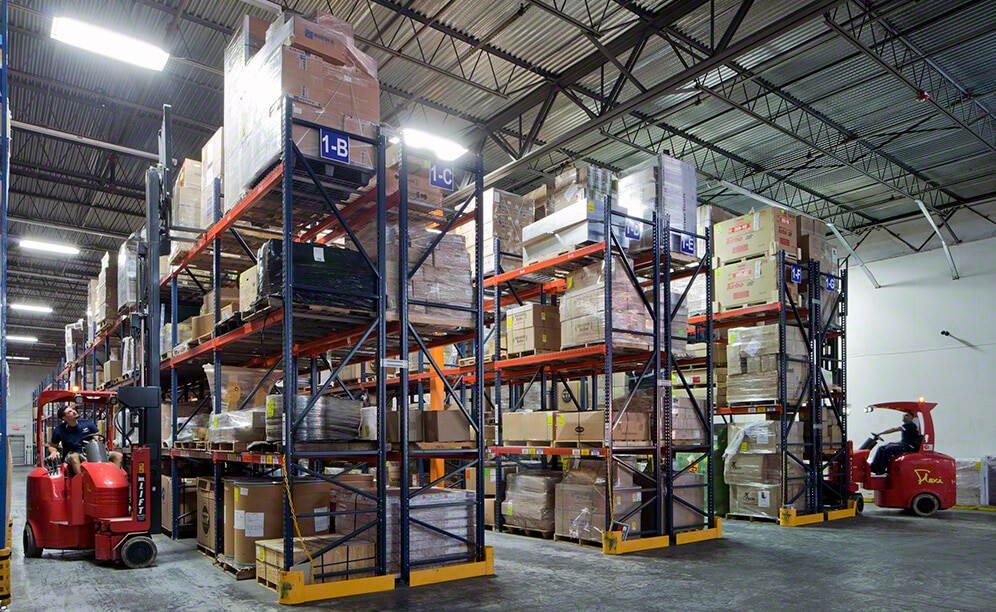
The Interworld Freight logistics warehouse in the United States
Multiple solutions in the Interworld Freight 3PL warehouse in Miami (United States)

The logistics operator Interworld Freight has renovated its warehouse in Miami (United States) with pallet racks, push-back racks and a mezzanine by Interlake Mecalux. These solutions make full use of available space to provide higher storage capacity and, moreover, ensure tight control over the goods.
About Interworld Freight
The Interworld Freight warehousing facility in Miami is home to a wide variety of products: from ordnance to soya sauce. It is a global logistics and distribution company that provides air and sea transport services to all types of companies.Interworld Freight opened in Colombia in 1992 and, only a few years later, its founder, John Crespo, moved the company to the US. In its beginnings, Mr Crespo took charge of almost all operations in the 74 m2 warehouse in Miami, from slotting tasks to loading incoming transport vehicles.
At a later stage, it moved to a 930 m2 warehouse where it hired eight operators to work the space. Recently, it held the grand opening of a 2,787 m2 warehouse installation that now employs more than 50 people. These days, the company manages around 7,000 or 8,000 sea containers, mainly in the US’s central and southern regions.
Space to grow
The company did not have enough room to handle the rise in goods. It reached the point that no one could walk or move around the warehouse since it was so packed. Plus, workers had stopped running four of the six reach trucks on hand because space restrictions made it impossible to operate them.
Faced with this situation, the company made plans to move to a larger-sized warehouse and, in fact, was just about to rent out a 5,574 m2 logistics centre.
However, before doing so, a handling equipment distributor convinced the company that storage space purposing was the real issue, and something to look at before deciding to rent out more space.
So, it got in touch with Atlantic Rack (a storage systems provider) to help rethink its installation’s layout.
The solution: Interlake Mecalux racks
“The warehouse was in complete chaos. Everyone was setting down products wherever there was a bit of open floor space,”, admitted one Atlantic Rack’s managers. The old, worn out racks were the reason things were out of control since they could only house 100 pallets, at the most.
Atlantic Rack analysed the warehouse’s dimensions in detail, as well as operation and product rotations throughout a normal working day. The company realised that product could not stay stored long (i.e max. a couple of weeks).
Keeping this in mind, Interworld Freight opted to install pallet racking from Interlake Mecalux that have the capacity to hold 1,346 pallets. The facility also includes push-back racks that significantly increase the warehouse’s capacity by 35% to 38%.
