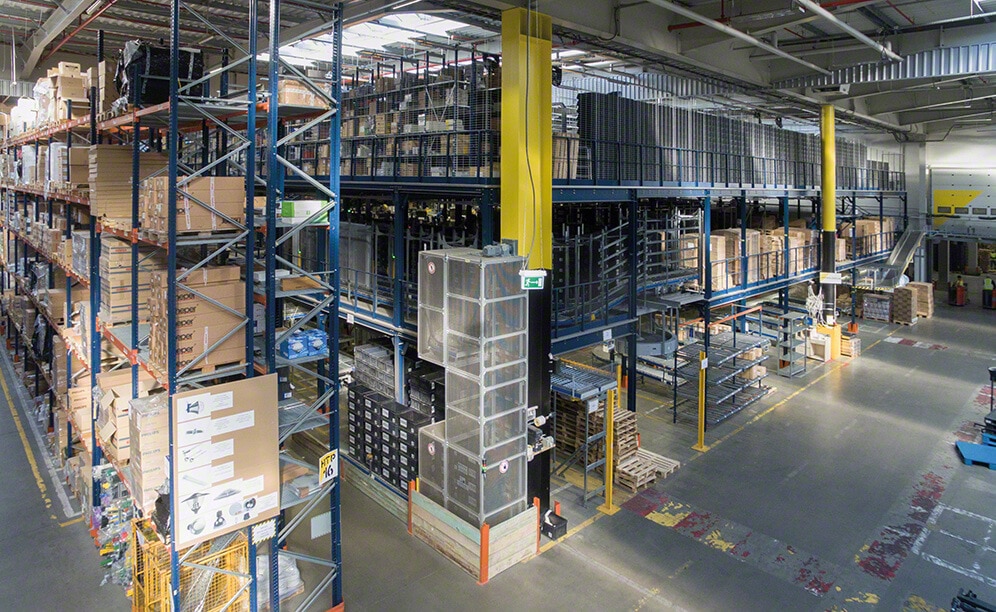
With a 35,000 pallet capacity, the logistics centre of the 3LP service operator and distributor becomes one of the largest, most efficient in Poland
Storage for picking with walkways and conveyors, and pallet racks drive the growth at 3LP
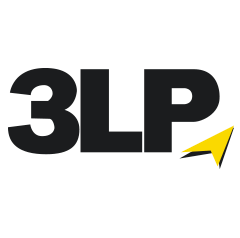
3LP S.A., the logistics operator of the TIM company, has a huge logistics centre in the Polish city of Siechnice with a 35,000 pallet capacity. Here Mecalux has supplied pallet racking, live storage racks, a mezzanine and a picking block with three walkway levels. This close collaboration with TIM-3LP S.A. dates back to 2007, with its first order. Since then, the company has worked alongside Mecalux on multiple occasions.
About 3LP S.A.
3LP S.A. is a logistics and distribution enterprise founded by the TIM company to manage and transport its products and those of other businesses specialised in e-commerce.
TIM is one of the largest distributors of electrical products in Poland. With more than 25 years of experience, the company was a pioneer in the online sale of electrical items, making this its primary source of revenue.
3LP S.A. offers comprehensive distribution support, optimised storage and around-the-clock transport, which guarantees fast, quality service.
The warehouse and its parts
With a total surface area of 40,000 m2, the warehouse 3LP S.A. owns in the city of Siechnice, near Wroclaw, is currently one of the largest and most modern in Poland.
The installation contains a broad range of solutions that fit all types of product and provide a higher storage capacity, as well as faster picking.
The warehouse features:
- Pallet racks
- Automated reel warehouse
- Picking block with three walkway levels served by a conveyor circuit
- A three-level mezzanine
- Consolidation zone and classification of orders from the picking block
- Consolidation and order closing area
- Dispatches
Pallet racks occupy much of the warehouse surface at 3LP S.A. A wide variety of products are stored in them, as well as reels on pallets.
The picking block, with three levels of walkways, is used to pick orders with small, highly consumed parts. A conveyor circuit connects the different floors and the consolidation zone together.
Frontal to the picking block, there is also a three-story mezzanine that joins the picking block through a conveyor circuit. On the ground level, order classification channels have been enabled.
Pallet racking
Pallet racks are set up in five sectors of the 3LP S.A. warehouse. Each sector has been allocated to store different types of products.
In Sector 5, there is an aisle with racks on both sides to store reels on pallets. Along the aisle is a stacker crane responsible for automatically moving the goods from the conveyors to the locations and vice versa.
The two conveyor circuits transfer the pallet with the reel to the area where the unwinding machine and footage control are located. This machine receives and unwinds the reels to cut the metres of product requested for each order. When the process is completed, the partial reel is repalletised and placed on the incoming conveyor, so that the stacker crane can deposit it back in the racks.
The pallet racks installed in Sectors 1, 2, 3 and 4 have an overall capacity for 35,000 pallets filled with a large variety of products in multiple sizes. The distribution of the racking levels has been adapted according to the product and operation. This type of rack is known for its versatility and for offering direct access to all the housed SKUs.
In some aisles, lower rack levels are set up to pick items directly from the pallet, while upper levels store palletised reserve stock.
To carry out storage tasks, operators are assisted by reach trucks capable of operating in aisles that are less than 3 m wide. These machines are ideal for handling the load, and their lift capacity allows them to reach the highest level of the racks.
