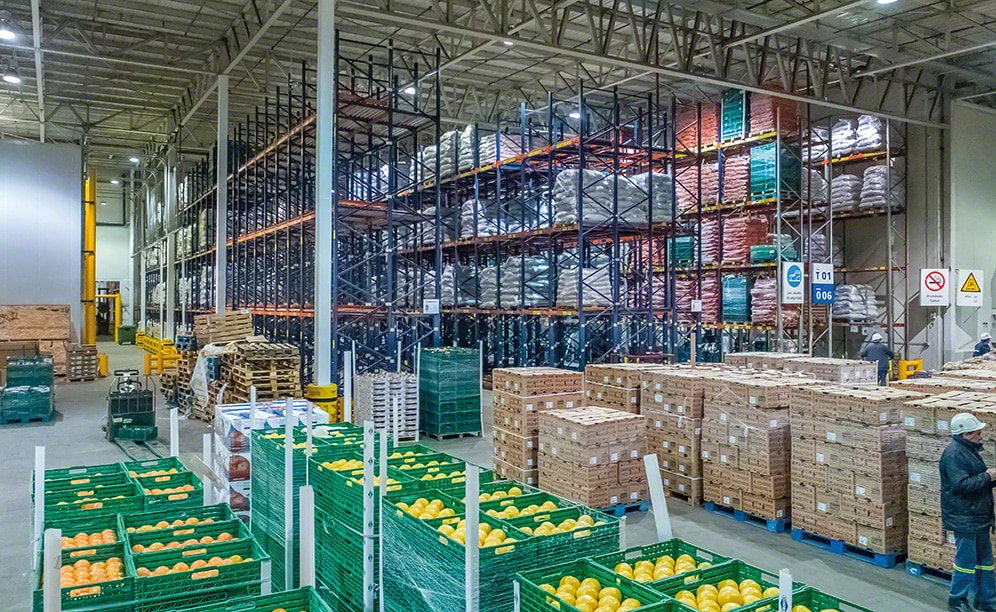
The new fresh fruit, vegetable and greens warehouse of Coto in Argentina
Multiple solutions to manage the fresh fruit, vegetables and greens of Coto in its warehouse
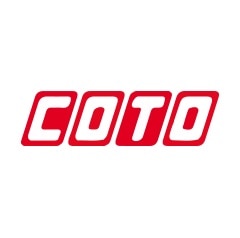
How are fruits and vegetables stored to ensure they are in top condition when they arrive at supermarket shoppers? The Coto supermarket chain has asked for Mecalux’s collaboration to answer this very question, renovating its distribution centre in the city of Nueve de Abril (Argentina). The warehouse comprises pallet racks, as well as drive-in, push-back and live pallet racking that offer a grand total of 2,250 pallet storage positions. Products are deposited in the most appropriate system according to their characteristics and demand level.
Four decades in business
Coto’s history started in 1970 when Alfredo Coto and his partner Gloria founded a meat business that, at that time, sold an average of 40,000 kg of meat per month. In 1987, the owners built their first supermarket in the city of Mar de Ajó. Soon after, they opened new supermarkets in Buenos Aires and, later on, in the rest of Argentina. Since the end of the 90s, the company has exported beef and Hilton quota ‘ribs and loins’ to all of Latin America primarily.
Today, the supermarket chain encompasses more than 120 branches all over Argentina and is under expansion, constructing new points-of-sales nationally to make its products readily available to customers. Moreover, it has allied itself with different Argentinian producers to expand its product portfolio, which now boasts 500 private label brands.
Space well spent
Coto has a warehouse in the city of Nueve de Abril, in the province of Buenos Aires, which it uses as a supply point to all its supermarkets throughout Argentina. For the company, it was a priority to raise the storage capacity to fit a larger quantity of foodstuffs, mainly, fruits, vegetables and greens.
“To get the storage capacity we needed, we realised that we have to leverage every possible millimetre of our warehouse,” explains an engineer who works in this distribution centre.
Mecalux has equipped the warehouse with four different storage systems:
The combination of these solutions means the goods can be sorted as per their characteristics and level of demand. Additionally, in the engineer’s words, “we have fewer aisles and instead allocated this space to more racks on purpose, so we could accommodate a greater number of products.”
Distribution centre engineer at Coto
“Our Mecalux racks are the best quality and give us the high performance results we need to run our distribution centre’s 24-hour service. We are very satisfied with our installation’s throughput because we could organise products according to their level of demand. Plus, we have used all our space and boosted storage capacity.”
Pallet racking
Citric fruit and lightweight veggies (tomatoes, beans, peppers, garlic, aubergine, etc.) are deposited in these racks that hold 150 pallets. “These are consumer products. So, the direct access that these racks offer helps us streamline all our storage tasks,” the engineer points out.
One of its main advantages is its adaptability to any type of load, weight and volume variable. Racks include accessories to adjust shelf levels to the pallets’ dimensions. Moreover, these racks guarantee perfect stock control, since each location is assigned to the same SKU.
