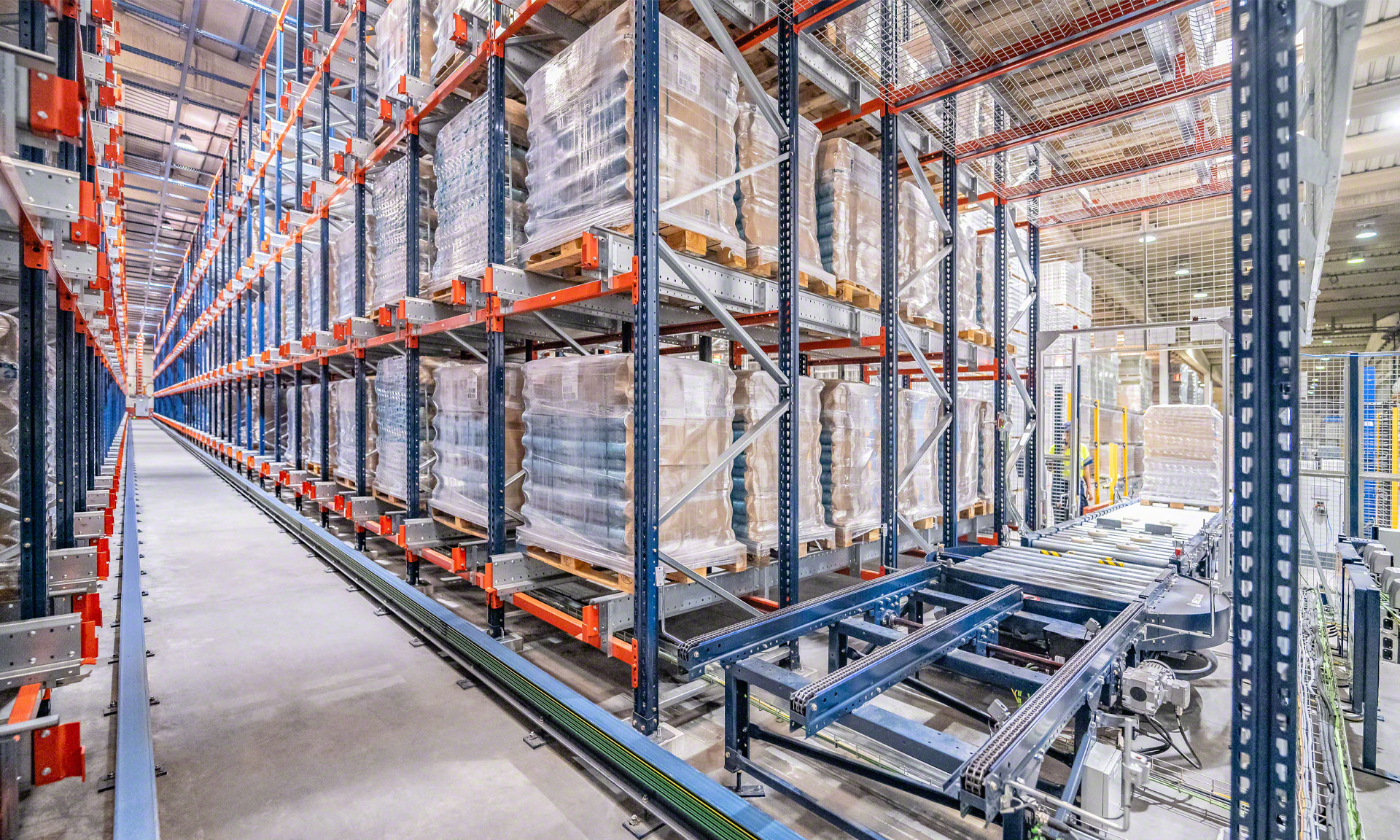
Envases Group automates its facility for tinplate lids from production
Envases Group, a global packaging solutions leader, automates storage and digitalises finished product management.
