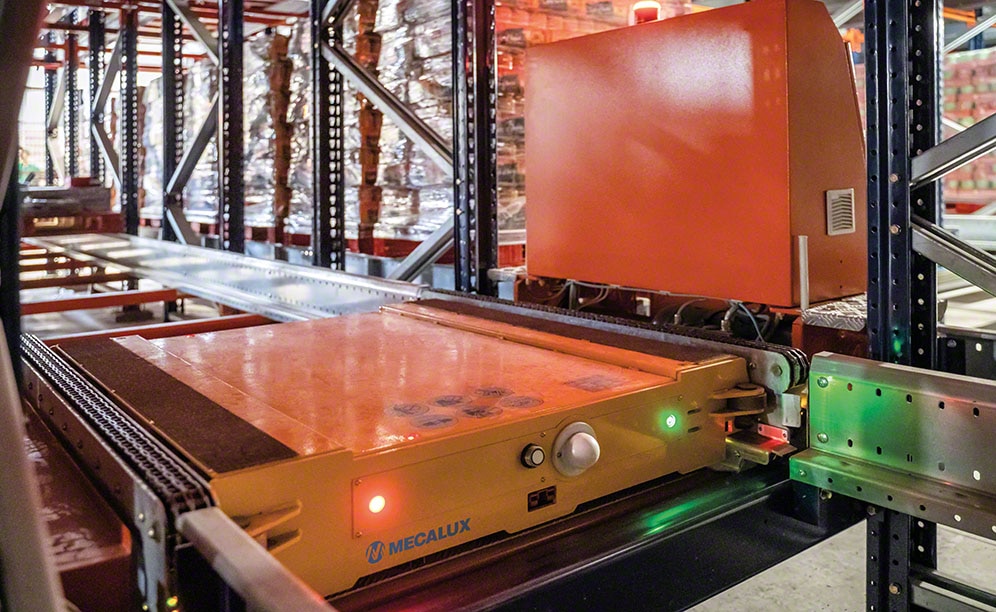
Efficient management of canned vegetables from Cistér with a new warehouse
Mecalux has installed the automatic Pallet Shuttle system with transfer cars in the Cistér warehouse in Portugal

Cistér, a Portuguese producer of pulses, has decided to automate its logistics processes to modernise and improve its supply chain. With the collaboration of Mecalux, the firm has set up the automatic Pallet Shuttle system with transfer cars in its new warehouse in Alcobaça (Portugal). The storage capacity is 12,672 pallets. The warehouse, connected to the production plant via a conveyor circuit, is managed by Easy WMS.
Highly nutritious pulses
Cistér is a Portuguese company that is part of the Raimundo & Maia food group. This division, founded in 1999 and dedicated to the production of pulses, brings together enormous knowledge of the market and of these foods.
One of the company’s priorities is to ensure that the points of sale always have pulses in stock; to this end, it has equipped its production centre in Alcobaça (north of Lisbon) with the latest technology. It is, thus, able to adapt its activity to market fluctuations such as, for example, occasional increases in demand.
Pulses are one of the staples of a healthy diet and are consumed throughout the year. For Cistér, this translates into a very demanding production rate due to the increase in sales in recent years.
From a logistics point of view, the increase in production makes it necessary to expand storage capacity to accommodate all products. The company wanted to solve this problem once and for all and was looking for a system that would allow it to manage large production runs of a single SKU. It also wished to speed up the dispatch of goods, given that the volume of orders, especially exports, continues to rise.
“The production centre produces around 600 pallets a day, which are then sent to customers. This generates a lot of movements that the operators had to make with forklifts, which could potentially lead to errors and accidental damage to the products,” explains Pedro Maia, director of Cistér.
The company tendered a project to improve its logistics centre and, after considering offers from various storage solution suppliers, opted for Mecalux. “One of the reasons we chose Mecalux is that their sales reps invited us to visit their 6,500 m² technological centre in Barcelona, where they showed us their proposal: the automatic Pallet Shuttle system with transfer cars. Seeing the system at work convinced us,” says the director.
It is ideal for optimising space and increasing capacity. In addition, a fully automated operation ensures a constant flow of entries and exits. “Mecalux is the supplier with the most experience in this type of solution. We are very satisfied with the system we have installed because it allows us to move a large number of pallets,” Maia points out.
