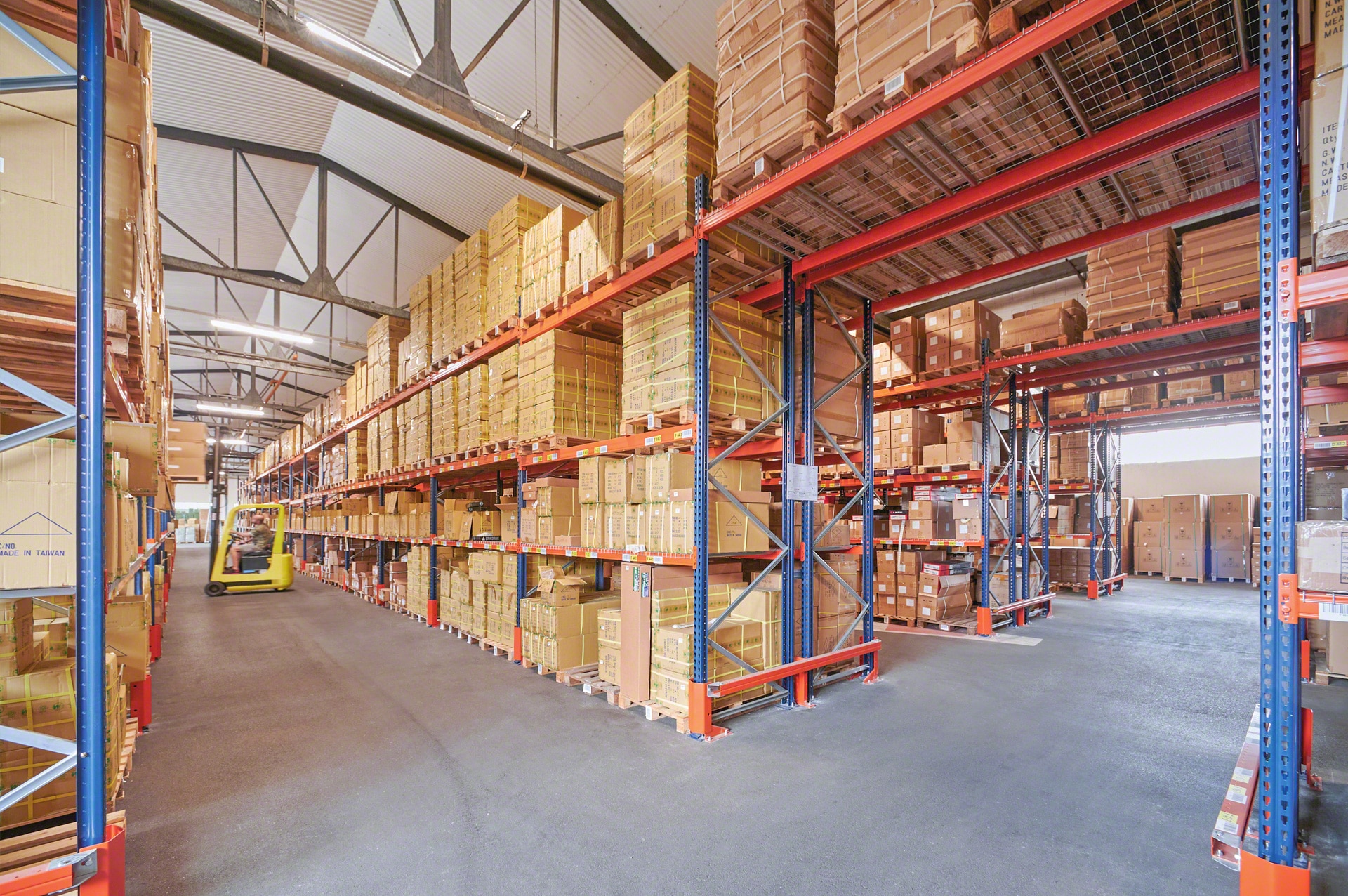
Integrated logistics solution for airsoft e-tailer Jolly Softair
Jolly Softair, the largest e-tailer of airsoft products in Italy, tackles the surge in online orders with Mecalux software.
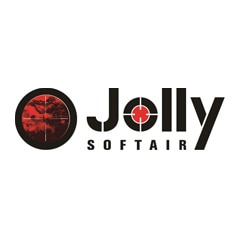
Jolly Airsoft, a marketer of airsoft products, has digitalised its warehouse in San Marino with Mecalux software. Easy WMS monitors goods in real time and organises order fulfilment for online customers.
About Jolly Softair: leisure and sports
With over 40 years of experience, Jolly Softair is a B2B (business-to-business) trading company headquartered in San Marino. It is primarily engaged in the sale of merchandise for airsoft (a game played with high-pressure air guns). Jolly Softair also markets archery gear, knives, optical devices and apparel and accessories for outdoor activities.
