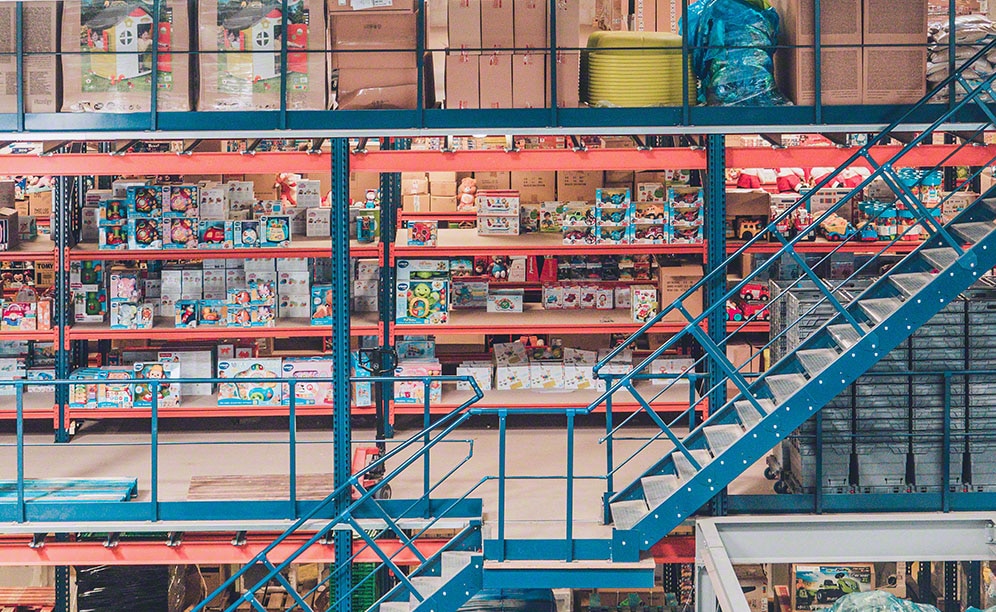
E.Leclerc: four warehouses for picking 110,000 SKUs
The warehouse manages products to be sent to hypermarkets, items to be sold online, and books
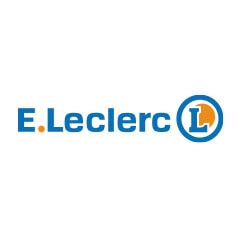
Supermarket chain E.Leclerc has revamped its installations in Tourlaville (France) with the aim of expanding its storage capacity and optimising order prep. In addition to conveyors, Mecalux has installed pallet racks, picking shelves with walkways, and a mezzanine floor, making the most of the available surface area. These systems have been set up to store 50,000 SKUs of products to be sent to hypermarkets, 45,000 SKUs of items related to culture, such as books, and 12,000 SKUs of goods to be sold online. All of these solutions provide direct access to the products, which is essential for quick order prep.
Who is E.Leclerc?
The company started its activities in 1940, when Edouard Leclerc opened a convenience shop in the town of Landerneau (France). His objective was to sell everyday goods (mainly food, cleaning products and alcoholic beverages) at a reasonable price.
E.Leclerc has steadily grown and currently has a presence in six other European countries: Spain, Italy, Poland, Portugal, Slovenia and Andorra. This supermarket chain has 10,000 employees and numerous warehouses, hypermarkets, supermarkets and specialised shops from which it distributes goods.
The drive model
Businesses are offering more and more options to facilitate their customers’ purchases. One of the most widely used methods in many European countries is known as the drive model. With this system, customers make their purchases online. They then choose whether they prefer to receive the products at home or pick them up at the supermarket of their choice without getting out of the car.
E.Leclerc is one of the pioneering companies in setting up this system in France and is expanding it to the other countries in which it operates. The firm has installations in the town of Tourlaville (Normandy, France); from there, it markets its products to its customers all over the north of the country. The company’s four warehouses in Tourlaville comprise a total surface area of 3,000 m2.
E.Leclerc sought Mecalux’s cooperation when fitting out its installations because they had worked together in the past. According to E.Leclerc CEO Philippe Bataille, “we knew perfectly well that we would turn to Mecalux once again to drive this project forward.”
E.Leclerc’s priorities were crystal clear; we needed to store more goods and, ultimately, optimise our storage space,” explains Bataille. The warehouse design had to help manage the myriad of SKUs with the firm works, such as food products (fresh, frozen and room-temperature) and toys.
In addition, it should be noted that order prep is the main operation carried out at the four installations; the warehouse design, therefore, had to facilitate and streamline picking as much as possible.