The company has also installed narrow, 2 m wide aisles to best use available surface area and obtain a higher storage capacity, as well as a two-tier mezzanine (i.e. picking done on the upper level and box storage on the lower).
Advantages of Interlake Mecalux racks
Considering Interworld Freight’s huge variety of products, the pallet racks from Interlake Mecalux have turned out to be a highly-suitable solution. Pallet rack-based systems offer direct access to the goods, space-purpose the surface area best, facilitate stock control and prevent loads from getting into or causing accidents or receiving blows. In fact, from when its warehouse was updated, the company has stopped receiving complaints from customers about products in poor condition.
Also, push-back pallet racks from Interlake Mecalux have made all the difference, by being a high-density storage system that optimises available space. The company receives close to 15 identical pallets of various SKUs, making this storage system highly suited for this type of storage situation.
Interworld Freight’s warehouse has undergone a spectacular transformation. The company distributes up to 15 containers in one day, i.e., triple of previous shipments. In the past, operators spent between three or four hours preparing a single container. Locating the SKUs that comprised each order was a laborious process, involving incessant crisscrossing of the entire warehouse by personnel to get the job done. However, finding the load is a no-brainer now since the team knows exactly where to get what they need.
Each day, various truckloads arrive at the warehouse from different spots throughout the United States. Operators must then count, measure and weigh incoming products. Afterwards, each item is entered into the WMS warehouse management system run at this installation, and labels are printed from that information and stuck to each pallet as identification.
Operators, riding trilateral forklifts, set the merchandise in the rack location the WMS assigns the palletised goods. Interworld Freight notifies the customer their products are stored and, next, Interworld Freight receives back a report with instructions on how to manage these goods over the next few days (which day to distributed, where, etc.).
Manager of Interworld Freight
“We are more than happy with our Interlake Mecalux racks because they have completely transformed our warehouse distribution and, from commissioning, we have minimised errors and stopped getting customer complaints.”
Advantages for Interworld Freight
- Greater storage capacity: these Interlake Mecalux solutions use the available space intelligently. Goods are no longer set on the floor and the initial storage capacity has tripled.
- Streamlined operations: trilateral forklifts insert and extract pallet from their locations quickly.
Gallery
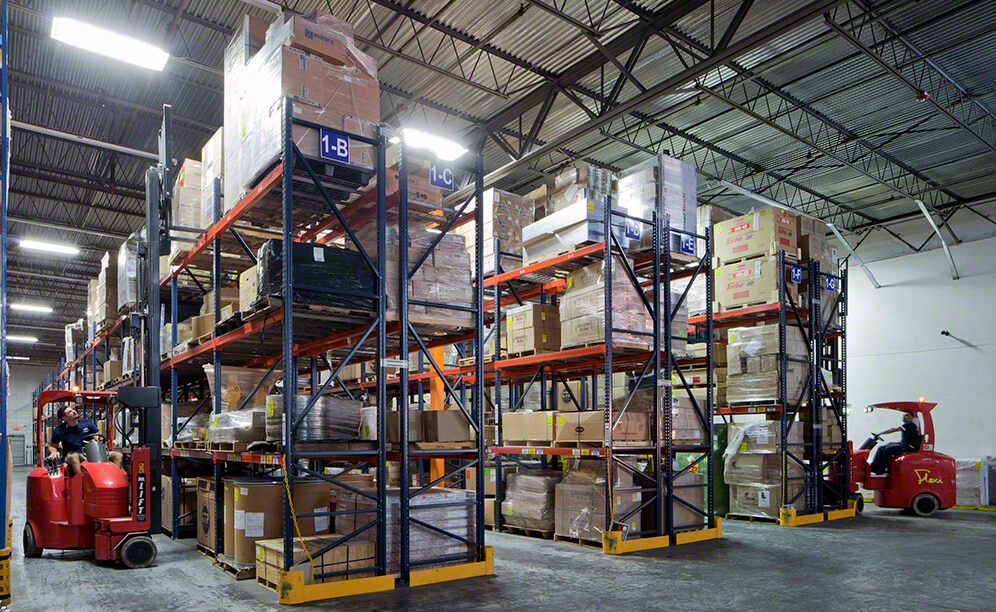
Interworld Freight’s 3PL operator warehouse in Miami
Ask an expert