- Founded in: 1981
- International presence: 1,300+ customers worldwide
- Storage area: 5,000+ m²
CHALLENGES
|
SOLUTIONS
|
BENEFITS
|
---|
“Digitalising our logistics processes is essential for gaining competitiveness,” says Daniele Albani, CEO of Jolly Softair. The e-commerce airsoft specialist has relocated to a new centre in San Marino to centralise its logistics operations and cope with the growing number of online orders it has seen in recent years.
“We used to have several facilities and we’d prepare and distribute online orders from the main warehouse. We didn’t have a software program to organise operations; all processes were paper-based managed. As the business began to take off, we reached a critical point where our facilities could no longer accommodate any more merchandise or keep up with the pace of work. It was then that we made the decision to move to our current warehouse. Now, all processes take place under one roof,” says Albani.
When outfitting the new centre, Jolly Softair sought out a logistics provider that would optimise its operations with advanced storage and management systems. “We first got in touch with a company in Milan that conducts feasibility studies and they provided us with a list of storage system suppliers. In the end, we chose Mecalux because it offered us the best price and service. What most convinced us was the fact that Mecalux presented itself as an all-in-one provider of storage systems and software,” says Albani.
With this new warehouse, the airsoft retailer has completely overhauled its logistics operations. “We’ve installed two Mecalux storage systems: pallet racking and picking shelves. We’ve also deployed the Easy WMS warehouse management system to efficiently organise 7,000 SKUs and streamline order picking,” says Albani.
Advanced logistics management
The transition from manual to digital goods management has been a game-changer in Jolly Softair’s warehousing processes: “We’ve noticed a huge improvement in how our operations are structured. Processes are now much less gruelling for our operators, who no longer have to expend so much energy. This has undoubtedly raised the quality of their work. Digitalisation has enabled us to reach our sales targets,” says Albani.
By digitalising operations with a flexible, scalable software program like Easy WMS, Jolly Softair can adapt to business changes such as increases in SKUs and orders. Software as a service (SaaS) technology allows operators to access the WMS’s functionalities from any browser or device with an internet connection.
“The Mecalux software is extremely intuitive and user-friendly. After receiving training, operators master it very quickly,” says Albani. Easy WMS plays a vital role in all processes in the centre. These range from receiving through to the processing and shipment of online orders for over 1,300 customers around the globe. Likewise, the program tracks the status of thousands of SKUs in real time.
Easy WMS has also been integrated with Jolly Softair’s ERP software, enabling seamless and bidirectional communication between the two systems. Both programs transfer data and information that are fundamental for optimising all logistics operations performed in the facility. For example, Easy WMS notifies the ERP system of replenishments so that it can coordinate purchases from suppliers.
Mecalux has also implemented two additional modules that expand Easy WMS’s features: Warehouse Slotting Software strategically organises goods, while Multi Carrier Shipping Software includes advanced functionalities to streamline the packing, labelling and shipping of online orders.
Warehouse Slotting Software: product control
“We implemented the Warehouse Slotting Software module to improve the distribution of products in the facility based on their turnover rates. Now that the items are organised properly, operators travel the shortest possible distances to store and pick orders,” says Albani.
The Warehouse Slotting Software module — an extension of Easy WMS — determines the best location for each product. This module is crucial for Jolly Softair because its logistics centre stores 7,000 SKUs of various sizes and characteristics, distributed across two different storage systems.
An efficient stock allocation strategy, based on rules and algorithms, significantly boosts throughput in operations such as receiving, replenishment and order picking. Operators merely have to read the barcode on each product with their RF scanners and the Warehouse Slotting Software module assigns it the ideal location.
When distributing stock in the facility, the module takes into account the physical attributes of the merchandise and the main operation performed: e-commerce order picking. Thus, for example, products with the highest demand level are more accessible to make their entries and exits more agile.
Multi Carrier Shipping Software: agile dispatch
“We installed the Multi Carrier Shipping Software module to manage shipments made through our two carriers in a unified way,” says Albani.
The module communicates directly with the software of the delivery companies to facilitate and expedite shipments. Multi Carrier Shipping Software sends documentation to the carriers (indicating the number of parcels to be delivered, for example) and the agencies provide data to generate the labels and tracking numbers. This way, when the carriers arrive at the warehouse, they simply collect the prepared orders, as all the information they need is already in their system automatically.
Additionally, Multi Carrier Shipping Software organises the packaging and labelling process. The system guides the operators at all times, showing them which items to pack and whether they should use a single box or multiple boxes for the same order.
To distribute the goods most effectively, the software also groups orders: it consolidates different shipments into a single batch based on route, agency, or parcel recipient. Thanks to the supervision of Multi Carrier Shipping Software, operators prepare packages more rapidly while guaranteeing that no mistakes have been made in order picking.