Leveraging every nook and cranny
Mecalux has equipped the four installations with picking shelves with walkways, pallet racking, and mezzanine floor. On the one hand, these solutions maximise the surface area and height of the buildings to provide the greatest possible storage capacity; on the other hand, they aid in order prep. “We chose them for their practicality,” points out Philippe Bataille.
The racks measure between six and eight m high (depending on the height of each warehouse). Fitted to the racks are walkways or raised aisles that form up to a maximum of two additional levels above the ground level.
The installations are divided into several zones. This means that each of the levels corresponds to a distinct area and is assigned specific products and a number of operators to carry out picking. This can vary depending on demand and the amount of orders to be prepared.
Operators move up and down the aisles, locating the items that make up each order. They follow an order grouping method, which consists of picking SKUs for several orders on the same run. Then, in the consolidation area, the products comprising each order are separated, sorted, verified, packed and shipped.
Replenishment is carried out during offpeak hours, i.e., when there are fewer orders to prepare.
Mecalux has also installed a conveyor for boxes that connects the various floors of the warehouse. This transport system minimises operator movements; that is, workers do not have to go all around the installation to select the items for each order but rather can remain in the area assigned to them.
Philippe Bataille - CEO of E.Leclerc
“We are extremely satisfied with the installations in Tourlaville. Because of them, we have cut costs and gained in productivity. In fact, we were initially considering moving to a bigger warehouse; after optimising the space we already had, though, we were able to stay in the same place.”
Systems that speed up picking
The racking in the four warehouses — for both pallets and picking — stands out for its accessibility, which facilitates goods handling and helps operators to quickly remove products from the shelves.
This accessibility also comes in handy when locating SKUs. Each location is allocated to a single product, optimising goods management and minimising errors.
E.Leclerc manages approximately 110,000 distinct SKUs. The racks are equipped with add-ons and accessories to deposit all the products of varying sizes, characteristics and turnover.
Advantages for E.Leclerc
- Maximum use of surface area: the storage solutions implemented by Mecalux optimise every available millimetre to manage close to 110,000 SKUs for E.Leclerc’s hypermarkets, online sales and entertainment/multimedia items.
- Efficient picking: the distribution of goods, taking into account their characteristics and demand level, optimises operator movements and speeds up order prep as much as possible.
- Optimal product management: the racks provide direct access to the goods and enable products to be classified by size and turnover.
Gallery
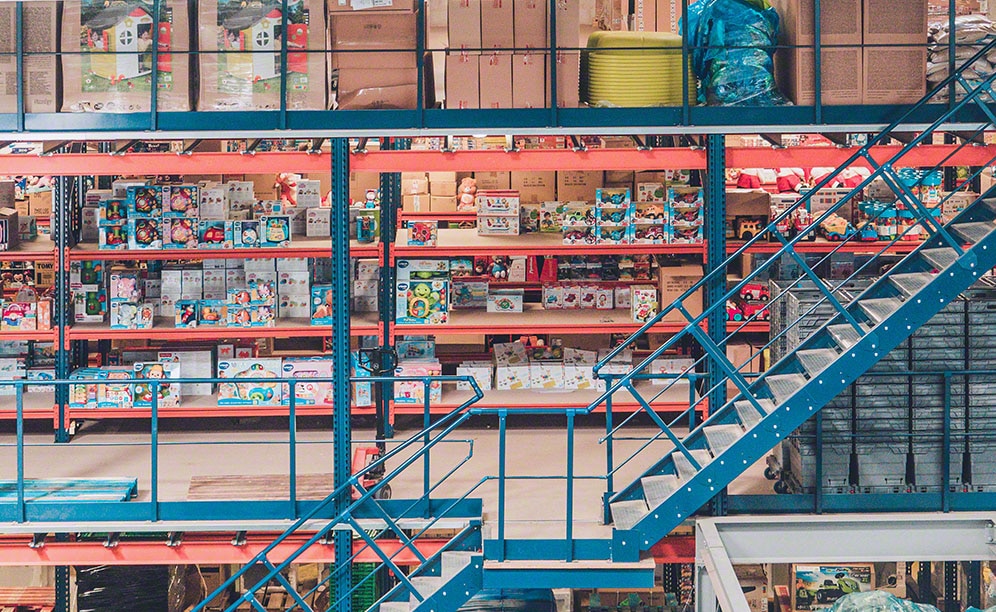
Warehouse with various storage systems for E.Leclerc's supermarkets
Ask an expert