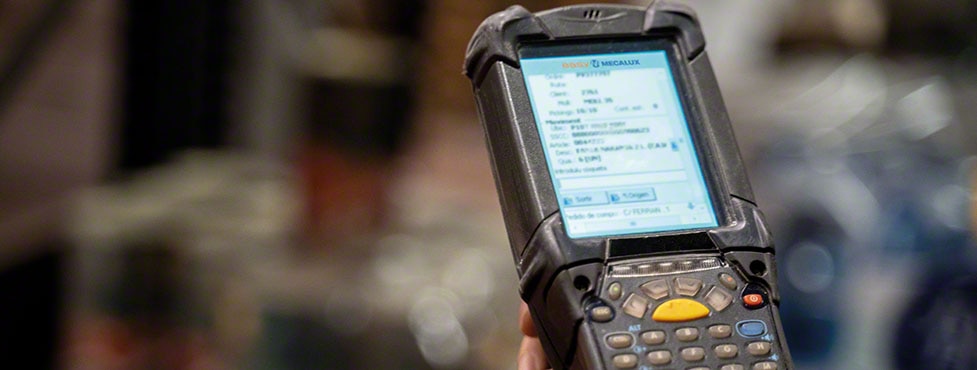
Jami Brisass: Easy WMS drives further growth
The WMS acts like the brain, coordinating and managing operations and exercing strict control of stock
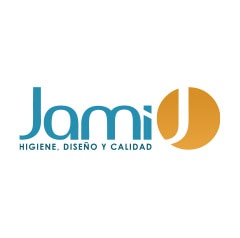
Productos Jami Brisass is a firm in constant transformation that specialises in bathroom products and accessories. Its top priority is to meet the changing needs of its customers and to embrace its future prospects. With a view to providing quality service and streamlining order preparation, the company has implemented Easy WMS. This warehouse management system developed by Mecalux carries out an extremely precise control of the 1,000 SKUs available in Jami’s warehouse and enhances its storage and order preparation capabilities.
Leveraging every opportunity
Founded in 1991, Productos Jami Brisass S.L. is a Spanish company with a long history of designing, manufacturing and marketing complete bathroom solutions for the hospitality sector. It has a catalogue of approximately 2,000 items including soap dispensers, hand dryers, water fountains and shower seats.
Jami does not miss a single opportunity to boost its business, so it transforms and improves its processes regularly. This strategy has led to stellar results: “We are undergoing a period of growth, embodied in the construction of a new 4,000 m2 warehouse in the city of Antequera (Andalusia), dedicated to the applicable logistics and assembly work,” boasts Jami General Manager José Ignacio Matesanz.
At present, Jami has two warehouses in the Andalusia region (one in Málaga and another in Seville). The installation in Málaga is the company’s central warehouse, as it is from there that the final distribution of the products to its customers all over Spain takes place.
This warehouse occupies 2,000 m2 where more than 1,000 SKUs of finished products are deposited. It consists of pallet racks that provide storage capacity for 1,900 pallets.
One of the special features of this storage system is that direct access to the goods facilitates and speeds up storage and order preparation. The lower racks are used for picking (either from boxes or directly from the pallets), and the upper racks are for storing the reserve products.
Previously, goods management was manual, i.e., operators organised the products as they arrived from production and then stored them. This operation was highly time-consuming, and mistakes were sometimes made, something Jami wished to prevent.
The company was adamant that it needed to implement a WMS because this would mean greatly improving its warehouse and, ultimately, its entire supply chain. The advantages are extremely appealing: having the necessary stock at all times to avoid service interruptions, spending the least possible time on operations and optimising flows and locations.
Advanced logistics
Logistics is one of Jami’s core activities; therefore, it needed to have software that would carefully manage all the warehouse processes (receipt, storage and order preparation and dispatch).
“After studying several proposals, we opted for Easy WMS, Mecalux’s warehouse management system, because we could easily link it to our ERP,” explains José Ignacio Matesanz.
