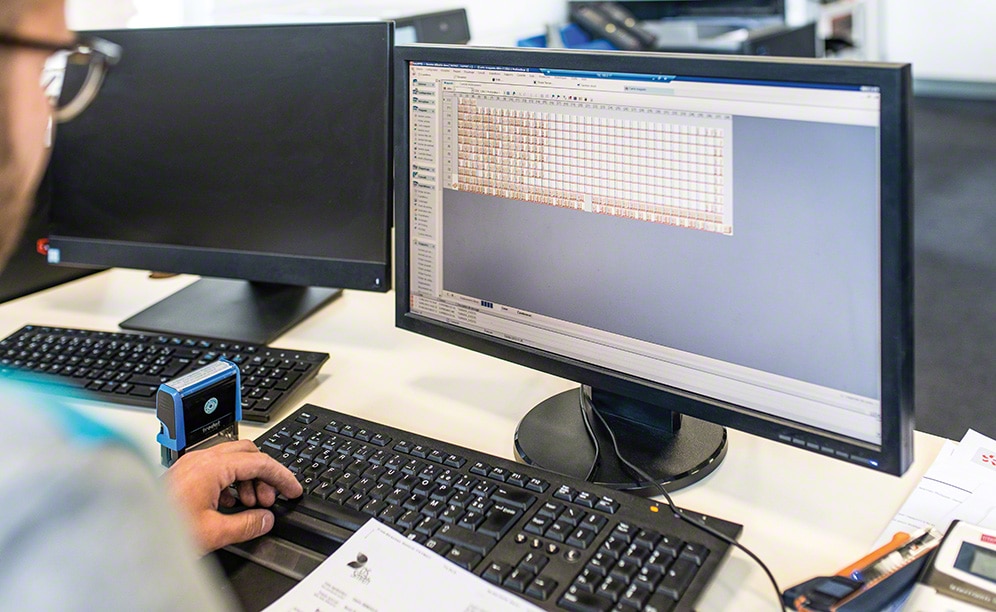
Warehouse in France with fasteners and raw materials of Faynot
Easy WMS identifies the 10,000 SKUs that Faynot manages from the moment they arrive at the warehouse
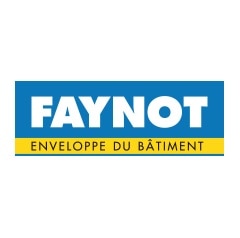
The fastener company Faynot is steadily modernising its logistics with the deployment of Mecalux’s Easy WMS warehouse management system in its three warehouses in France. Through this software, the business can efficiently deal with all 10,000 SKUs in stock, handle the preparation of 200 orders per day and supply the production area with raw materials on time.
The customer comes first
Faynot was founded in 1912 in Thilay (Northern France) and specialises in fixing and cladding components for roofs, walls and facades. It has built an extensive network of authorised dealers to solidify the brand’s presence in more than 30 countries.
The company’s goal is to provide its clientele with the best service. For this reason, the sales reps are on hand with personalised advice and customer care. Likewise, good inventory management is a priority to ensure that orders are dispatched as quickly as possible.
Complex logistics
The company has three warehouses in the Champagne-Ardenne region (in the north-east of France): two of them next to the Thilay production sites and the third in the town of Glaire.
“In our three warehouses we handle around 10,000 separate SKUs,” Faynot managing director, Jean-Edouard Gissinger explained. This figure includes, on the one hand, finished products ready to be distributed (screws and anchors for fixing concrete) and, also, raw materials (wire reels and sheet metal). The products are stored on pallets and in metal containers to facilitate easy handling and transport.
All warehouses are similarly structured and designed to provide the same great service to customers regardless of location. All three are equipped with 9 m high Mecalux pallet racks, split into five or seven shelf levels. An area has also been set aside for warehousing products on the floor (especially reels and bulky items).
Pallet racks were chosen as they provide direct access to products, making it quicker to deal with goods and prepare orders. Moreover, racks can be modified and adapted to product features and sizes (whether boxes or loose parts).
Overall, Faynot’s logistics are very complex because, according to its general manager, “it involves non-stop transfers between the various warehouses, shipments of raw materials to different production processes —like assembly or tinting— and distribution of finished products to customers.”.
Control over the goods becomes essential if one wants to avoid mistakes and ensure that the production centre has the materials it needs at the right time. “Tracking is a decisive issue for us,” Gissinger said.
On top of that, the team prepares 200 orders daily. “The size of orders varies greatly: from a single bag of screws, to an entire lorry load of pallets,” Gissinger noted.
Optimal management of products
The company planned to install a warehouse management system (WMS) to ramp up its three warehouses. “After going over lots of proposals, we felt that Mecalux’s WMS was the system most in line with our expectations, in terms of stock management,” the company’s general manager reported.
Mecalux’s Easy WMS oversees all products and operations in Faynot’s three warehouses because, as Gissinger said, “we wanted to use the same system to manage all our resources at each installation.” Although the three warehouses are very similar, on the surface, the WMS runs each of them quite independently.
