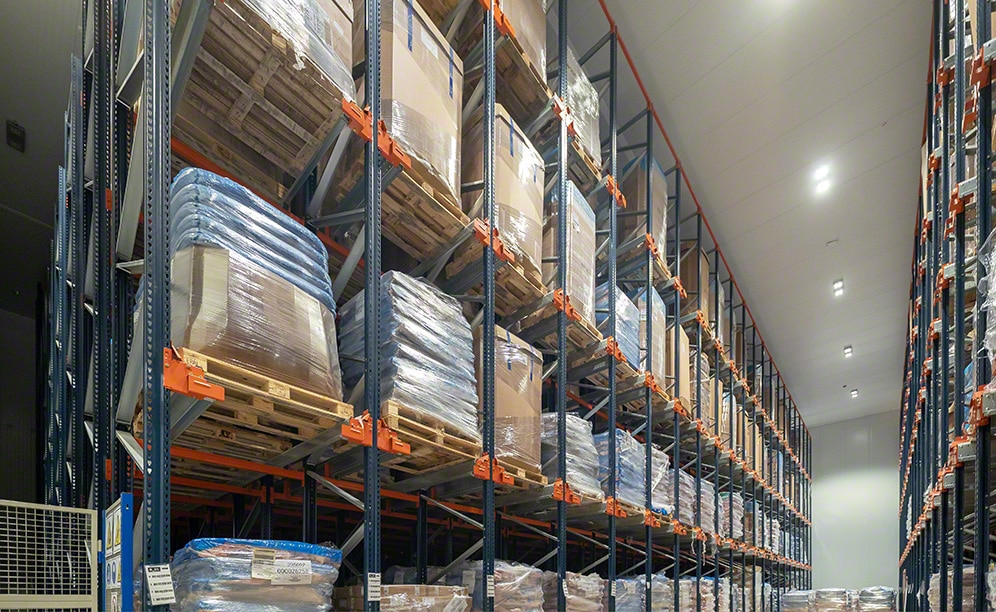
The ice cream warehouse of Helados Estiu in Chester (Valencia)
Helados Estiu can house its ice creams, bonbons and cakes in the Pallet Shuttle run racks.
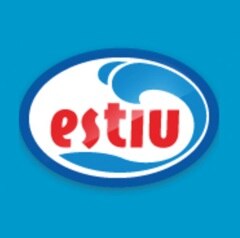
With more than 30 years under its belt, the Helados Estiu i.e. “Summer Ice Creams” manufacturing company has opened up a brand new logistics centre in Cheste (Valencia). Equipped it with the Mecalux Pallet Shuttle system, the company can now store 10,344 pallets. This solution ensures top capacity, as well as speedy pallet inputs and outputs.
About Helados Estiu
Founded in 1983, Helados Estiu is a 100% Valencian funded company, with a long family history of ice cream making.
In the last few years, after reaching exponential growth, it saw fit to expand production to fulfil rising sales. It started out making half a million litres of ice cream and, at the moment, this number exceeds 25 million litres. To do so, it purchased a 70,000 m2 plot of land in Cheste (Valencia) where it has constructed a warehouse for finished products, ready to be shipped out.The finished product warehouse
This facility comprises four frozen-storage chambers that run at a steady -25 ºC. SKUs are placed in the corresponding frozen storeroom depending on their level of demand. Mecalux has equipped the four chambers with the semi-automatic Pallet Shuttle system. It involves a high-density storage system that fully uses the available space to provide greater storage capacity. Overall, it can store 10,344 pallets.
Each of the chambers has two blocks of 11.5 m high drive-in racks, one in front of the other. Three of the chambers hold goods and are managed as per the FIFO principle (first in, first out). In other words, the first pallet in is the first to leave. The pallets are inserted into one side of the racks and extracted from the opposite side. Meanwhile, in the remaining chamber is run through LIFO (last in, first out) managements because pallets enter and exits from their locations on same side of the aisle.
A main feature of this storage system is it’s speed when it comes to load management. Operators place the Pallet Shuttle into the corresponding channel, deposit pallets into the rack’s first position and the shuttle transfers these to the next open location inside the channel automatically. The same process takes place but in reverse order when removing the goods.
Operators use a tablet with an internet connection to control the automatic shuttles. Its user interface is highly intuitive and, through the device, workers select the shuttle that will run a task, pick out which strategy to run (input or output of the goods) or do inventory.
The shuttles have built-in cameras and the operator’s tablet is used as a monitor to reproduce images. This is of great help because the operator can visualise the direction and movement of the forks when they need to insert the Pallet Shuttle in the channel, which has a positive impact on the work.
Advantages for Helados Estiu
- Maximum storage capacity: the racks make maximum use of the available space to provide storage capacity for 10,344 pallets.
- Fast, compact system: the Pallet Shuttle carries out inputs and outputs of the goods at top speeds.
- Efficient goods management: product are slotted to fulfil the FIFO criterion, something essential in dealing with food type goods and those with expiration dates.
Logistics centre of Helados Estiu | |
---|---|
Storage capacity: | 10,344 pallets |
Pallet size: | 800 x 1,200 x 2,450 mm |
Max. pallet weight: | 1,100 kg |
No. of channels: | 600 |
Height of racks: | 11.5 m |
Length of racks: | 33 m |
Storage channel depth: | 8 and 19 m |
Gallery
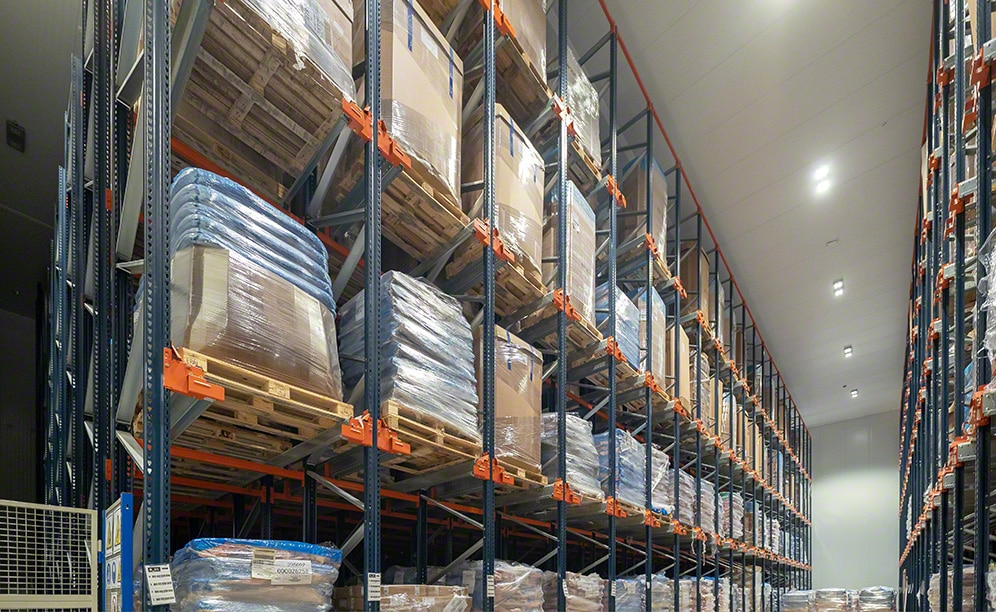
The warehouse of Helados Estiu in Chester (Valencia)
Ask an expert