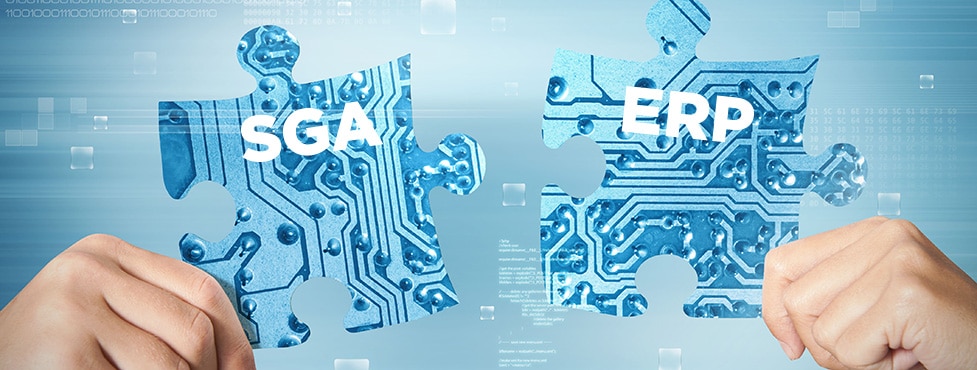
Purchasing network IXOS cealco digitalises its logistics to provide streamlined service
Easy WMS manages the preparation of orders for the IXOS cealco Group's points of sale and the new IXOS shops
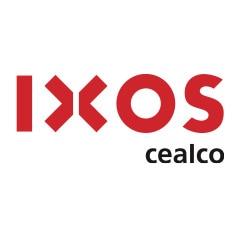
Purchasing network IXOS cealco is opening a chain of shops throughout Spain to provide more agile service focused on the customers of the companies that make up the group. To do so, it needs to have an advanced, modern and flexible logistics system. Easy WMS, the warehouse management system by Mecalux, streamlines order preparation and dispatch and ensures stricter control of the 5,000 SKUs at the firm’s warehouse in Granollers (Barcelona, Spain).
Transformation in progress
Purchasing network IXOS cealco was founded in 1977 when a group of wholesalers from the plumbing, air conditioning and heating sectors joined together. Their daily activities consisted of buying, storing and dispatching supplies required by the companies comprising the group.
IXOS cealco includes multiple partners and suppliers, some of which have been doing business for over 100 years. As a result, it has picked up very valuable knowledge from this extensive experience, becoming a major stakeholder in the distribution of plumbing and heating products.
In recent years, the company has faced numerous changes in its business. On the one hand, it has launched its own brand (called ‘concept’), with a wide range of over 1,000 items for plumbing and air conditioning installations. It has also increased its international presence in countries such as Germany, France, Belgium and Poland through the EDT Group, Europe’s largest organisation dedicated to representing independent wholesale firms specialising in bathroom fixtures and heating products.
On the other hand, IXOS cealco has started up one of its most ambitious products to date: the creation of a chain of shops all over Spain named IXOS.
Manuel Hervás, Logistics Manager at IXOS cealco, describes the particulars of the IXOS project, which has involved great effort and brought tremendous satisfaction, saying, “We used all the accumulated know-how in our experience as a purchasing network to open several shops. Our idea is to get a lot closer to our customers and help them more quickly and effectively.”
Integrating the WMS with the ERP
In the city of Granollers (just 26 km from Barcelona), IXOS cealco has a 5,000 m2 facility where it manages 5,000 SKUs in total. It is a multi-channel warehouse, supplying IXOS establishments as well as the 93 sales outlets of the group’s partners. Currently, there are only seven shops in northern Spain (the first was set up in Vitoria in 2019, while 2020 saw the opening of three IXOS retail outlets in the Basque Country and another three in Navarra). However, the company plans on opening more points of sale in the next few months.
The facility is made up of two warehouses: the main one is a larger building in which most of the goods are stored (mainly pallets and 5- to 6-metre-long pipes).