Flexible supply chain
The 600 pallets that leave production daily can be directed to one of two destinations: to the manual order fulfilment area next to the production centre, or to the automated warehouse located on another site. The two buildings are connected by a conveyor platform that automatically transports the products safely to the warehouse.
The automated warehouse consists of two racking units that take full advantage of the entire surface area (71 m long and 19 m high, with nine levels) to provide a storage capacity of 12,672 pallets. The channels support between eight and twenty-four pallets in depth. At each level, a transfer car serves the storage channels. It is equipped with a motorised shuttle that moves inside the channels, inserting or removing the goods.
“Although the installation has been operational only for a short period of time, we have already seen the advantages provided to us by this storage system. Not only have we increased capacity, but also the number of cycles,” stresses Pedro Maia.
The Pallet Shuttle system with transfer cars multiplies cycles/hour by the number of levels in the warehouse (nine in this case). Each transfer car can carry out 20 combined cycles/hour (20 incoming pallets and 20 outgoing pallets). Two pallet lifts have also been installed, one for entries and the other for exits, and these connect the levels. While operations could be carried out with a single pallet lift, with two, the number of cycles has been doubled.
Taking Cistér’s growth prospects into account, the warehouse design has a future expansion factored in. Whenever the company so requests, two more racking units will be added to accommodate 10,000 more pallets and two additional pallet lifts.
Advantages of the automatic Pallet Shuttle
The automatic Pallet Shuttle is one of the most efficient high-density storage systems on the market, guaranteeing a very high flow of incoming and outgoing goods. The automation of this system is carried out by incorporating stacker cranes or transfer cars that move the products to the corresponding slot.
This solution has many advantages:
- Elimination of errors that occur as a result of manual management.
- Increased number of pallet cycles/hour.
- The use of stacker cranes or transfer cars requires a smaller width between aisles, so the area dedicated to storage is larger.
- The supercapacitors of the electric shuttle are charged while they are on board the stacker crane or transfer car.
- High availability of goods.
- Assembly in phases, implementing automation in different stages as the needs of the company change.
- The features offered by automated warehouses with Pallet Shuttle compensate for the initial investment with a quick return on investment.
Large dispatch area
The dispatch area is one of the warehouse’s most active areas: about 600 pallets are shipped daily to Cistér’s customers in Portugal. This area has been specifically designed to facilitate the distribution of goods and minimise any possibility of error.
Two transfer cars organise the pallets and sort them into 19 live preload channels depending on the order or route. The pallets remain in these channels, waiting for the operators to load them into the lorries.
Each live channel has enough depth for ten pallets. Three channels together fully load a lorry that has previously been assigned a dock. These channels are slightly inclined, and the pallets are moved by gravity from the highest to the lowest part (which faces the docks).
Product oversight
Previously, Cistér managed its inventory with the company’s ERP. With that software, however, it was impossible to know the exact location of the products in real time, something considered essential to manage the business.
In order to make the most of all the warehouse features, Mecalux has implemented the Easy WMS management system. The reason is clear: “to streamline the storage and dispatch of pallets, have a strict and controlled organisation of the stock, manage the goods based on their date of manufacture and increase the number of orders,” notes Pedro Maia.
As a fully automated warehouse, Easy WMS incorporates the Galileo module, responsible for giving movement orders to conveyors, transfer cars and pallet lifts.
One of Cistér’s priorities was to integrate the WMS with its ERP. The two systems communicate continuously to ensure operations are running smoothly and to coordinate the movement of goods from the time they leave production and arrive at the warehouse until they are prepared for distribution to customers.
The WMS intervenes in each of the warehouse processes:
Receipt of goods
All products arrive stretch wrapped and labelled from production. The WMS identifies them when they cross the checkpoint, where it is validated that the pallets comply with the requirements established for their slotting in the warehouse.
Product storage
Once the WMS identifies the pallets that have arrived from production, it makes a series of calculations, taking into account the number of empty slots, the SKU and the level of demand in order to assign a place to each item. Thus, for example, the products with the most sales are deposited near the pallet lifts so that their entry and exit is more agile.
In addition, the WMS also follows the FIFO criterion when dispatching goods, so the first products inserted are those that are dispatched first.
