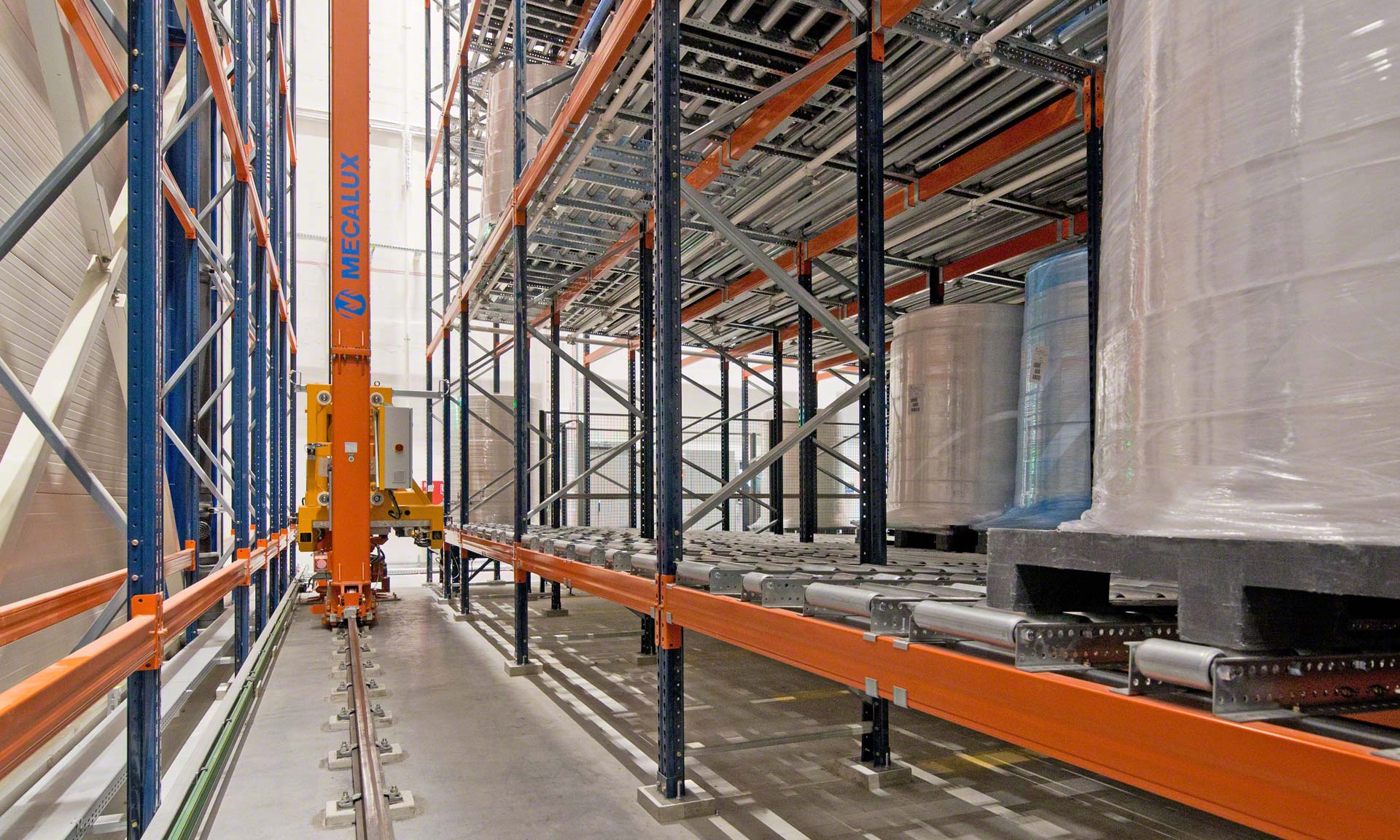
EcoWipes: automated logistics, 30% jump in productivity
The Mecalux systems have enabled EcoWipes to increase productivity by 30%
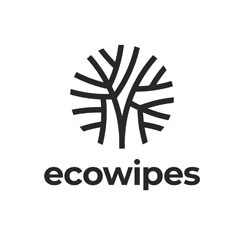
Cosmetic and hygiene product manufacturer EcoWipes has connected its warehouse in Poland with its production lines automatically via conveyors. It has also installed live pallet racking with a stacker crane and Movirack mobile pallet racking to optimise its storage space.
