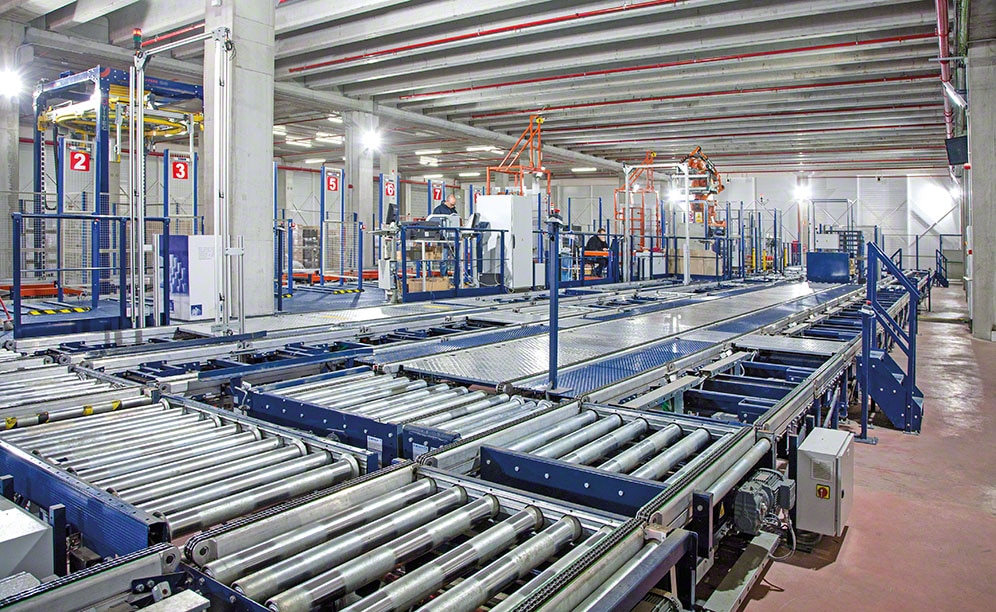
Nupik Internacional: centralised, interconnected and automated logistics
Nupik has a modern and automated logistics system that allows it to provide rapid, high-quality service
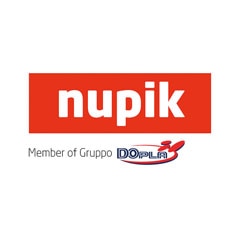
A leader in the manufacture of sustainable products for the Hotel and Catering and Retail industries, Nupik Internacional has concentrated all its production and storage in the town of Polinyà (Barcelona). It has its central plant where the production lines, warehouses and offices are located. Technology and innovation are part of its logistics processes, as they ensure high efficiency, mainly in order preparation and dispatch. Mecalux has set up an extensive picking area where up to 345 orders a day are completed in sequence, following the instructions given by Easy WMS. Over the last year, the company has moved a total of 789,000 pallets to its customers in Spain and abroad.
Committed to sustainability
Founded in 1985, Nupik Internacional is a leading manufacturer of single-use tableware, such as plates, glasses, cutlery and containers, for both industrial and domestic use. With a staff of nearly 200 employees, Nupik exports to France, the United Kingdom, Portugal, the Netherlands, Russia and several Arab countries. The company markets its own brand and allocates part of its production to supplying other brands.
Committed to and focused on sustainable industrial development, it has launched Nupik NaturGo, a range of sustainable and recyclable products. These products are made from raw materials such as cassava, sugar cane, paper and wood pulp. All these products come from sustainable and controlled forestry operations.
Bustling logistics
Determined to limit logistical dispersion and, in the words of Eduard Pinosa, Nupik’s Logistics Manager, “to concentrate all our activities in one space,” the company built its central plant in the municipality of Polinyà (Barcelona). In a 40,000 m², area it carries out production, storage, order preparation and dispatch.
“Centralising all our logistics was a key objective for us. Unifying storage with production (where our activity runs continuously, 24 hours a day), has provided us with significant cost savings,” adds Eduard Pinosa.
It was clear to Nupik that it had to automate all possible processes, especially the operations related to the flow of goods and picking.
Stacker cranes, pallet conveyors, transfer cars, pallet lifts and an anthropomorphic robot help to prepare and distribute up to 345 daily orders (in peak season) as quickly as possible. “Automating our logistics has helped us consolidate the increase in sales,” says Pinosa.