Easy WMS speeds up the entry and exit of goods through the correct organisation of products and optimisation of the movements of automated equipment (transfer cars, pallet lifts and conveyors).
Manual order preparation
Easy WMS tells operators how to prepare about 50 orders per day without delay. The WMS has designed a route that optimises operators’ movements when grouping the SKUs that comprise each order. Through radiofrequency terminals, the WMS tells operators which products to collect, in what quantity and where to locate them.
Employees communicate with Easy WMS via these terminals to receive orders and confirm their fulfilment. This WMS supervision reduces mistakes in the picking process.
Dispatch of goods
The ERP assigns a dock to a set of live channels; then, Easy WMS plans which orders will be distributed on that lorry and orders the pallets to be shipped to the dispatch area.
The optimal organisation of the dispatch area also contributes to faster and more error-free distribution of products.
Compact storage system with high throughput
Cistér has decided to improve its customer service and cope with the increase in production with the help of a new automated warehouse in Alcobaça, equipped with high-density racks with the automatic Pallet Shuttle system and transfer cars. This solution accommodates more than 12,600 pallets and provides speedy goods flows.
The company has taken advantage of the benefits of automation and compacting to modernise its logistics. Cistér now has a flexible supply chain ready to meet the challenges they face.
Pedro Maia - Cistér Director
“The design of the warehouse was a long and complex process. However, the result is very satisfactory because we coordinate production with all processes, and all operations (mainly warehousing and shipping) are fluid.”
Advantages for Cistér
- Capacity for 12,672 pallets: with this figure, Cistér can smoothly tackle the increase in production. Space has also been reserved for future expansion.
- 24/7 operation: the Pallet Shuttle with transfer cars guarantees the uninterrupted movement of around 180 pallets/hour with minimal operator intervention.
- Control of goods: all items are identified from the moment they arrive at the warehouse. Thus, the company knows the status of the pallets in real time.
Automated warehouse of Cistér | |
---|---|
Storage capacity: | 12,672 pallets |
Pallet sizes: | 800 / 1,000 x 1,200 mm |
Max. pallet weight: | 1,025 kg |
Racking height: | 19 m |
Racking length: | 71 m |
No. of automatic shuttles: | 9 |
Gallery
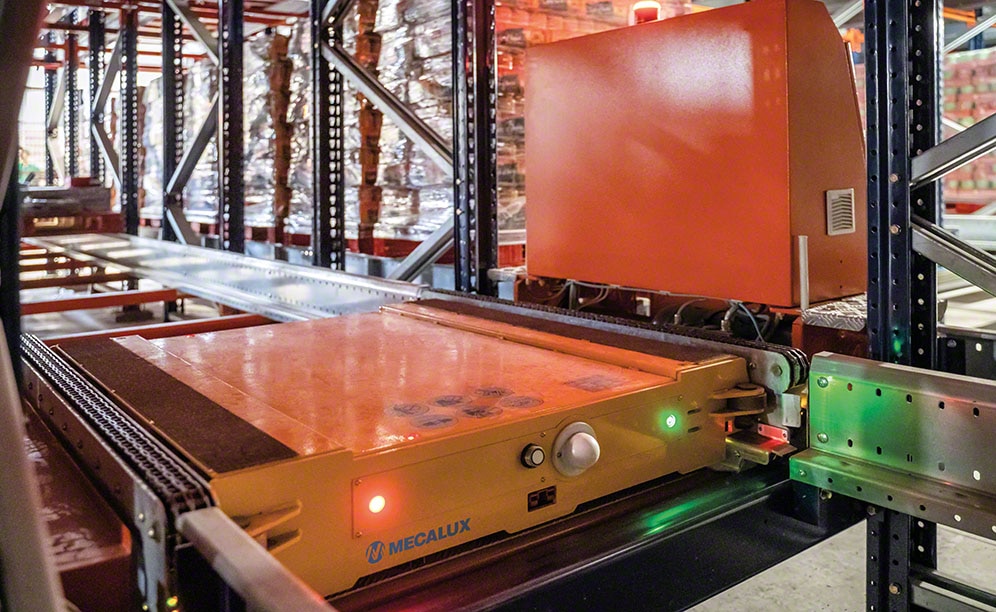
Pallet Shuttle with transfer cars at the Cistér warehouse in Portugal
Ask an expert