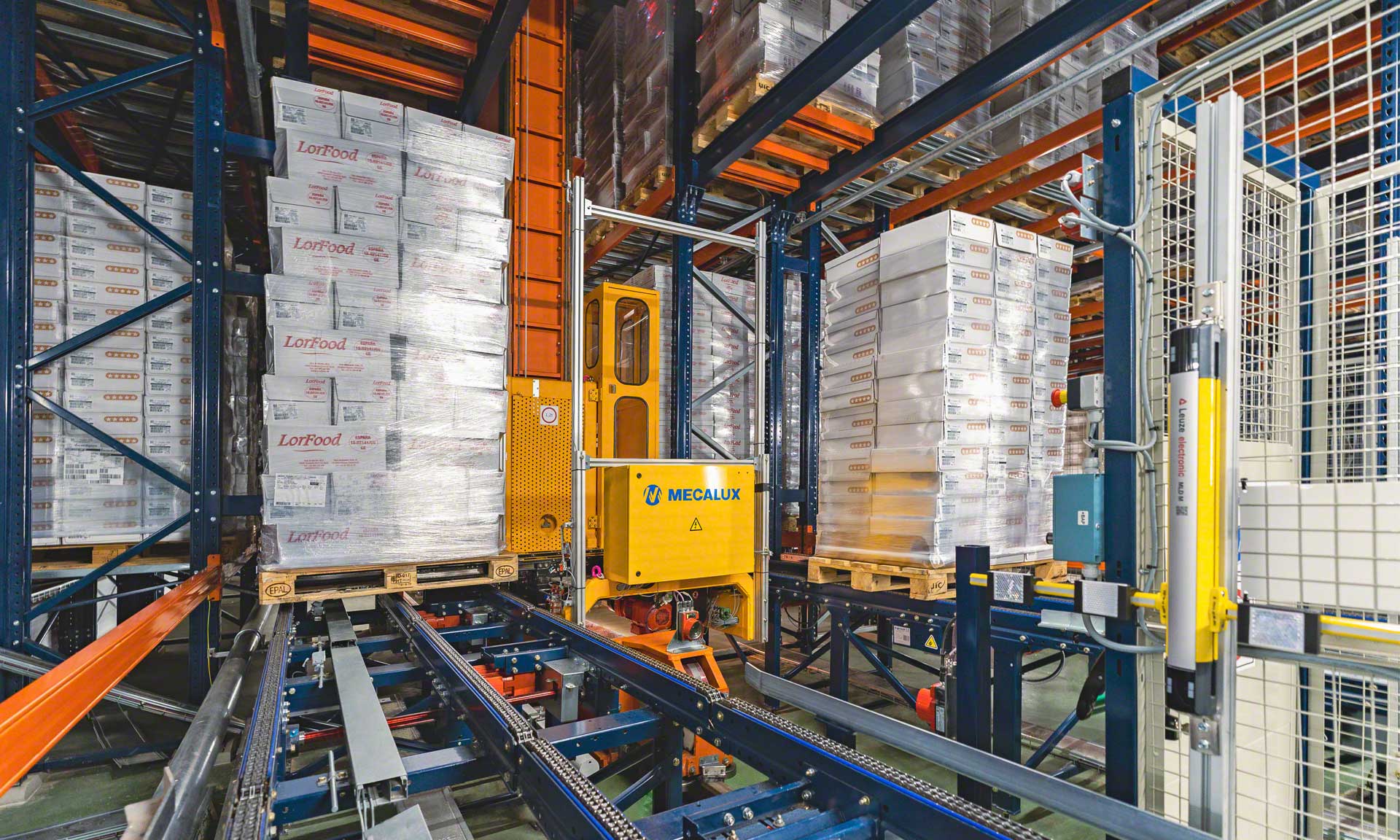
Logistics at low temps: comprehensive solution in six warehouses
Mecalux has been enlisted as Incarlopsa's trusted provider, equipping six warehouses
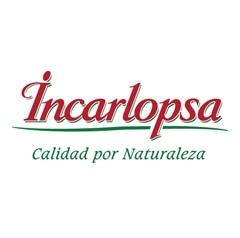
Managing logistics processes for food at low temperatures presents an added challenge: guaranteeing quality while preserving the cold chain. Incarlopsa, a leading producer of pork products in Spain, has incorporated the most cutting-edge technology on the market in all its logistics processes to boost productivity and ensure the traceability of its goods. Mecalux was chosen to be its trusted logistics provider, outfitting six Incarlopsa warehouses at its plants in Tarancón and Corral de Almaguer, Spain. These facilities stand out for their automated operations, which have contributed towards Incarlopsa’s expansion in recent years.
