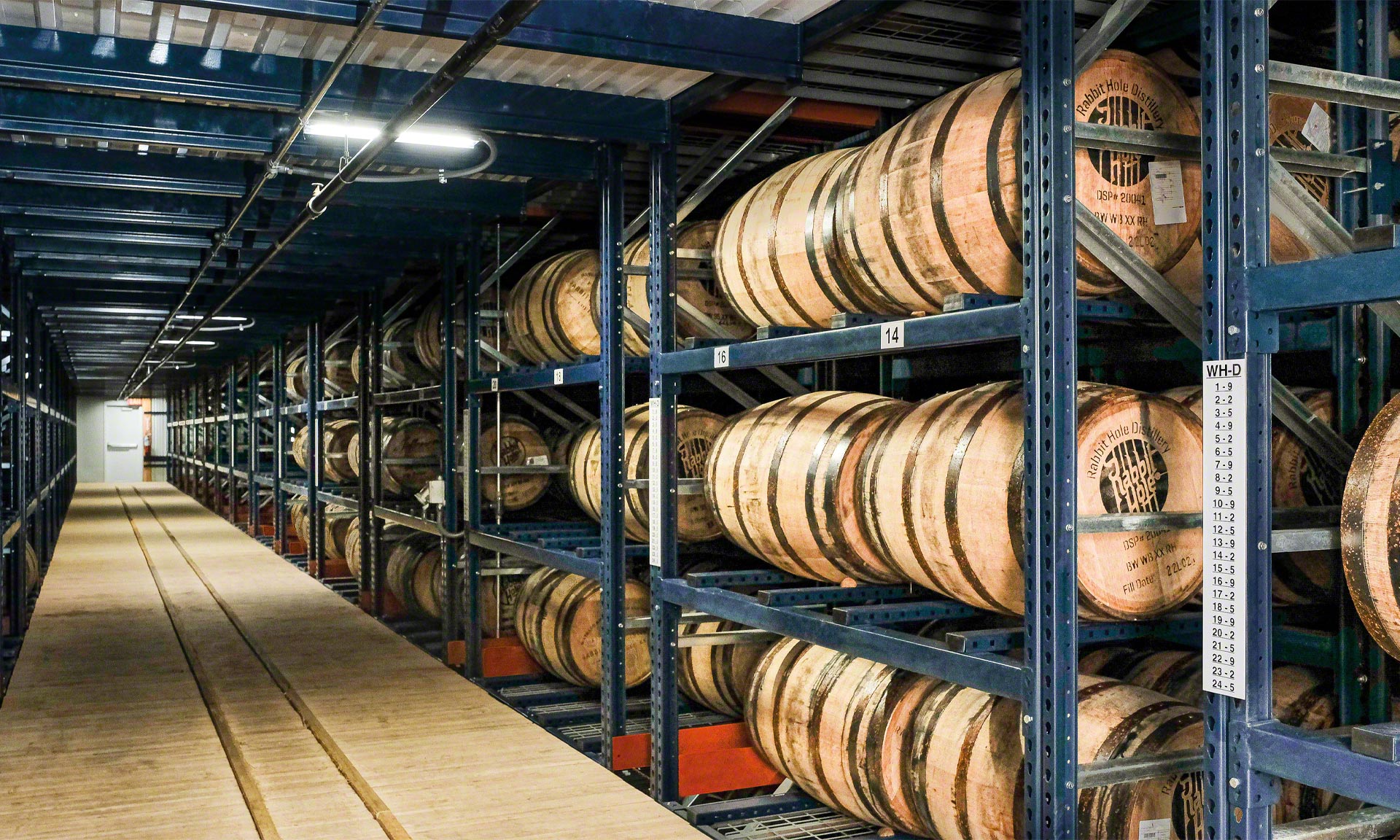
Rabbit Hole Distillery: high-density warehouse for bourbon whiskey barrels
Rabbit Hole Distillery installs a high-density system to store 24,500 barrels of bourbon whiskey.
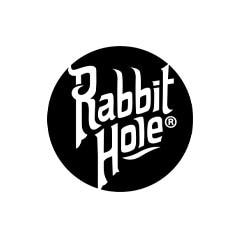
Rabbit Hole Distillery has installed an innovative solution to store thousands of bourbon whiskey barrels during the ageing stage. The company has built a clad-rack warehouse to store 24,500 charred oak barrels in just over 1,000 m².
Rabbit Hole Distillery: a distillery that combines tradition and innovation
Kaveh Zamanian founded Rabbit Hole Distillery in 2012 after his family moved to Kentucky, leaving behind a successful career as a clinical psychologist and psychoanalyst to start his own spirits company. He put everything on the line to start a liquor brand that would eventually put Rabbit Hole at the forefront of the American spirits category, producing 27,000 barrels a year.