The Nupik plant has two storage sites. Each of them has automated systems that offer a total storage capacity of 28,000 pallets with 3,890 SKUs.
One of the sites consists of an automated clad-rack warehouse with a capacity for 24,188 pallets of raw materials and finished products. As the installation is clad-rack constructed, the racks not only support the load units, but also the rest of the building.
The other site, right next to the first, consists of an automated storage area, as well as the picking and dispatch zones. A reception area for goods from other production centres (around 950 pallets per day) has also been set up inside this building.
The Nupik plant is notable for its interconnection. The two storage sites are connected by conveyors located in a raised tunnel. In turn, the storage areas are automatically connected to production via a bi-directional underground tunnel. The conveyors provide a lot of agility in the transport of goods and ensure continuous and controlled movement.
Six pallet lifts have been installed to link the different heights of the warehouses very smoothly and efficiently. They also communicate the clad-rack warehouse with the production site.
Two automated storage systems
Both warehouses are equipped with automated systems:
- An automated high-density system for the most in-demand products (A and B). It consists of twin-mast stacker cranes and automatic shuttles that move the pallets around inside the channels. It is an ideal storage system for Nupik, as it manages many pallets for each SKU.
- An automated warehouse with double-deep racking served by stacker cranes for low rotation products (C). The majority of these SKUs are destined for the picking area, except for customised products that are transferred on full pallets — without the need for splitting — directly to the dispatch area.
To control such a large number of SKUs and products, the Mecalux Easy WMS warehouse management system has been implemented. “We wanted software that would suit our operations and integrate easily with the SAP ERP. Easy WMS is ready to cope with our huge workload; it is very intuitive and easy to use,” says Nupik’s Logistics Manager.
This software identifies the pallets as they arrive from production (859 per day) and assigns them a slot in one of the two warehouses. Easy WMS incorporates pre-parametrised rules that follow criteria for optimisation and maximum productivity to define a location for each pallet based on its rotation. By having each item identified, Easy WMS knows the stock status in real time and can report the exact location of each product at the precise time it is needed.
Eduard Pinosa - Logistics Manager of Nupik Internacional
“The two warehouses have exceeded all our expectations. Having automated logistics helps us to further improve our processes to meet customer requirements. Our challenge is to be present at a national and international level; to this end, we have surrounded ourselves with storage systems that enable us to compete in terms of automation, safety and service.”
Order preparation
The picking area is designed to prepare and dispatch a large number of orders in sequence in the shortest possible time.
“Three operators can get all the orders ready in a single shift. Our business is seasonal, and, on the dates with the highest volume of work, up to 345 daily orders with an average of 14 lines each can be prepared,” points out Eduard Pinosa.
A total of 32 orders can be prepared simultaneously in three different ways:
- Automatic picking. An anthropomorphic robot can prepare three orders at the same time and is capable of handling up to 150 layers/hour or, in other words, more than 1,000 boxes/hour. The Easy WMS warehouse management software optimises the stackability and sequencing of loads, thus saving time and minimising costs.
- Semi-automatic picking. The robot starts to prepare the order; once it has finished its task, the transfer car moves the pallet to one of the sixteen manual picking stations. A re-circulation area has been set up in which pallets that are missing goods are held to complete the order, thus ensuring that order preparation is not slowed down.
- Manual picking. The manual picking stations are equipped with PTL (pick-to-light) devices that show the operators how to prepare each order, ensuring efficient and error-free picking.
Sequencing is one of the key areas in order preparation. Easy WMS takes care of sending the SKUs to the picking area so that the shipments are prepared according to the order in which they will be delivered to the customers. In addition, the conveyor circuit, when performing the recirculation function, supplies the various picking stations at the right time.
Sequencing of dispatches
Once the orders have been completed, the transfer cars take them to the stretch-wrapping area; this process takes place at a rate of more than 70 pallets/hour. The pallets are then labelled and transported to the dispatch area by means of pallet lifts. Those pallets that have not passed through the picking area are labelled in the shipping area and dispatched immediately.
A total of 24 live preload channels, which can accommodate 11 pallets each, have been arranged. There, the goods are organised, following the sequence of orders established by Easy WMS, waiting to be distributed at the right time.