Quality by nature
Founded in 1978, family business Incarlopsa has become a benchmark in the Spanish meat sector. With its headquarters in Tarancón (south-east of Madrid) and its 11 production centres throughout Spain, the company specialises in the processing of fresh pork products, cured ham, Iberian sausages and cooked sausages. Incarlopsa, which employs over 3,600 people, closed the 2020 financial year with a turnover of €883 million, accounting for an increase of 4.7% over the 2019.
For over 40 years, an unwavering commitment to product quality and to a responsible, sustainable and long-term business model have been crucial for this family-run company. Its promotion of the local economy plays a key role in boosting activity around its production centres.
Incarlopsa combines its financial and environmental objectives with a social perspective. An example of this was the effort made by the company at the start of the pandemic: it donated medical supplies and protective materials to hospitals, nursing homes, police stations and city halls, as well as food to the Spanish Federation of Food Banks (FESBAL) and the Red Cross, among other organisations.
Incarlopsa and Mecalux: collaboration between two touchstones in their sectors
“We’re extremely satisfied,” says Victorino Carabantes, General Manager of Engineering at Incarlopsa, regarding the throughput of the four warehouses Mecalux installed at the Tarancón plant and the two it commissioned in Corral de Almaguer. Both facilities were recently certified for organic production.
The relationship between the two companies began more than 20 years ago, with the installation of manual facilities that, over time and due to Incarlopsa’s constant growth, have given way to state-of-the-art storage solutions. During that time, Incarlopsa has consistently relied on Mecalux as its trusted logistics provider. “Its warehousing solutions always more than meet our logistics needs,” says Carabantes.
The six warehouses Mecalux has equipped for Incarlopsa have two essential qualities for this meat company: automation and traceability. “We have uninterrupted, controlled goods movements,” notes Carabantes. Automation comes in the form of the automated storage and retrieval systems (AS/RS) for pallets, while traceability - vital when working with food - is provided by Easy WMS, the warehouse management system (WMS) from Mecalux.
“Our aim was to store a large number of pallets in the smallest space possible,” says Carabantes. The AS/RS make the most of the available surface area to provide the greatest storage capacity and, thus, reduce the energy consumption for cooling.
Carabantes highlights another aspect that was fundamental when it comes to attaining logistics excellence: “Thanks to Mecalux’s extraordinary after-sales service, our warehouses are almost 99% operational."
Incarlopsa in Tarancón
Tarancón is home to Incarlopsa’s corporate headquarters as well as one of its most modern centres in Spain, expanded and renovated on a regular basis. It currently features a slaughterhouse, a fresh meat packaging and processing plant, a slicing plant and a ham drying room. In line with its commitment to promoting and improving sustainable development, Incarlopsa has installed six smart freezer tunnels that optimise energy consumption and raise the company’s total freezing capacity to 120 tonnes.
Mecalux has participated in four automated projects in the Tarancón centre, which stores about 8,500 pallets:
- AS/RS for pallets at a refrigerated temperature. With capacity for 1,994 pallets distributed in two 38.3-metre-long aisles, this system houses finished products sent to customers. Annexed to the warehouse, Mecalux has set up two rooms with temperature control units to store 25,200 hams at -20 °C.