The other is a smaller installation just beside it, where orders containing smaller goods are prepared. With the opening of the new IXOS shops, warehouse operations have become more complex. Now, workers not only manage a large number of very diverse SKUs, but also prepare many orders for both physical shops and IXOS cealco’s partners. Against this backdrop, the company set out to modernise and perfect its entire logistics system.
Previously, the company supervised its supply chain with the help of the Sage X3 ERP and Microsoft Dynamics NAV. These systems are prepared to perform the facility’s most basic day-to-day operations (for example, monitoring of goods receipts and dispatches) and prepare a limited number of orders. As these increased, the firm was forced to alter its processes.
It was looking for a more sophisticated, advanced system for its logistics activities that was capable of boosting the productivity of warehouse operations. In the words of Manuel Hervás. “It was then that we seriously considered implementing a warehouse management system (WMS) with certain guarantees and market recognition.”
However, IXOS cealco’s Logistics Manager adds, “Our priority was for the WMS to integrate well with the ERP and be able to adapt to changes in the company. This installation was the first designed for the IXOS project. However, we plan to open more shops and warehouses in the future, and we want all of them to be connected just as easily.”
After comparing various options, the company chose Easy WMS, the warehouse management system by Mecalux. “They recommended it because its capabilities and functionalities could more than meet our needs. That was clear to us when we saw that it could integrate with our Sage X3 ERP with no problem,” assures Manuel Hervás.
The objective of this integration is for the WMS and IXOS cealco’s ERP to communicate continuously and bidirectionally. In this way, both systems transfer data and information to achieve increased productivity in operations.
Optimising operations
In the warehouse, two operations are primarily carried out: goods receipt and order prep and dispatch. Easy WMS can make the most of them in two different ways.
On the one hand, it controls inventory to avoid stockouts that would cause interruptions to service. On the other, it tells the eight operators in the installation how to fulfill their tasks and designs routes throughout the facility that minimise travel distances.
The operators use radiofrequency terminals to communicate with the WMS in real time. “Our team has been working with this system for years. When we decided to implement Easy WMS, we stressed that we wanted it to be intuitive and user-friendly,” ,” notes the Logistics Manager.
Greatly improved goods receipts
Manuel Hervás emphasises, “Easy WMS has especially helped us to improve goods receipts. Now, we are quicker and more efficient than before when allocating the same human resources.” Every day, the warehouse receives between 50 and 60 pallets per day from Spain, as well as other countries such as Italy, Germany and Bulgaria.
The ERP notifies Easy WMS in advance of the goods that are scheduled arrive; immediately afterwards, the operators verify that none of them are missing. Working with notifications of pending deliveries, or ASNs (Advanced Shipping Notices), ensures that the goods are extremely secure and reduces the possibility of mistakes.
In total, 25% of the pallets are single-SKU; that is, they contain products all belonging to the same SKU. These pallets have a label that operators merely need to read with their radiofrequency terminals in order for the WMS to recognise the item.
The warehouse also receives individual products of various SKUs. As they are identified, they have to be grouped onto pallets, following instructions from Easy WMS.
In this process, the WMS assigns the goods a location based on their particular features and demand level. Manuel Hervás states, “Goods are stored using the FIFO (first in, first out) method. Even though hardly any of our products have expiry dates, we make sure they are dispatched taking into account the order in which they arrived at the installation.”
Several of the items received are shipped directly without having to be stored. This working practice, known as cross-docking, streamlines dispatches and frees up warehouse space. It is employed when a product received forms part of a pending order.
Operators specialised by order and product
The ERP also notifies Easy WMS of the products that need to be prepared and dispatched. Every day, 35-40 orders made up of 30-35 lines each are sent. They comprise up to 60 pallets in total, the equivalent of two fully-loaded lorries. Operators specialise in product type, area and work equipment.
Thus, for example, the worker who prepares orders containing pipes only picks and handles pipes. Easy WMS sends personalised orders to each operator, taking into account his/her location in the installation. Therefore, the items they need to work with are found close by.