A complete preload is formed with pallets from three channels, so up to eight lorries can be left ready in advance. The transfer car, which can take two pallets at a time, sorts them into the corresponding channel according to the orders given by Easy WMS. The goods are grouped by route, vehicle, customer, delivery order and other characteristics, thus completing the entire sequencing process.
“At the time of peak demand, we ship around 2,400 pallets a day. In this last year, we moved a total of 789,000 pallets,” says Eduard Pinosa.
Environmentally-friendly range
Recently, Nupik launched Nupik NaturGo, a range of sustainable products that respond to the growing demand from a public that is increasingly concerned about looking after the planet. These items include glasses and cutlery made only from raw materials of sustainable origin.
Just a few metres from the automated clad-rack warehouse, the company has built a new production plant specifically dedicated to this product line. Mecalux has equipped its storage area with pallet racking and drive-in racks with a capacity of 4,070 pallets. The pallet racking stands out for its adaptability to any type of load, with variable weights and volumes. The high-density racks can hold up to ten pallets in depth.
Consolidation of international expansion
Nupik has a modern logistics system that allows it to provide swift, high-quality service. The technology helps it to prepare and dispatch 345 orders a day to customers in Spain and abroad. In addition, with Easy WMS monitoring, orders can be prepared sequentially, quickly and error-free. Centralising and connecting its logistics activity with production has resulted in a significant improvement in Nupik’s entire supply chain. The direct communication between the warehouse and the company’s production lines has meant significant reductions in goods transport and handling costs.
Advantages for Nupik Internacional
- Centralised logistics: unifying and connecting production lines, warehouses and offices has marked a turning point in Nupik’s supply chain and has led to significant savings in logistics costs.
- Maximum control: thanks to the WMS from Mecalux, Nupik controls all the processes and operations that take place throughout the whole plant. It also monitors the goods precisely, from the time a product leaves the production centre until it is shipped in sequence.
- Automatic operation: automation has helped Nupik to provide uninterrupted service 365 days a year. In addition, it minimises errors and reduces the number of goods movements.
Gallery
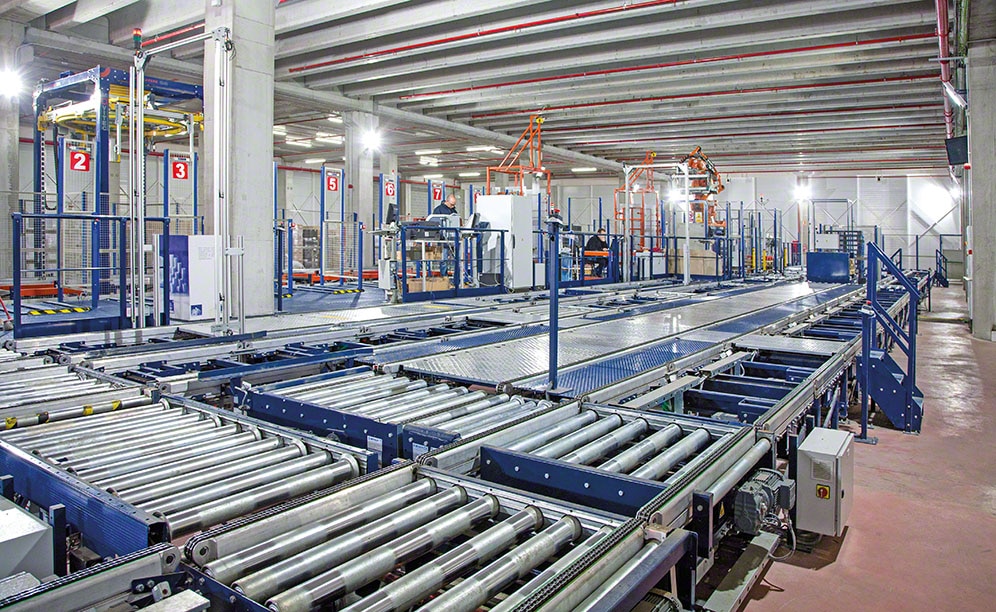
Nupik Internacional's automated warehouse with disposable products in Barcelona
Ask an expert