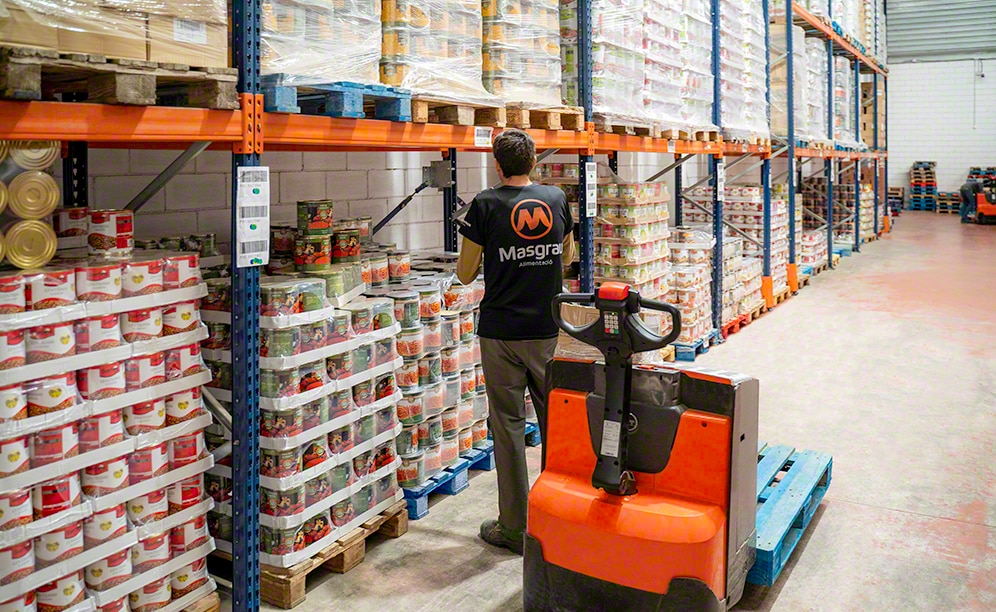
Masgrau Alimentació renovates the management of its warehouse with Mecalux WMS
Mecalux's WMS directs the preparation of Masgrau Alimentació's orders
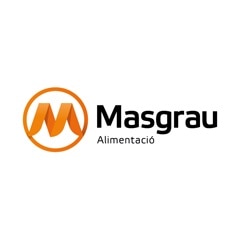
Masgrau Alimentació, a dry food distributor for restaurants, hotels and other local groups and entities, has super charged its supply chain competitiveness thanks to Easy WMS, Mecalux’s warehouse management system. The company has rolled out the WMS in its distribution centre in Girona (Spain) to organise its catalogue with over 3,000 different SKUs and enhance preparation of a large volume of orders: up to 250 a day.
About Masgrau Alimentació
Masgrau Alimentació is a dry goods distributor (soft drinks, biscuits, cereals, juices, sugar, salt, etc.), which supplies hotels, restaurants, airlines, hospitals or nursing homes, among others.
All staff work hard to exceed customer expectations and search for innovative solutions to anticipate their demands. To have a wide and varied catalogue of products and so guarantee that its clientele does not go without, the company collaborates with some of the most well-known food brands in the Spanish market. Plus, since 2001, it also carries its own brand name goods called Serhos.
Challenges of food distribution
Masgrau Alimentació has more than 50 years of expertise in the distribution sector, so it is well aware of the market situation. Companies like these run highly complex logistics and must meet a multitude of demands:
- Manage multiple SKUs. The portfolio of Masgrau Alimentació includes over 3,000 items of various sizes, weights and demand levels.
- Flexible operations. The company must adapt to the specific wishes and demands of each individual customer.
- Handling products. As these are foodstuffs, it is absolutely essential that they are kept in proper condition to prevent them from spoiling or being distributed in poor condition.
- Expiry date. The products have a limited expiry date, which requires a tight grip on stock control.
- Agile distribution. Customers expect short delivery times for their orders.
To solve all these issues and make its Riudarenes (Girona) warehouse as productive as possible, Masgrau Alimentació has deployed Mecalux’s Easy WMS warehouse management system.
One priority when installing the software was being able to manage the stock efficiently because, according to Alex Masgrau, head of the company’s logistics department, “it was very important if we wanted to broaden our SKU base.”
The company was also interested in an intuitive, hands-on system that would help operators get the job done. “We needed the new team to learn how to use the system quickly,” Masgrau explained. The company hit the nail on the head with Easy WMS, because this system plays an integral part in the operators’ work: it tells them what to do with each product, where to slot the goods or where to locate the SKUs they need. With this supervision, workers concentrate on their job and avoid mistakes.
Alex Masgrau - Logistics Department Manager at Masgrau Alimentació
“Thanks to Easy WMS, we have gained better control over our warehouse processes: inventory statuses, expiry dates, lots, staff preparing orders, etc. With all this data, we can make strategic decisions to improve operations.”.
A sectored warehouse
The Masgrau Alimentació warehouse has been divided into three sectors. Each of them groups products with similar characteristics:
- Smaller-sized products (boxes of biscuits, cereal, etc.). This area contains Mecalux pallet racks with shelving for picking on the bottom levels. The reserve pallets are housed in the upper levels, so picking shelves can be replenished quickly.
- Large products (pallets with packaged sugar, salt, macaroni, etc.). In this area, Mecalux has installed pallet racks and picking is done directly off the pallets on the lower tiers. Spare pallet loads (i.e. reserves) are also found in the upper levels.