- AS/RS in a freezer store. Also used to accommodate the finished product, this system is equipped with two 36.1-metre-long aisles with double-deep racks and capacity for a maximum of 2,352 pallets. In each aisle - separated by a wall to better maintain the cold - a stacker crane inserts and removes goods into/from their locations automatically.
- Automated clad-rack warehouse. This facility is comprised of four aisles measuring 50 m long by 26.5 m wide: three operate at a frozen temperature of -30 °C for product waiting to be sent to the processing lines, while the fourth runs at an ambient temperature and stores auxiliary material. This building consists of a self-supporting structure and is connected to production by means of conveyors. It features a pallet entry and exit area at both ends of the racks.
- AS/RS with the semi-automatic Pallet Shuttle system. Mecalux has installed three units of 9.2-metre-tall pallet racks that accommodate 752 pallets containing finished product. This storage system operates at a controlled temperature of between -18 °C and -22 °C. The goods are managed according to the LIFO (last in, first out) method in two of the racking units and in line with the FIFO (first in, first out) method in the third.
Incarlopsa in Corral de Almaguer
In Corral de Almaguer (south-east of Madrid), the company boasts one of the world’s largest ham drying rooms, with an annual production capacity of 4.25 million pieces of ham. There, Mecalux has also commissioned two AS/RS: one in one of Incarlopsa’s freezer stores and another in a cool store. The overall capacity of both systems is 6,560 pallets.
- AS/RS at a frozen temperature. This system stands 22.5 m tall and consists of two 70-metre-long aisles. The AS/RS houses 4,448 pallets at -20 °C containing goods to be processed on the production lines. The two aisles, joined by a transfer car, are separated by a wall to more effectively maintain the cold air in each aisle.
- AS/RS at a refrigerated temperature. This system is slightly taller (24.4 m) but shorter (41.9 m) and works at 0.2 °C. With a total capacity for 2,112 pallets containing finished product, its operation is practically identical to that of the freezer warehouse, with two aisles connected by a transfer car. In this case, though, the two aisles are not separated by a wall.
Every day, 200 pallets are prepared at the Incarlopsa centre in Corral de Almaguer.
Safety: food logistics
Incarlopsa’s facilities are noted for their efficiency, productivity, speed and safety when dealing with food. In this vein, the company has implemented technology in all its processes, including production, storage and management.
Storage: automation for working in the cold
Meat must be kept at ideal temperatures to ensure that it is preserved properly. Therefore, Incarlopsa’s freezer stores are built with sandwich panels - insulating elements that prevent the transfer of the cold air to the exterior - while the flooring is also insulated to stave off condensation (ice build-up). The freezer stores have all the necessary cooling equipment: compressors, condensers, expansion valves and evaporators.
Outside the cold store, a secure airlock system has been installed. This antechamber has two fast action doors - one opens into the chamber while the other leads out - which are never open at the same time. The system is used to prevent cold loss, condensation and sudden changes in temperature.
Lastly, investing in AS/RS not only guarantees correct product handling, but also facilitates the work of the operators, simplifying tasks and making them more efficient in those that are indispensable. “Our team is used to working with automated storage and retrieval systems, which helps us operate reliably and effectively,” says Carabantes.
Management: Easy WMS
Incarlopsa’s warehouses are outfitted with the Easy WMS warehouse management system to orchestrate all goods movements (entries, storage and dispatch) and offer total traceability.
“I’m sure we’re not even exploiting 50% of the potential of Easy WMS, but it’s more than enough to control the goods and exchange information with our JD Edwards ERP system,” says Carabantes.
The minute they arrive at the warehouse, Easy WMS sorts the items in batches, using algorithms to assign each pallet an appropriate location. Easy WMS maintains full control over the goods, providing information on stock status in real time. This WMS knows all the product details, such as size, batch, weight, characteristics, production and expiry dates, and inspection controls passed.
The traceability provided by Easy WMS is a must for a food business such as Incarlopsa; it helps it to identify and strictly monitor the product characteristics and all the phases the goods go through before being delivered to customers. This eliminates errors and ensures compliance with hygiene standards.
