
A special pallet racking solution sorts out the storage and handling of fabric rolls
A custom pallet racking design for cloth distributor Trivantage
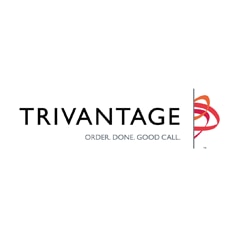
Trivantage had 50,000 fabric rolls in its North Caroline distribution center that it did not know how to store. That was when Interlake Mecalux (IKMX) suggested an innovative, yet simple solution to manage the thousands of fabric rolls housed in the more than 9 m high racking compartments.
Parachutes and pantyhose
The flag that the American astronauts sank into the moon was woven in a North Carolina company called Glen Raven, best-known for making parachutes during World War II or selling the first pantyhose for woman.
As of 1998, Glen Raven merged with several national and foreign companies. Trivantage is one of three business units created through these mergers, and focuses on fabric distribution. Since then, Trivantage is the only national distributor of the fabric Glen Raven produces, and its Mebane distribution center was the first installation in North Carolina to receive the LEED certification (Leadership in Energy & Environmental Design). Each year, the company sources those fabrics wholesale. They divide them into thousands of individual SKUs and distribute them to their chain of distribution branches all over the United States, so that fabrics arrive to the end-customer.
Needs of the company
The Mebane distribution center pursues two separate-but-equal purposes: to replenish product in the eleven branches distributed throughout the country, and to process and ship orders directly from the warehouse.
In order to deal with such a wide range of orders, the Trivantage warehouse not only provides capacity to tens of thousands of fabrics, but it also must be able to locate a particular roll quickly. Typically, if a customer places an order today, they want it tomorrow. This means that its operators cannot afford to spend time rooting around fabric stacks aimlessly hoping to find the necessary product.
Before reorganizing the installation, it would not have been out of the ordinary to find fabric rolls stacked in a compact area ready to be tugged out when needed. This practice left many rolls frayed, dented, with unnatural ridges; essentially destroyed. For that reason, the company was forced to consider alternative methods to improve the storage and location tracking of products.
Discarding options
Many of the companies that do not store rolls on vertical carousels tend to stack the product in a pyramid-style, forcing personnel to move product at the top of the heap in order to reach the products on the bottom.
This handling process wears out the tubes that hold each roll of fabric ― to the point of having to throw them out and buy new ones ― and added to the fire risk by storing flammable fabric in cardboard. With all these disadvantages, the tube solution was completely off the table.
Instead, they requested several metal fabrication shops for ideas. The best idea was a half-moon cradle-type metal pallet that could be made from either steel or aluminum. The idea was good, but the price to manufacture and ship them was unthinkable.
After mulling things over, Trivantage invited IKMX to take a stab at finding a solution to store 50,000 rolls of fabric individually without the damaging stack-and-tug methods traditionally used. The result was not a complicated design, but it turned out to be the most efficient. Ample wooden shelves rest on the frame’s beam, where long rectangular wood pieces create spaces for the fabric to rest on without them rolling to either side. Each shelf is wide enough across to fit ten fabric rolls. The simplest ideas are sometimes the best, enabling the storage of a great amount of fabric rolls and to locate them quickly.
A custom design
Interlake Mecalux had to install 5,000 long-span shelves capable of preventing the bending produced by the weight of the load. At the same time, they were smooth and polished so that the fabric slid over them easily and without fraying.
Considering these premises, average density fiber boards were provided to which rectangular wood strips were attached on top. That way, fabric rolls were separated from each other and the shelves were reinforced to be more resistant to bending.
Given that they do not manufacture fabric rolls in standard lengths ― some are up to 1.5 m wide, whereas others are less than 1.2 m ― turned out to be essential to grouping the articles by lengths and similar weights to create a more efficient storage system and to safeguard the quality of fabrics.
The system was designed and constructed in order to achieve maximum storage density and at the same time maintain the most effective method to locate fabrics.
Automated management
The operations at the Trivantage installation are automated and paperless, because all fabrics are coded in the warehouse management system.
When a certain kind of roll is needed, its code is entered into the computer system and, immediately, the location of the roll is obtained.
It is a very fast process: the article is scanned in its location, it is extracted and the operator can now move onto their next location.
If it was not for the automation implemented, finding fabric rolls in another racking system would be more cumbersome and time-consuming.
Interlake Mecalux understood from the start the importance of product accessibility in the warehouse, especially considering the high turnover of the goods.
Advantages for Trivantage
- Optimal logistics management: the center emphasizes efficient operational organization, with fabric rolls stored on the basis of their volume and characteristics.
- A warehouse model: the applied storage solution has become an example for the rest of the facilities that Trivantage owns.
- Environmental sustainability: the new distribution center permitted lower power consumption and improved air quality.
Cantilever and high-rise pallet racking | |
---|---|
Surface of the installation:: | 9,290 m² |
Special shelves for fabric rolls:: | +5,000 |
Rack height:: | 9.1 m |
Space between rows:: | 45 cm |
Shelf width:: | 1.5 m |
Width of spaces:: | 30 cm |
Average weight per fabric roll:: | 9-14 kg |
Gallery
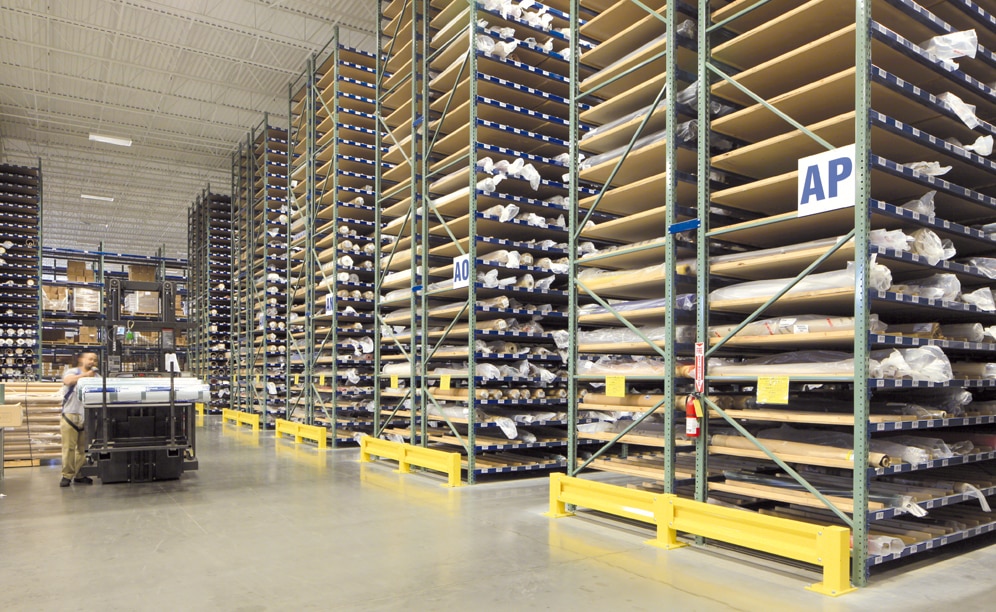
Interlake Mecalux suggested a solution to manage the 50,000 rolls of fabric individually in the 9 m high racking compartments
Ask an expert