The tinplate lid manufacturer Envases Group automates its warehouse with the automated Pallet Shuttle and software from Mecalux. The company has optimised its available space to maximise storage capacity in a limited area: 3,196 pallets in just over 1,400 m².
Envases Group: worldwide supplier
The Envases Group is a global leader in packaging solutions and one of the most prominent companies in Mexico, where it operates in over 30 production facilities. The business offers a wide array of packaging products, from bottles and jars through to lids and caps. Its merchandise is designed to meet the packaging needs of its customers in sectors such as the food and chemical industries. With a presence in the Americas, Europe and Asia, the Envases Group has 84 manufacturing centres and a professional team of over 3,000 people.
CHALLENGES
|
SOLUTIONS
|
BENEFITS
|
---|
For manufacturing supply chains, the key to success lies in optimising finished product storage and guaranteeing prompt goods distribution whenever customers place an order. In La Rioja (Spain), the Envases Group produces and sells tinplate lids for businesses in the food sector.
The organisation — which markets its products in Spain under the name Envases Universales Ibérica — is currently engaged in a comprehensive digitalisation and automation process. Its goal is to provide better service to customers and ensure the highest product quality. For the Envases Group, logistics is a fundamental stage in the machinery of the business. Speed and efficiency in warehouse operations are two inseparable requirements for the organisation, particularly as its production pace continues to increase.
Jesús Unzueta, Vice President Cluster South, explains what prompted the company to overhaul its facility: “Before, our goods were stacked directly on the floor. So we were looking for a system that would offer better performance in all aspects, from enhanced productivity to optimal space utilisation.”
The business took advantage of the warehouse renovation to digitalise its operations. “As the pace of work ramped up, we realised we needed software capable of improving the throughput of our logistics operations. We wanted a system that would provide us with more control and higher-quality information,” says Unzueta.
After weighing several solutions, the company contacted Mecalux to install the Automated Pallet Shuttle served by a stacker crane. This high-density automated storage and retrieval system (AS/RS) has boosted efficiency in the Envases Group facility. In addition to making the most of its floor space to expand storage capacity, the company has leveraged automation to streamline and maintain stricter control over incoming and outgoing goods.
“We opted for an AS/RS since we wanted to upgrade our logistics processes. Automation increases productivity in our warehouse by reducing operator forklift movements and thus operation times. We’re extremely pleased with the result: we’ve maximised space and improved accessibility to each SKU stored,” says Unzueta.
The Envases Group has also implemented the Easy WMS warehouse management system. This software is responsible for monitoring the broad range of SKUs in stock as well as goods movements made in the centre prior to shipping. The system distributes tinplate lids throughout the facility according to SKU type, characteristics and turnover rate. “The greatest advantage of this solution is that our logistics processes are now fully automated,” says Unzueta.
Easy WMS continuously communicates with the Envases Group’s SAP ERP system to optimise product management and warehouse processes efficiency. “We’re thrilled with the software. By integrating it with our ERP system, we can track all stock-related information,” says Unzueta.
Automatic storage of tinplate lids
“The AS/RS has brought our logistics processes numerous advantages. Among them, I’d highlight raised productivity, reduced errors, improved safety and faster, more rigorous inventory control,” says Unzueta.
The AS/RS consists of a single 76–metre-long aisle with double-deep racking on both sides. The racks stand 7.5 m high and have four levels. They can store six pallets deep on one side of the aisle and 11 on the other. The racking maximises storage space by obtaining the highest possible capacity: 3,196 pallets in little over 1,400 m².
The Pallet Shuttle is a fully automated high-density system. It features a motorised shuttle that moves pallets inside the storage channels with complete autonomy. “Every day, we receive and ship around 160 pallets,” says Unzueta. A stacker crane for pallets transports goods from the AS/RS entry point to the storage channel assigned by Mecalux’s Easy WMS.