Centralised logistics tailored to e-commerce
“We’re a leading player in the industry at the European level and we want to maintain the high sales volume we’ve achieved in recent years. Starting in 2020 — despite the pandemic — our business has grown exponentially. Like all companies, our goal is to keep expanding,” says Albani.
Jolly Softair is on course to do just that, thanks to the successful strategy of centralising and digitalising its logistics processes. With its newly implemented flexible and scalable software, the company can effortlessly adapt to evolving business dynamics and seize future growth opportunities. Moreover, Easy WMS has revolutionised Jolly Softair’s supply chain, making it more efficient and competitive while ensuring meticulous traceability of products in the warehouse.
We highly recommend Mecalux as a storage systems and software provider because it puts the client front and centre. The fact that Mecalux offers storage solutions integrated with software is one of its key strengths.
Gallery
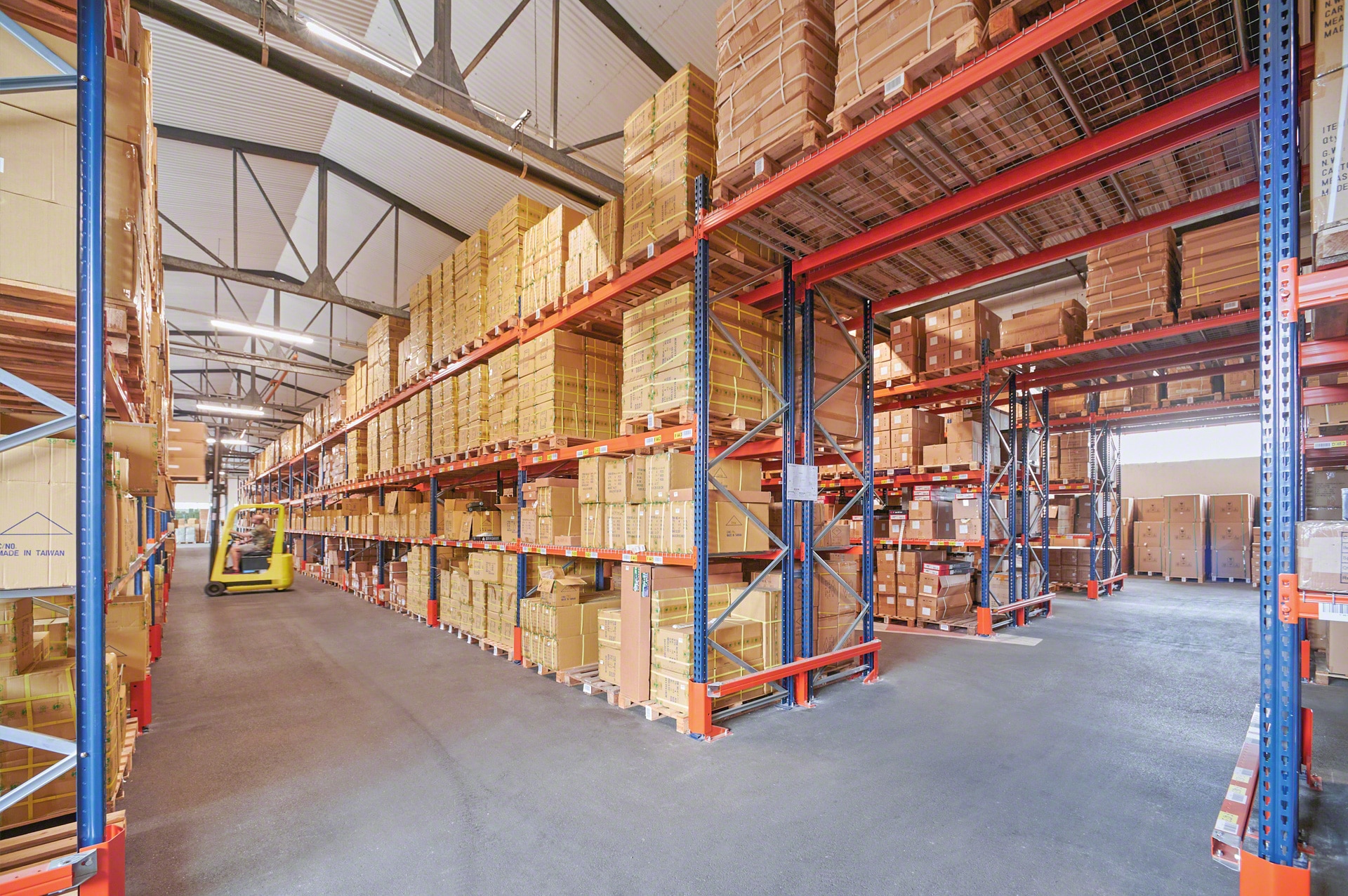
Warehouse of e-commerce airsoft product retailer Jolly Softair in San Marino
Ask an expert