Drive-in pallet racking
Mecalux has installed drive-in racking for one of the most popular products at Coto: green bananas. According to the engineer, “the storage capacity means we can hold 300 pallets, enough to accommodate all our products.”
The racks are comprised of a set of 7.5 m high lanes, with three levels equipped with support rails and pallet centralisers for precise insertion of the loads.
Pallet trucks enter the inner storage lanes with their load raised above the level it is going to be deposited. Both loading and unloading of the goods are performed in the same aisle, but in reverse order.
Guide rails were installed on both sides of the floor since it is such a busy centre with such high incoming and outgoing movements. Thus, forklifts run centrally down the insides of the lanes, preventing possible blows to the racking structure.
Push-back pallet racks
According to the distribution centre’s engineer, “these racks are allocated to heavy vegetables (potatoes, carrots, pumpkins, onions, beets, etc.) that have an average rotation.” In other words, as average consumption vegetables, they require constant entries and exits each day, although not as intense as the other products.
Thus, one of the advantages of this storage system is product accessibility. This yields greater agility when handling the goods the moment they are needed (both during storage and extraction so they can be distributed).
Channels are arranged on a slight incline. The front side is lower so that, by taking a pallet out, those behind it slide forward by the force of gravity up to the first exit position.
Live racking
High rotation products like potatoes and onions are warehoused in the live racking.
The racks comprise slightly inclined roller channels so that the merchandise displaces via gravity automatically. Workers put the pallets into the highest part of the roller frames. Gravity works its magic, and the other pallets move towards the other point at a controlled speed, ready to be removed.
This solution speeds up the loading and unloading of pallets, since handling by personnel is minimal.
Plus, the distances being covered are nominal, since all SKUs are in the same aisle. The engineer at Coto points out that “Even though the distinct storage systems let us apply different inventory management methodologies, for example, push-back and drive-ins organised with LIFO (last in, first out); in this case, the goods are managed as per FEFO (first expired, first out). So, the pallet whose labelled expiration date is approaching is the first out, making perfect product rotation possible.”
Advantages for Coto
- Maximum storage capacity: the four storage systems have optimised the volume of this warehouse sector to yield a capacity for 2,250 pallets, exactly what Coto needed.
- Efficient warehouse organisation: each product is deposited in the most appropriate storage system taking their characteristics and demand level into account.
- High productivity: all the storage solutions are designed to ensure a massive flow of product inputs and outputs.
Distribution centre of Coto: Pallet racking | |
---|---|
Storage capacity: | 150 pallets |
Pallet size: | 1,000 x 1,200 mm |
Max. pallet weight: | 1,350 kg |
Racking height: | 8.7 m |
Racking length: | 37 m |
Gallery
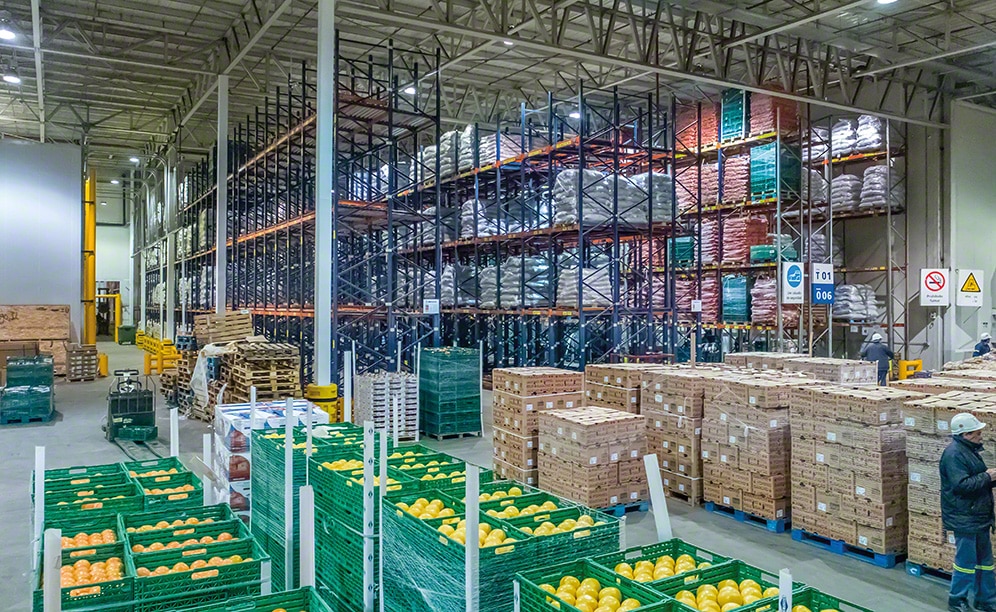
The fresh fruit warehouse of Coto in Nueve de Abril (Argentina)
Ask an expert