EcoWipes: sustainable and environmentally friendly cosmetics
The business philosophy and production technologies of EcoWipes, a company specialising in the manufacture of cosmetic and hygiene products, are rooted in ecological sustainability and respect for the environment. The company began marketing its products in Poland, then in Europe, and they can be found today in such competitive markets as the US.
- Founded in 2011.
- European leader in the manufacture of wet wipes and cotton pads.
- Present in Europe and the US.
- Natural and environmentally friendly products.
THE CHALLENGE
|
THE SOLUTIONS
|
THE BENEFITS
|
---|
Increased sales have forced businesses to step up production rates and, in most cases, to transform their logistics processes in order to guarantee quality service. To that end, EcoWipes acquired French company Hydra Cosmetics, thereby strengthening its European expansion strategy. To take on this challenge, the company has started up a new production line in its plant in Nowy Dwór Mazowiecki (Poland) and has optimised its supply chain through automation.
“By putting the new production line into operation, we realised that our storage capacity was limited; we needed more space to store our semi-finished products and raw materials. We were looking for a solution that would take advantage of the available surface area to house 1,800 SKUs,” says Michał Kulczyński, Director of Logistics at EcoWipes.
At that time, the company had a manually run warehouse located in the production centre itself. However, with the rapid growth caused by the increase in orders, it made the decision to build a new facility that would meet its rising demand.
With the opening of this new warehouse, EcoWipes took the opportunity to renovate all its logistics operations, implementing automated systems to boost efficiency in storage processes.
When the time came to drive this project forward, EcoWipes contacted Mecalux “because of its extensive experience in designing warehousing solutions for leading companies in the industry, its attractive offer and its team’s professional approach,” says Kulczyński.
The comprehensive solution installed by Mecalux includes live pallet racking served by a stacker crane, Movirack mobile pallet racks, and pallet conveyors and lifts that connect the production lines with the storage areas.
Warehouse connected to production
Two-way communication between the warehouse and the production lines is essential in EcoWipes’ day-to-day to ensure the availability of the materials required in production.
The installation of pallet conveyor systems has brought a host of benefits for the company. Kulczyński says: “The conveyors have significantly shortened the time used to carry out logistics operations such as production supply and the receipt of products from the production lines. Operator travel has been minimised, so safety has also been improved, since fewer forklifts are driven around the facility. Thanks to the conveyors, we’ve completely done away with interruptions on the production lines due to the lack of raw materials.”
The Mecalux technical team encountered an added difficulty when installing the conveyors: a busy street separates one of the warehouses from the production plant. The solution for connecting the two areas consisted of building an elevated, covered bridge accessed by the pallets via a lift. Two conveyor lines are set up on the covered bridge. One moves the pallets in a single direction (from the warehouse to production), while the other is two-way.
Storage space optimisation
Mecalux has equipped EcoWipes’ storage area with live pallet racking with a stacker crane and Movirack pallet racks. Both solutions share a common denominator: they leverage the available floor space to house the largest number of products possible. “We’re thrilled with the efficient use we make of the space with the new storage systems.” The company receives 1,200 pallets every day from the production lines or sent by suppliers. Depending on their characteristics and demand level, it deposits them on the live pallet racking or the Movirack racks.
The live pallet racking with a stacker crane stores the raw materials with the highest demand. This automated solution speeds up goods inflows and outflows: the pallets cross the bridge and arrive at the warehouse. A stacker crane then picks them up and inserts them into the corresponding location automatically.
The automation of operations has enabled EcoWipes to achieve the throughput it sought. The stacker crane travels down a 54-metre-long aisle non-stop, placing the pallets in the assigned locations as quickly as possible. The advantage of this solution is evident: “We’ve eliminated errors, in addition to saving time and money,” says Kulczyński.