Workers follow an order grouping method that consists of picking SKUs for several orders on the same run. Most of the orders include stock from more than one area in the warehouse, so, various operators each prepare a part of the order, leaving the products they have picked in the consolidation zone. There, the items that make up a single order are grouped onto pallets.
They are subsequently wrapped, labelled and sent to the dispatch dock, where they remain until they are loaded onto the lorry. To perform this action, operators follow instructions from the WMS, which tells them what goods to deposit inside and in what order. For example, parcels to be delivered first are the last to be placed on the lorry.
A qualitative leap for warehouse management
The IXOS cealco purchasing network has decided to make its supply chain more flexible with the installation of Mecalux’s warehouse management system, Easy WMS. With this software, the company can not only lend continuity to its business and meet the needs of the firms that constitute the group, but also respond to new market demands.
The company has gone from managing its installation with an ERP to doing so with a WMS, thus, obtaining greater throughput in all processes. “The WMS has been aligned with our way of working and the particularities of our facility,” indicates IXOS cealco’s Logistics Manager.
After enhancing the management of its warehouse, one possible future improvement the company is considering is to carry out more accurate control of the stock available in its shops. To do this, it would implement the Store Fulfillment module, a system that coordinates operations in the shop and the installation, transferring items with no possibility of error.
In reality, Easy WMS is specifically designed to address the needs of each individual company. As a result, IXOS cealco has a seamless logistics system prepared to provide efficient service.
Manuel Hervás - Logistics Manager at IXOS cealco
“One of Easy WMS’s most outstanding features is its easy integration with our Sage X3 ERP. Likewise, Easy WMS has been moulded to and boosted our warehouse operations. Now, we can face any changes in our business with confidence, including the opening of new shops and warehouses down the line.”
Advantages for IXOS cealco
- Adaptable system: Easy WMS can be adjusted to market trends and any changes IXOS cealco might undergo in the future, such as the opening of more IXOS shops.
- Integration with the ERP: Easy WMS has been integrated with IXOS cealco’s Sage X3 ERP. The two systems exchange data and information to optimise warehouse operations.
- Multitude of SKUs: the WMS controls all stock, consisting of 5,000 SKUs of different sizes and characteristics.
- Variety of orders: the system also organises and supervises the preparation of orders. These can be sent to the sales outlets of IXOS cealco’s partners, as well as IXOS shops.
Purchasing network IXOS cealco | |
---|---|
Warehouse size: | 5,000 m2 |
No. of SKUs stored: | 5,000 |
No. of pallets received / day: | 50-60 |
No. of orders prepared / day: | 35-40 |
No. of lines making up each order: | 30-35 |
Gallery
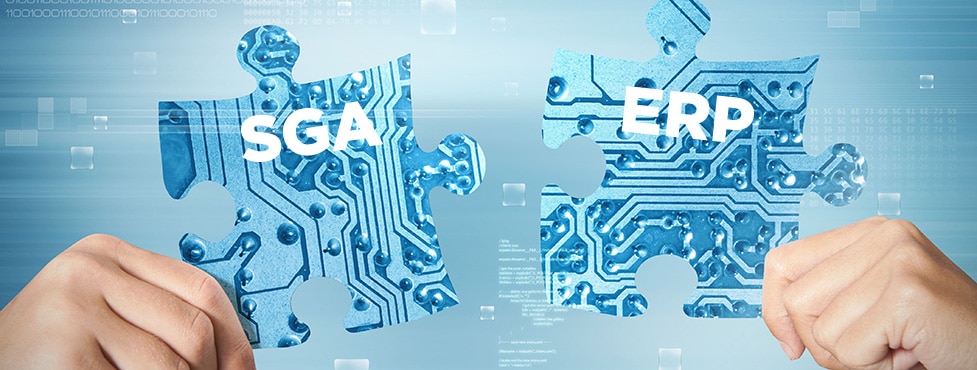
Easy WMS is integrated with IXOS cealco's Sage X3 ERP
Ask an expert