
Innoaesthetics boosts its growth with a digitalised logistics strategy
Skincare laboratory Innoaesthetics digitalises its logistics operations to enhance efficiency.
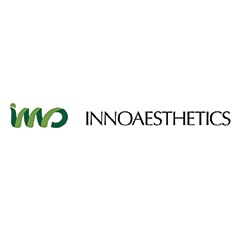
Innoaesthetics, a dermatological and aesthetic medicine laboratory, has digitalised its warehouse in Barcelona with Easy WMS. The software ensures the traceability of raw materials and finished products. Additionally, it optimises and streamlines operations such as order picking.
Innoaesthetics: skin care solutions
With over 120 years of experience, Innoaesthetics is a family-run manufacturer of dermatological and aesthetic medicine products. Its priority is to develop formulas with innovative active ingredients that enhance the therapeutic effect of their treatments. In addition to its own brands for professionals and end customers — Innoaesthetics and Meline — the laboratory develops solutions for other organisations.
Founded in 1898, Innoaesthetics is composed of a professional team of over 80 people and is present in more than 75 countries. In 2022, it received the SME Award granted by the Barcelona Chamber of Commerce.
CHALLENGES
|
SOLUTION
|
BENEFITS
|
---|
“In recent years, we’ve experienced rapid and substantial business growth. While this has afforded us valuable opportunities, it’s also presented considerable challenges. We unexpectedly found ourselves having to handle a large number of orders — and we weren’t adequately prepared for this,” says Liliana Concha-Alecchi, Logistics Manager at Innoaesthetics.
The company used to carry out all its logistics operations manually: warehouse operators would make a note of incoming and outgoing products in the ERP system. “Even though the ERP controlled stock, we needed much more effective management of the goods to facilitate key operations like order picking. With the steady growth we were seeing, it was essential to improve processes in our facility. That was when we decided to digitalise our supply chain with specialised software,” says Concha-Alecchi.
Innoaesthetics has digitalised its logistics centre in Barcelona, Spain, with Mecalux’s Easy WMS warehouse management system. This powerful software program manages inventory in real time. The skincare laboratory’s facility is divided into two warehouses: one for storing raw materials sent to production and another for finished products distributed to customers.
The Mecalux software has optimised all goods movements, enabling the business to provide high-level service to its clientele, with on-time, error-free deliveries. “Easy WMS is a flexible software program that fits us like a glove. Together with Mecalux’s technical team, we designed a customised solution capable of addressing our fundamental needs: boosting order distribution and optimising picking,” says Concha-Alecchi.
Improved operations
“Easy WMS controls all operations in our logistics centre, from the distribution of storage locations to order picking, which is now much simpler,” says Concha-Alecchi.
The system identifies all items, from their arrival at the facility through to their shipment to customers. In total, 85% of Innoaesthetics’ production is exported. “We have over 80 distributors around the world, primarily in China, India, New Zealand, Ecuador, Venezuela, the US, Canada and other countries in Europe,” says Concha-Alecchi.
Warehouse operators use RF scanners to perform their tasks. “This makes them much faster,” says Concha-Alecchi. Easy WMS sends operators extremely precise instructions. As a result, it knows the exact location of all products and the movements they make in the logistics facility until the orders are distributed to customers.
“Traceability is vital in our sector. Although our ERP had it covered, there was definitely room for improvement in the process. Before, we would record goods-in/goods-out in the ERP program, but we really needed to optimally organise the locations and be able to track products at any given time. With Easy WMS, we’ve achieved this,” says Concha-Alecchi. By tracing the movement of each item, Innoaesthetics has significantly reduced the number of errors made and can ensure that its end customers receive top-quality orders. Easy WMS knows the status of all SKUs in stock, from raw materials and components for production through to finished products.
Easy WMS has also been integrated with Innoaesthetics’ ERP system to maintain tight inventory control. The logistics software informs the ERP of the stock required to prepare orders so that it can take care of replenishment. This action prevents stockouts that could lead to delivery delays. “This was the main reason behind the whole project: to simplify goods management and inventory control,” says Concha-Alecchi.
The Mecalux software assigns a location to the goods — whether raw materials or finished products — according to variables such as SKU type and demand level. “We organise items by turnover: those consumed most frequently are more accessible to facilitate their entry and exit. And those with a lower demand are placed in slightly more distant areas,” says Concha-Alecchi. Products are stored following the FIFO (first in, first out) method.
The correct distribution of the goods has a direct effect on order fulfilment: it makes operators quicker when locating goods to be sent to production or end-customers.
“To pick the required materials, operators simply go to the location indicated by Easy WMS. They no longer have to roam the warehouse searching for items. In the past, one operator would collect the merchandise, another would check it and a third would place it in the box to be used to ship it. We did all this with a single aim: to avoid human errors. Thanks to the software and the RF scanners, we’ve eliminated any possibility of mistakes. We’re also much faster at filling orders,” says Concha-Alecchi.
Logistics in growth mode
“The company has grown tremendously over the past few years and we expect this trend to continue. Our goal is to serve our customers with the excellent service and professionalism we’re known for,” says Concha-Alecchi. With Easy WMS, Innoaesthetics is equipped with a digital tool that will support it in implementing its plans for expansion in the coming years. The system organises all available resources to ensure efficient order fulfilment and distribution and make delivery delays a thing of the past.
“The cosmetics market is highly demanding and constantly changing. We always have to be ahead of the curve, continuously launching new products in line with customers’ new needs,” says Concha-Alecchi. With the Mecalux software, Innoaesthetics’ supply chain is at the forefront, prepared to take on this fast-moving market with all its SKUs under control.
We’ve digitalised our warehouse with Easy WMS to better organise and control our goods. It was critical for us to provide effective product traceability and streamline key operations such as order picking.
Ask an expert