The live pallet racking facilitates goods management according to the FIFO (first in, first out) method, whereby the first pallet inserted is the first removed. This ensures optimal turnover of the stock and avoids interference in goods entries and exits.
Mecalux also installed Movirack mobile pallet racking, a compact storage system that makes the most of the warehouse space to expand capacity while maintaining direct access to the products. As the racks are on mobile bases, they move sideways when the operator selects the aisle they wish to access via the remote control. This enables them to reach the racking location from which they need to extract or deposit the products.
Ever-expanding
From the beginning, EcoWipes has developed innovative, technologically advanced solutions to provide environmentally friendly alternatives that eliminate plastic from cosmetic and hygiene products.
EcoWipes’ production pace has increased every year, even during the coronavirus pandemic. Kulczyński says: “As a result of the outbreak, the number of orders to prepare rose by 20%.”
The company also stands out for its firm commitment to society. This is evidenced by the fact that during the COVID-19 pandemic, EcoWipes donated the material needed to manufacture the protective masks used by healthcare workers in Poland.
To satisfy the growing demand for its products, EcoWipes constantly updates its logistics facilities in Poland, making use of automated systems that boost and optimise their operational throughput.
“We aim to continue investing in our plant in Nowy Dwór Mazowiecki and implementing modern, green solutions,” says Kulczyński.
We’re really happy with the storage systems and the pallet conveyors from Mecalux because they’ve optimised our logistics processes. We’ve improved our responsiveness and ramped up our productivity by 30%. Moreover, all the Mecalux solutions have had a positive impact on the safety of our employees.
Flow racks with stacker crane | |
---|---|
Storage capacity: | 2,240 pallets |
Pallet size: | 800 x 1,200 mm |
Max. pallet weight: | 600 kg |
Rack height: | 12.8 m |
Rack length: | 54.8 m |
Gallery
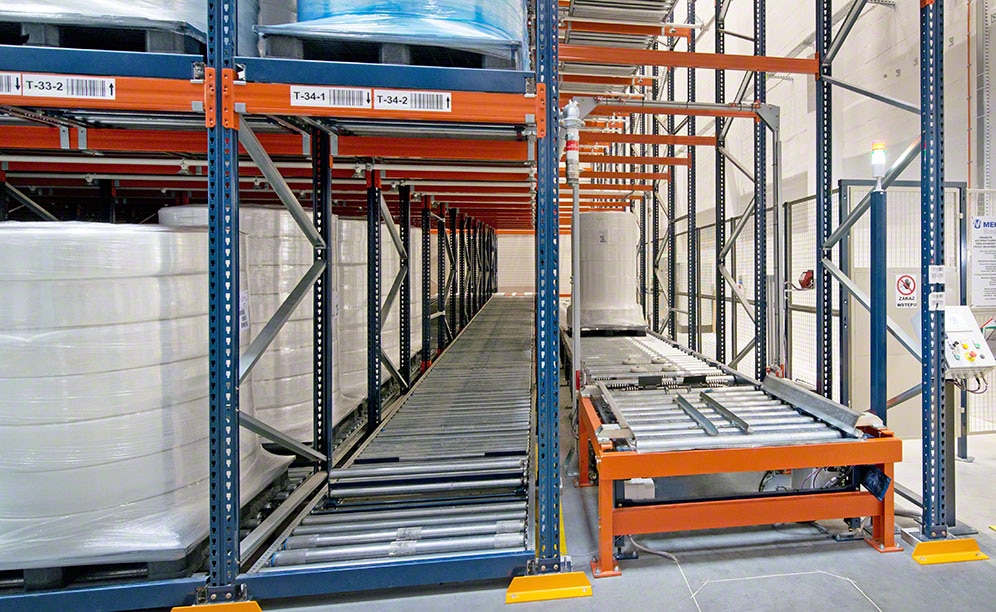
The conveyors connect EcoWipes' warehouse with its production lines
Ask an expert