To carry out picking on lower rack levels, operators work with ground level and high reaching order picking machines. Ground level order pickers deal with items located on the first level of the racks or on the floor. Meanwhile, high reaching order pickers facilitate access to the goods deposited at the higher levels.
As a safety measure, racking uprights have been protected to absorb possible impacts produced by the handling equipment while manoeuvring unit loads.
Consolidation and order closing area
Pallet racking has also been placed in Sector 9, just above the loading docks. Here, pallets warehouse closed orders and those ready to be dispatched.
This zone has a wide area set aside for the classification, consolidation and closure of orders. Operators put together and verify the packing list and shipping labels for orders. Plus, the necessary computer equipment and printers have been provided to complete the operation.
Pallets are grouped on the floor according to whether they correspond to an order, route or outsourced transport. Orders are fully prepared before the lorry is loaded, this way wait times are cut for goods leaving the warehouse.
Live pallet racking in the picking block
An aisle with double-depth live pallet racks has been arranged as part of the picking block. The merchandise stored on these racks is used to supply this picking block with full boxes of consumer products.
This system is based on the same structure as a traditional rack, but with the levels slightly inclined towards the floor and the incorporation of rollers on which the merchandise displaces.
A picking block with walkways
The 72 m long, 36 m wide, 9 m high racking block allows the preparation of high consumption products in three walkway levels, all linked together by a conveyor circuit. Likewise, this circuit crosses each of the floors through the central zone and in front of the live storage racks (forming two prep areas) and moves the merchandise to the consolidation zone.
The operators, working by zones, use the roller tables placed on both sides of the circuit to prepare the orders with the products they collect from the shelves. Once the order is completed, the operator deposits the box in the central circuit so that it reaches the next zone, where another operator will repeat the same process.
Racking levels are made out of perforated shelves that, in addition to having a high load capacity, favour the flow of water in case the fire safety system is activated. Furthermore, vertical side meshing has been attached to the ends of the racks.
Access to the different walkway levels is done via strategically located ladders that prioritise accessibility and maximum safety of both the installation and the operators.
The mezzanine
Sector 7 features a large three-level high mezzanine (including the ground floor) that has been integrated just beyond the picking block, and has tripled the useful surface of the warehouse. This way, the installation's height is fully used to maximise the space available and to gain greater storage capacity.
The conveyor circuit runs to the bottom floor, where the order sorting channels have been arranged. The ramps are on a slight incline that facilitates the gravity flow of orders from the picking block and the mezzanine. Subsequently, they are sent to the order consolidation and closing area in front of the docks to be dispatched.
As in the picking block, operators access each level through stairways, while the open areas are protected by railing that guarantees the safety of operators.
In addition, raised floors have hinged safety doors, an ideal system for creating a forklift loading and unloading area for palletised goods.
Advantages for 3LP S.A.
- High storage capacity: 3LP S.A. can warehouse 35,000 pallets and a lot of boxes with smaller sized items.
- Diversity: installed solutions enable the storage of a wide variety of products of different weights and dimensions.
- Maximum throughput: the 3LP S.A. facility is an example of profitability and efficiency, letting the company increase storage capacity and expedite the preparation of orders.
3LP S.A. logistics centre | |
---|---|
Storage system: | Pallet racking |
Storage system: | Racks for reels |
Storage system: | Live racking |
Storage system: | Picking block with conveyors and walkways |
Storage system: | Mezzanines |
Gallery
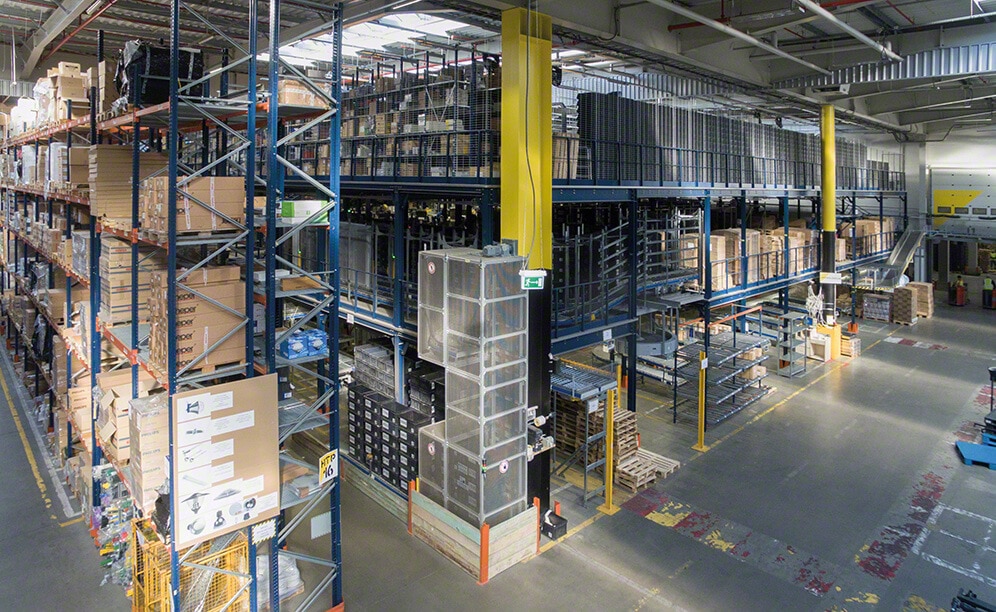
3LP S.A. has a huge logistics centre with a 35,000 pallet capacity. Here Mecalux has supplied pallet racking, live storage racks, a mezzanine and a picking block with three walkway levels
Ask an expert