Comprehensive logistics for productivity and safety
“With the automated systems from Mecalux, we’ve improved inventory control, optimised the storage area and, particularly, reduced the use of manual handling equipment. The result has been a net growth in productivity and security,” says Carabantes.
Incarlopsa has a highly competitive supply chain due in large part to the logistics efficiency of the AS/RS from Mecalux.
In addition, the business can now better respond to changes in demand, maintaining the quality and flavour of the meat at all times. “We’re an innovative business in our sector; we’re not afraid of automation, and we’ve been investing in automated systems for 20 years. Fortunately, we’ve continued to see year-on-year growth. So, there’s no doubt we’ll continue to rely on Mecalux’s automated logistics solutions in the future,” says Carabantes.
I’d stress the security and control of the goods that we’ve gained by automating our supply chain. On the one hand, we’ve increased the safety of our operators and our facilities. On the other, the control we now have enables us to know for sure the quantity and location of our products. Thanks to automation, the rate of human error has completely disappeared from stock control.
Advantages for Incarlopsa
- Increased productivity: Incarlopsa’s supply chain can efficiently cope with an annual production of 150,000 tonnes of meat products.
- Improved traceability: Easy WMS monitors the food along the various stages it goes through, controlling every detail of Incarlopsa’s products (size, batch, weight, characteristics, production and expiry date, etc.).
- Goods security: automation ensures the safe transport of the meat while preserving the cold chain. This ensures its flavour and quality.
AS/RS at a frozen temperature - Plant in Corral de Almaguer | |
---|---|
Storage capacity: | 4,448 pallets |
Pallet sizes: | 800/1,000 x 1,200 mm |
Max. pallet weight: | 1,000 kg |
Racking height: | 22.5 m |
Racking length: | 71 m |
Gallery
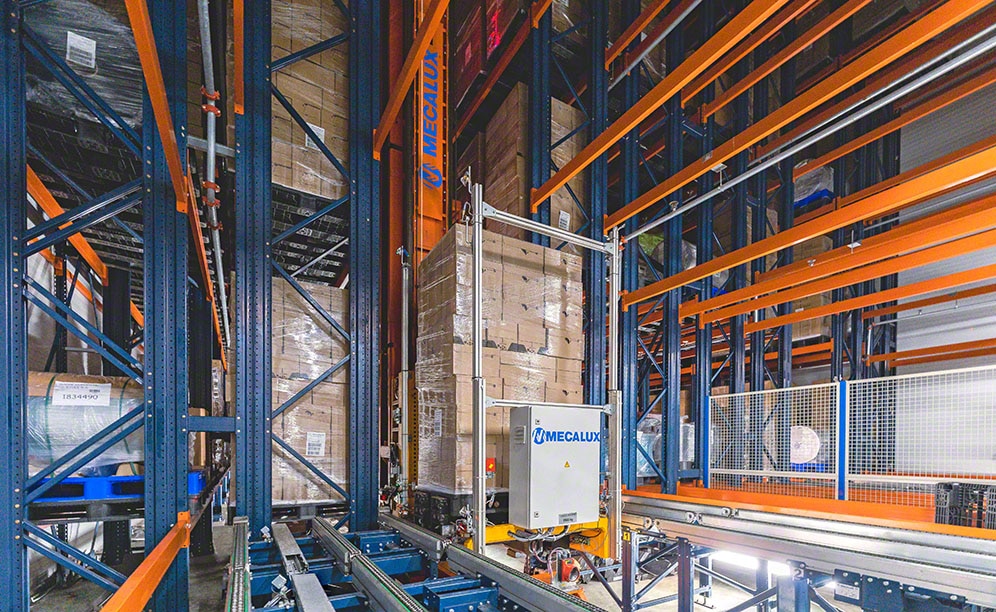
Tarancón is home to Incarlopsa's headquarters and one of its most modern plants
Ask an expert