- Heavy and bulky products ((juices, water jugs, soft drinks, etc.). A floor buffer area has been set aside for ground level storage.
The receptions area becomes one of the most essential areas of the warehouse to get products organised. Every day operators are in charge of sorting and organising the incoming pallets before placing them where they belong.
For error-free completion of this task, workers follow the Easy WMS’s instructions throughout. The system assigns a storage location to the merchandise based on the product type, its dimensions, and the level of demand. It then points out to the operators the area where each particular article is to be stored.
The shipping area is also known for its high volume of product movements. Pallets are grouped there according to their corresponding order or transport route. This way, they can be loaded into the distribution vehicle faster. Orders are sent to Masgrau Alimentació customers in Catalonia and Andorra.
Maximum pick performance
Order picking is the core operation of the distribution centre. And, each day, it fulfils 250 orders with an average of 17 lines each. For this reason, one of the primary functions of Easy WMS is to maximise operator output by locating the SKUs that make up each order in the warehouse.
“We are really impressed with the WMS because it is very flexible and has completely adjusted to our work pace,” Masgrau said. Easy WMS has enhanced picking in several ways. First, thanks to successful product organisation, all goods are identified from the moment they arrive at the warehouse and arranged according to their dimensions and demand level. As a result, workers know exactly where to head when picking.
Second, operators use RF devices to receive orders from the WMS in real time and confirm they have been fulfilled. Easy WMS’s supervision ensures that operators concentrate on their work and, also, wipes out errors.
Third, Easy WMS has designed a picking route that streamlines operators’ routes. These routes are sensitive to product measurements. For this reason, operators must collect bulky products first, then large ones, and finally smaller ones.
Fourth, contact between Mecalux’s WMS and Masgrau Alimentació’s ERP acts a bridge so that the warehouse has all the required products when assembling orders. Easy WMS keeps tabs on stock status in real time and, with this information, arranges restocking when locations become empty and tells the ERP to purchase more product from suppliers.
Constant growth
Indeed, warehouse management software is a strategic ally for any company. Not only is it a work tool that efficiently manages warehouse operations and resources, it is also a system set up to deliver maximum supply chain competitiveness.
Choosing and purchasing the right WMS is a big responsibility. The people in charge of Masgrau Alimentació wanted to be absolutely sure before making any sort of decision. In the words of Masgrau, “we visited another company’s warehouse where they held many more SKUs than we did, and we saw that Easy WMS was working smoothly, which sold us on the idea. This was the WMS we needed.”
Easy WMS is a system that will grow alongside Masgrau Alimentació in its plans for the future. “We want to become the largest supplier of dried, refrigerated and frozen food in Catalonia,” the head of the logistics department emphasised. To achieve this, the WMS raises the warehouse’s productivity so that the company can tackle any project, always putting customer satisfaction first.
Advantages for Masgrau Alimentació
- Quick picking: Easy WMS helps Masgrau Alimentación operators achieve their goal of preparing 250 orders per day.
- Error-free operations: overseeing all operations through the Mecalux warehouse management system removes any potential error making.
- High productivity: the WMS has designed a picking route for operators. This optimises and minimises the number of trips taken by the team.
Masgrau Alimentació warehouse | |
---|---|
No. of stored SKUs: | 3,000 |
No. orders prepared / day: | 250 |
No. of pallets distributed per day: | 100 |
Gallery
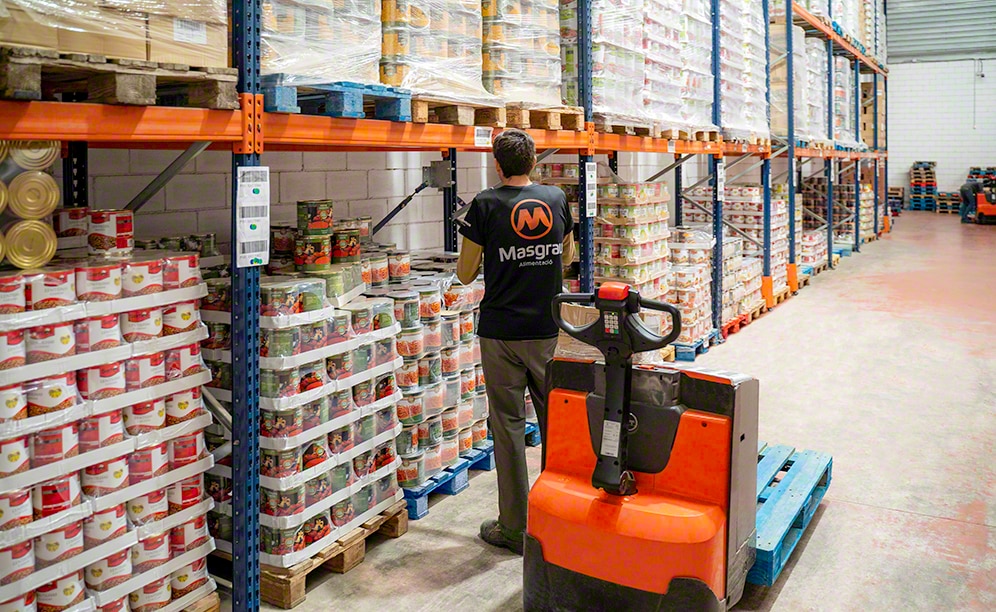
Masgrau Alimentació manages more than 3,000 SKUs in its warehouse
Ask an expert