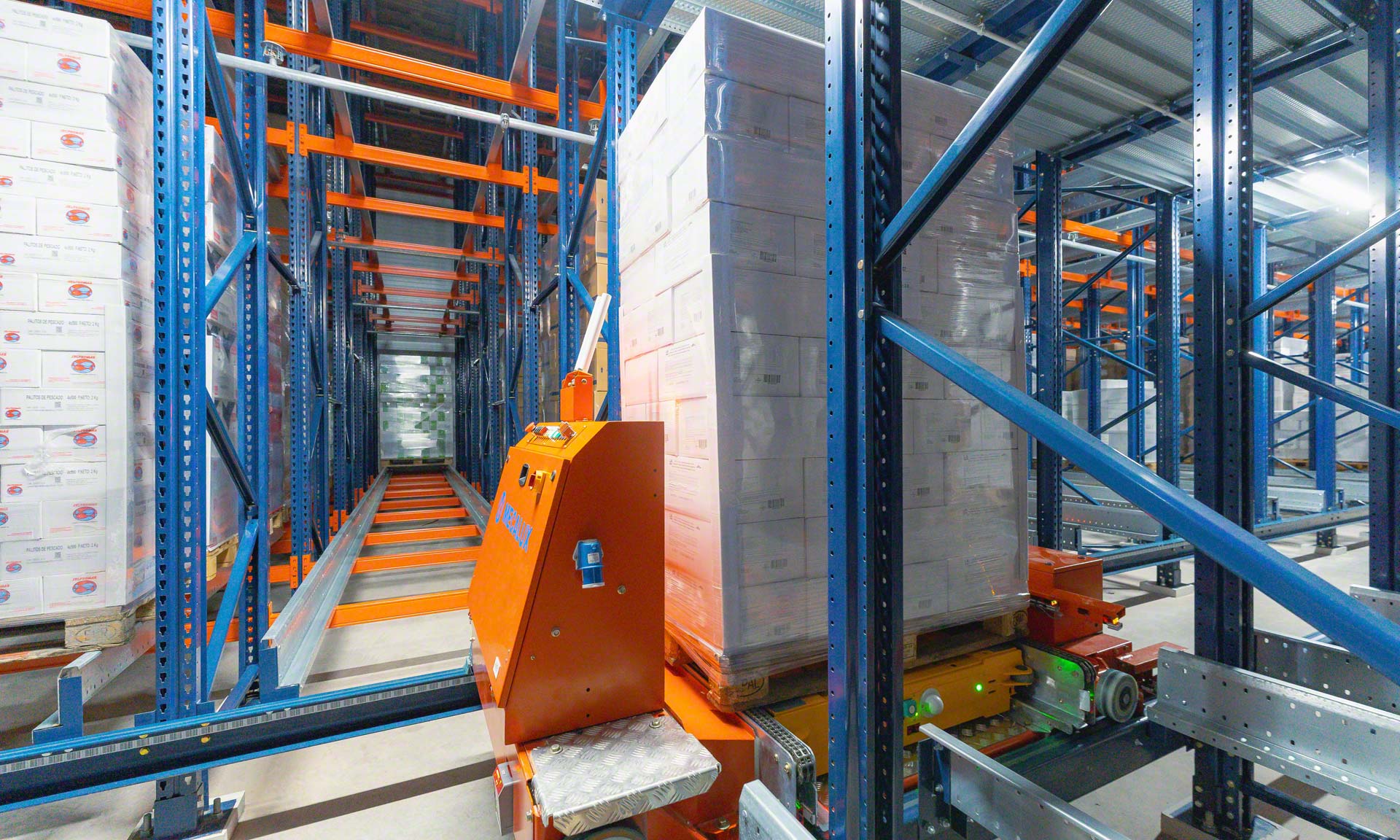
Sub-zero, future-forward automation
The warehouse operates at a constant temperature of -25 °C to ensure the correct preservation of the food
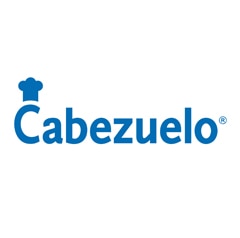
What’s the best solution for managing an annual production of 10,000 tonnes of food at -25 °C? Deep-frozen food company Cabezuelo Foods knew the answer: automation. The firm has turned to automation to facilitate the storage and distribution of its products to customers all around Europe. The company - which has achieved sustained year-on-year growth of around 10% in recent years - has opened a new clad-rack warehouse with the Pallet Shuttle system with transfer cars from Mecalux to centralise all its logistics operations.
Founded in Spain in 1978, Cabezuelo Foods is a family-run business dedicated to the production and distribution of precooked, deep-frozen food.
At its production plant in Socuéllamos (Spain), Cabezuelo Foods produces close to 10,000 tonnes of products annually for companies in the hospitality industry in more than 20 countries. “Over the last 10 years, we’ve seen steady growth of 8-10% annually,” says company owner Félix Cabezuelo.