Warehouse and production fully controlled
One of the Envases Group’s priorities was for the WMS software to integrate with the SAP ERP system. The two programs communicate with each other to ensure that operations run smoothly. For instance, they coordinate movements of merchandise from production to the logistics facility and during the preparation of orders subsequently distributed to customers. “With digitalisation, we’ve optimised all putaway, picking and inventory management processes,” says Unzueta.
The ERP system notifies Easy WMS in advance of the tinplate lids scheduled to arrive at the warehouse from production. This way, it can assign them a location more quickly. Products arrive from the manufacturing centre stretch-wrapped and labelled. Easy WMS identifies the pallets as they cross the checkpoint and verifies whether they meet the requirements established for storage in the AS/RS.
Once the pallets from production are entered into the software, Easy WMS applies an optimal slotting strategy to each one. It does this based on a series of calculations considering the number of empty locations, SKU and demand level.
Digital logistics for Industry 4.0
“By automating and digitalising our operations, we can ensure that, on average, 11 lorries leave our facility with customer orders every day,” says Unzueta.
Logistics is the cornerstone of this global leader in rigid consumer packaging solutions. Thanks to reliable processes, the manufacturing centre can sustain daily production and efficiently fill and distribute orders to its extensive customer network. The new AS/RS provides the necessary storage capacity and throughput to absorb the Envases Group’s high production rate. Digitalising operations with Easy WMS was also pivotal for streamlining goods inflows and outflows. Products are now effectively organised and the automatic equipment moves materials in an agile way.
With this integrated logistics solution from Mecalux, the Envases Group has an optimised supply chain. It can meet customers’ needs efficiently and is well-prepared to tackle the challenges of Industry 4.0.
The AS/RS brings our logistics processes numerous advantages. Among them, I’d highlight raised productivity, reduced errors, improved safety and more rigorous inventory control. Moreover, Easy WMS enables us to track all stock-related information more thoroughly.
Gallery
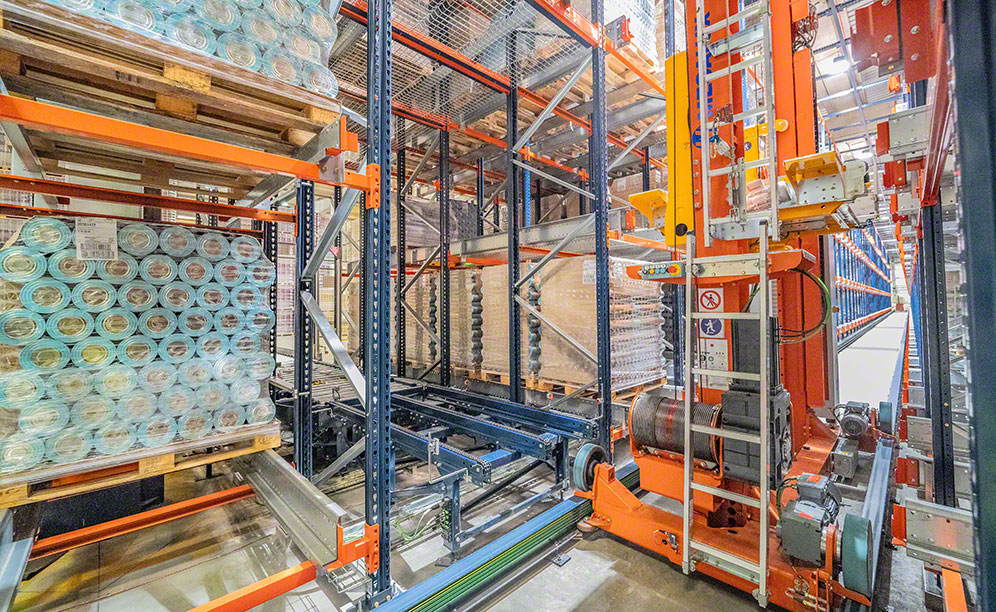
Automated Pallet Shuttle system and stacker crane in the Envases Group warehouse
Ask an expert