Mecalux’s Easy WMS is a very flexible system, which has been adjusted to each installation’s idiosyncrasies in a completely automatic way. “Our top concern was how to track raw materials shipped to production and to process our customers’ orders all in the same space,” said Gissinger.
The WMS guides operators at all times, telling them what to do with each product, thereby reducing any chance of mistakes. Operators use RF devices to receive orders from Easy WMS and, once executed, confirm that the orders have indeed been fulfilled.
Easy WMS also keeps an eye on the real-time status of all products. With this information, it is possible to check whether sufficient raw materials are available to supply the production area, as well as the products required to prep orders requested by customers.
As Jean-Edouard Gissinger pointed out, “the WMS has kept inventory errors down to a minimum.” To achieve this outcome, Easy WMS identifies the products as they arrive at the warehouse and assigns them a location based on their characteristics and demand level. Thus, for example, raw materials are grouped in a certain zone and finished products in another.
Order preparation
Order picking is at the heart of how Faynot runs the three warehouses. On a daily basis, operators walk through each installation locating the items that comprise the 200 orders they need to put together.
Reaching such a high figure requires a WMS that lets operators know which products to take off the shelves and in what quantity. One of the benefits of Easy WMS, on top of that, is that it plots a route to keeps operator travel distances to a minimum when locating goods. Not only is the job of the operators essential but also having reserve goods and avoiding service disruptions.
To do so, the WMS is in permanent synchronised communication with the ERP to prevent stockouts. “So, we can guarantee that the orders our customers place with us are prepped and sent,” the general manager said.
Consolidated growth
Faynot knew unequivocally that to serve its customers well and reach its potential growth, it had to apply flexible, high-tech logistics in its business. Easy WMS’s deployment in its three warehouses marks an enormous leap forward in quality, as the tool directs and streamlines all processes with the aim of delivering better performance.
The Mecalux WMS has significantly increased Faynot’s productivity thanks to sound stock management and a drop in order prep errors. Each process from production to end-customer merchandise deliveries is coordinated with the company’s WMS software-integrated ERP.
Jean-Edouard Gissinger - Managing Director at Faynot
“We installed Mecalux’s Easy WMS in our three warehouses because it is completely flexible with all our operations. This has brought about a host of advantages, including traceability, efficient picking and fewer mistakes.”
Advantages for Faynot
- Product traceability: the WMS identifies the 10,000 SKUs managed by Faynot from the moment they arrive at the warehouse and organises their distribution based on their characteristics and level of demand. The WMS provides real-time identification of the lot number sent to the customer.
- More efficient order picking: Easy WMS steers the operators around each warehouse during the daily preparation of 200 orders. It shows the team what products they need and points them to where to find them.
- Three warehouses managed: the Mecalux system participates in the inner-workings of Faynot’s three warehouses and supplies the production area with raw materials.
Faynot warehouses | |
---|---|
Storage capacity: | 13,000 pallets |
Pallet size: | 800 x 1,200 mm |
Max. pallet weight: | 1,000 kg |
Racking height: | 9 m |
Gallery
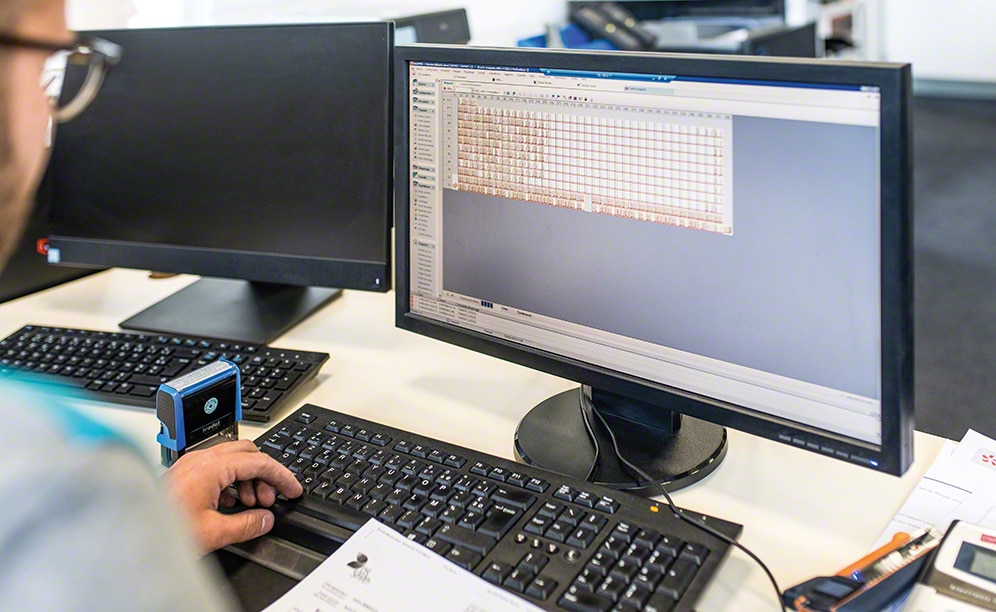
Easy WMS is the WMS that manages all Faynot operations
Ask an expert