To cope with this increased activity, the business needed to improve its supply chain efficiency. “Before, we stored the finished goods on manual storage racks in the production centre itself and 600-900 tonnes of raw materials in external warehouses. This solution wasn’t very practical and increased the cost of transporting goods between the various facilities and the production plant,” explains Cabezuelo.
The company decided to put a new warehouse into operation to store all the goods under one roof and effectively deal with the growth pace. Cabezuelo started this project with a clear priority in mind: “We were looking to expand our storage space to accommodate all our current and future production.”
Automation for continued growth
To outfit the new warehouse, the company contacted Mecalux because “we’ve been partnering with Mecalux for many years now. Plus, we had a lot of faith in the sales team when it came to proposing the solution that would meet our needs.”
Cabezuelo adds: “At first, we considered installing Movirack mobile racking because of its low investment cost. But we understood that, if we really wanted to transform our logistics operations, we had to take into account our future prospects. We didn’t want to implement a storage system that could become obsolete for us in three or four years.”
Cabezuelo used to manage its goods manually. That is, the operators would pick the products as they came off the production lines and place them on the racks using forklifts. Consequently, the risk of error was high, and the company wanted to avoid this at all costs.
After analysing Cabezuelo Foods’ needs, Mecalux suggested installing an automated storage and retrieval system (AS/RS) to house the finished product: the automated Pallet Shuttle system served by transfer cars. Mecalux has also implemented the Easy WMS warehouse management system, which rigorously controls the goods, from receipt through to dispatch.
Automating a facility does require a higher initial investment than a manually run warehouse. However, the advantages of automation - which include load safety, availability, productivity and energy efficiency - provide a very quick return on investment. “We chose to automate because we saw that it would be the best solution for dealing with the anticipated growth over the next five years,” says the company’s owner.
Technical characteristics of the automated warehouse
The facility stands 28 m tall and has a clad-rack structure. It operates at a constant temperature of -25 °C to guarantee that the food is stored properly and to preserve its flavour and properties for a long time.
The facility comprises a single 54-metre-long aisle with racking on both sides. The racks are 8 levels high and 11 pallets deep. On each level, a transfer car transports a motorised shuttle containing the goods to the corresponding storage channel. Once there, the shuttle raises the pallet and moves it inside the storage channel to the deepest free location. “Now that we’ve adapted to this new system, we’re thrilled because we’ve achieved what we set out do to in terms of our warehouse operations: goods inflows and outflows are both a lot faster,” says Cabezuelo.
One advantage of the automated Pallet Shuttle is that it makes the most of the available space to increase storage capacity (in this case, 5,104 pallets with 350-450 SKUs). Cabezuelo says, “When it comes to warehousing capacity, we can continue to grow, without any constraints.”
Likewise, using a compact storage system notably reduces the energy used to generate cold air. Energy consumption per pallet, therefore, is lower (since it is distributed among a larger number of pallets stored).
At the front of the warehouse, Mecalux has set up a picking area with an anthropomorphic robot. The entire operation is automated: the goods needed to complete the orders are sent to this zone in a completely autonomous way. Once there, the anthropomorphic robot extracts the boxes from the pallets and sorts them into orders. This robot can perform 150 movements per hour, that is, 1,350 boxes an hour.
Smooth, automated, efficient operations
Every day, the warehouse receives between 5 and 6 lorries loaded with finished products from the Cabezuelo Foods production plant, that is, up to 198 pallets that need to be stored as soon as possible.
The pallets cross a checkpoint, where it is verified that they meet the requirements established for their storage in the warehouse. This process allows Easy WMS to read the pallet barcode, identify the item and assign it a location.
Easy WMS incorporates rules and algorithms to assign a location to each pallet based on its turnover. Low-turnover products are deposited on the higher levels of the racks, while high-turnover items are placed on the lower levels, closer to the end of the aisle to streamline their entry and exit.
In this warehouse, orders are also prepared at the pick station. Although the number of orders varies depending on customer demand (with Tuesdays and Thursdays being the busiest days), the company generally dispatches 100-150 orders a day.
Cabezuelo notes the improvement in order prep: “The pick station with the anthropomorphic robot was installed afterwards, once the automated warehouse was already up and running. This new automated area has been fundamental for our supply chain. Manual picking is very repetitive and far more cumbersome. Thanks to automation, the operation is now much faster and more efficient.”
Benefits of a clad-rack building
- Leveraged space: an automated clad-rack-warehouse optimises the available surface area to achieve the greatest possible storage capacity.
- High productivity: all goods movements are automated (transfer cars, motor-driven shuttles and conveyors move the pallets to the corresponding location).