Jami uses the Sage Murano ERP to organise information flows from all the company’s departments, including logistics. However, unlike the WMS, an ERP is not used to manage logistics processes since it is incapable of comprehensive inventory control.
The WMS acts as the brain that coordinates and directs operations, performing much tighter inventory control. Easy WMS has been integrated with Jami’s Sage Murano ERP to leverage all processes and, as a result, meet customer needs in the shortest possible time. The two software systems are connected via text files to transfer data and information continuously and bidirectionally.
In the warehouse, the WMS is responsible for supervising operators’ work and guiding them in the receipt of goods and in the preparation and subsequent distribution of the orders::
Receipt of goods
The ERP notifies Easy WMS of the arrival of products in advance. The WMS automatically prints a label for each SKU, which the operators have to place on the corresponding pallet. Most often, pallets are single-SKU and include all the items of the same SKU.
Once all the products have been received, the operators check that all processes were performed correctly and in accordance with the prior notification from the ERP. They use radiofrequency terminals so that the WMS can tell them which item to check and what to do with it afterwards. Operators receive the orders at the RF terminals and confirm that they have been carried out, thus minimising errors.
“Identifying the product from the moment it arrives at the warehouse helps to maintain a very strict control of the inventory. We have ironed out the kinks when it comes to locating goods when we need them,” says José Ignacio Matesanz. This control ensures traceability and allows the WMS to know the location of each item in all the processes.
Once the goods have been identified, the WMS assigns them a location, taking into account the type of item and its demand level. Easy WMS organises products according to whether they can be stored (waiting to be distributed when ordered) or whether they are intended to replenish the picking shelves.
Order preparation and dispatch
The ERP distinguishes between two types of orders: those that can be picked up at the warehouse and those that are sent to companies. In fact, the operation itself is the same, as the operators go around the warehouse to collect the SKUs. The only difference is that orders picked up from the warehouse are given priority, as these are placed by companies that have requested a particular item.
Operators must go to the warehouse immediately and prepare it as quickly as possible. Some of these orders are even prepared by cross-docking, i.e., they are delivered the moment the goods are received, without having to be stored. Orders for companies, meanwhile, include all the goods that Jami distributes to its customers on a regular basis. Through radiofrequency terminals, Easy WMS tells the operators which aisle to go to and which slot to locate; once there, it tells them how many items to remove.
Once the orders have been closed, they are grouped together in the dispatch area. Easy WMS organises them based on the transport route to ensure, for example, that orders to be delivered at the end of the journey are loaded onto the lorry first.
Quality service
The company has put its supply chain at the forefront with a management system capable of directing and optimising all warehouse operations. By having all its goods under control, Jami can organise its operators’ work more precisely and take measures that help to increase their throughput more easily.
“If there is one thing we have gained with Easy WMS, it is that we have eliminated the mistakes and problems that searching for the goods entailed,” says José Ignacio Matesanz. After implementing the Mecalux WMS, Jami has increased its warehouse productivity by 50%. In practice, this is translated into much faster order preparation and dispatch, and, therefore, better service for the hundreds of customers waiting to receive the products they have purchased.
José Ignacio Matesanz - General Manager of Productos Jami Brisass
“We’ve turned our supply chain around. Easy WMS assigns a slot to each product as soon as it arrives in the warehouse and, thus, has each SKU located. We now have greater control over the goods.”
Advantages for Productos Jami Brisas
- Redesigned logistics: Jami has completely transformed its supply chain. From manually managing products, Easy WMS is now able to manage them automatically, resulting in a 50% increase in productivity.
- Controlled goods: Easy WMS knows the exact location of the 1,000 SKUs available in the warehouse. Thus, its traceability is very rigorous.
- Guidance and supervision: the WMS helps operators to prepare orders. Since they receive orders on what products to pick up and where to slot them, mistakes are minimised.
Ask an expert