- Real-time inventory: the warehouse management system (WMS) strictly monitors the goods, from their arrival at the facility through to their dispatch. As a result, product traceability is extremely precise.
- Cost reductions: although the initial outlay is higher than that of a traditional warehouse, the return on investment is faster thanks to the durability of the automated handling equipment, the increased productivity and the lower energy and maintenance costs.
Traceability as a priority
Product traceability is a must in the food sector: the main priority for these companies is to maintain food safety in all the stages the products go through before being delivered to customers.
The Easy WMS warehouse management system provides this traceability, identifying the goods from the moment they arrive at the facility and in the different phases they undergo until they are dispatched. The WMS monitors every movement the pallet makes, including its transfer to the pick station if required.
In addition to strictly controlling the goods movements in real time, Easy WMS provides detailed information on the products. This can be very helpful for consumers (e.g., quality controls passed). To ramp up throughput in all operations, Easy WMS had to coordinate and be integrated with Cabezuelo Foods’ ERP system.
The two software programs exchange data and information on how to carry out the various processes in the facility. For example, when the ERP system receives an order from a customer, it notifies Easy WMS so that it can be prepared immediately.
Quality and customer satisfaction
The success enjoyed by Cabezuelo Foods over the past few years lies in its commitment to customer satisfaction. Its top priorities are to guarantee the quality of the food it sells and to make timely deliveries.The firm now has a comprehensive logistics solution that will enable it to confidently face its future prospects. “In 2020, we suffered a setback as a result of the COVID-19 pandemic. This is because 80% of our customers are in the service industry, one of the hardest hit due to the restrictions. We know that our 2021 results won’t match our pre-pandemic earnings, but the outlook for 2022 is very positive. We trust this technology will help us to boost our business,” says the company owner.
We’re very happy with the automated Pallet Shuttle system with transfer cars. It makes the most of all the space in our warehouse and allows us to grow without any limitations. What’s more, by enhancing our operations, we’ve increased our speed in entries, exits and order prep.
Advantages for Cabezuelo Foods
- Stock control: automation and Easy WMS ensure strict control of the goods to preserve the quality of the food stored at a refrigerated temperature.
- Space optimisation: Cabezuelo Foods has centralised all its logistics operations in a single facility with capacity for 5,104 pallets, enough to cope with the rise in production.
- Energy savings: by effectively leveraging the available surface area with the installation of a compact storage system, energy consumption for cooling is reduced.
- Automated picking: the automated Pallet Shuttle system with transfer cars, coupled with the anthropomorphic robot, speeds up order prep tasks, making it possible to prepare up to 150 pallets a day.
Automatic clad-rack warehouse | |
---|---|
Storage capacity: | 5,104 pallets |
Warehouse height: | 28 m |
Warehouse length: | 54 m |
Temperature: | -25 ºC |
Gallery
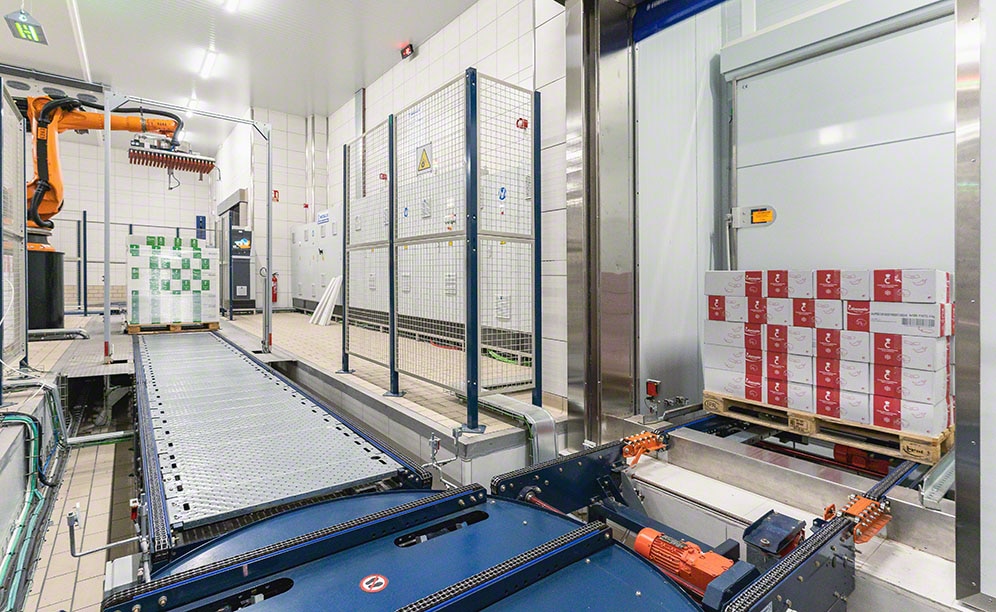
Cabezuelo Foods' facility with the Pallet Shuttle with transfer cars
Ask an expert