CHALLENGES
|
SOLUTIONS
|
ADVANTAGES
|
---|
Innovation and creativity have always been at the heart of Rabbit Hole Distillery, a producer of fine spirits located in Louisville, Kentucky. The company prides itself on honouring the past by restoring creativity to the craft of producing spirits such as bourbon whiskey, rye whiskey, barrel-aged gins and more.
Rabbit Hole was looking for an innovative way to store thousands of bourbon whiskey barrels during the ageing stage, where the beverage is left to rest for four to six years before being bottled. The company’s main need was to maximise storage capacity and guarantee safe goods handling. At the same time, it had to continually preserve the quality of the product and the safety of the operators. Another of Rabbit Hole’s priorities was to guarantee that the warehouse was prepared to adapt to the drastic temperature changes in winter and summer and to overcome any possible ground movement. Temperature changes are extremely important in the ageing process because they cause the whiskey to expand and contract inside the barrels, resulting in a unique flavour, colour and aroma.
With all these requirements, the distiller turned to Interlake Mecalux and partner A&S Solutions to develop a solution at its Campbellsburg, Kentucky, location that would do just that. After analysing Rabbit Hole’s current needs, Interlake Mecalux and A&S proposed building a clad-rack rickhouse, which is a storage space for bourbon whiskey barrels during the ageing process. This warehousing structure is unique in that it is the racking structure that supports the building façade and roof. This would be one of the safest ways to house the facility’s 24,500 barrels, according to Alex Smith, A&S Vice President: “The great thing about partnering with Interlake Mecalux on installing this storage solution for the distilled spirits industry is the effectiveness of its storage system.”
High-density storage system
Rabbit Hole’s new clad-rack rickhouse stands out for its maximisation of space thanks to a high-density storage system. In just over 1,000 m², the company can now store 24,500 charred oak barrels. To store the goods compactly, the racks were designed with a depth to accommodate up to 24 barrels, each weighing 250 kg.
Safety was a major priority when designing and installing the warehouse. Capable of withstanding 6,105 tonnes, the facility is equipped with numerous devices to ensure the safety of the products and the structure.
“A focus on this system is safety. It has safety grating, so if somebody were to roll a barrel and slip, we’re ensuring that we’re protecting the products and the structure,” Smith says. “And then we’ve got corrugated decking underneath the floors. This acts as a fire barrier. It’s also a structural component for employees walking on each level who are rolling barrels”, says Smith.
In addition to improved fire protection, the storage system’s racking is seismic rated to protect against tremors in the event of an earthquake. Reinforced profiles, numerous safety accessories and a non-rigid structure allow for the rack to perform better against any seismic movements.
Another unique feature of this 455-tonne clad-rack warehouse is that it’s easy to assemble and repair. If a bolted rack component is damaged, only that element needs to be replaced. This is done both quickly and easily, Smith says. “Typically, in the US material handling industry, your uprights and frames are all welded. We’re ensuring that we can replace a component to the system itself quickly and affordably. The focus was easy preventable maintenance and if something were to rust inside this warehouse storing 24,500 bourbon whiskey barrels, we can just simply unbolt a bolt, pop the strut out and put a new one in in five minutes,” Smith adds.
Different temps: key to the ageing process
The rickhouse design also took into account temperature changes in Kentucky, which can range from -12 to 48 °C depending on the time of year. In the summer heat, the liquid expands, penetrating the pores inside the wooden barrels. When the temperature drops, the liquid contracts, extracting the aromatic components and flavours from the oak. Thus, with each season of the year, the bourbon whiskey in storage ages, gaining more flavour, aroma and body.
The location of the barrels in the warehouse also affects the ageing process of the final product. Barrels stored at the top are exposed to a higher temperature, which causes the whiskey in the barrels to age faster. By contrast, barrels placed on the lower levels remain cooler, slowing down the ageing process. To regulate and compensate for the difference in temperature between storage levels, the facility has been designed to maximise airflow, both cold in winter and hot in summer.
Fluctuations in temperature and humidity — which favour the ageing of whiskey — can cause the components that make up the structure to deteriorate. To increase safety, cataphoresis, an immersion painting method based on a cathodic electrodeposition process, has been employed. Cataphoresis also provides a more uniform finish as well as high resistance to corrosion.
Warehouse designed for whiskey ageing
Oftentimes, clad-rack warehouses are the most economical storage solution when a new facility is necessary. These structures can be built with a variety of racking systems such as adjustable, drive-in and push-back racking. Moreover, with the current demand for industrial land at a premium, clad-rack warehouses can be the best choice, especially when an accelerated construction schedule is required.
For Rabbit Hole Distillery, the decision to construct a clad-rack rickhouse was a simple one, as it offered a unique solution for storing close to 24,500 barrels for long periods of time safely and economically. And much like Rabbit Hole places a value on creativity when crafting high-quality spirits, the structural system of this clad-rack warehouse enabled Interlake Mecalux and A&S Solutions to offer a more creative, custom, fast and efficient solution.
The great thing about partnering with Interlake Mecalux on installing this storage solution for the distilled spirits industry is the effectiveness of its storage system.
Gallery
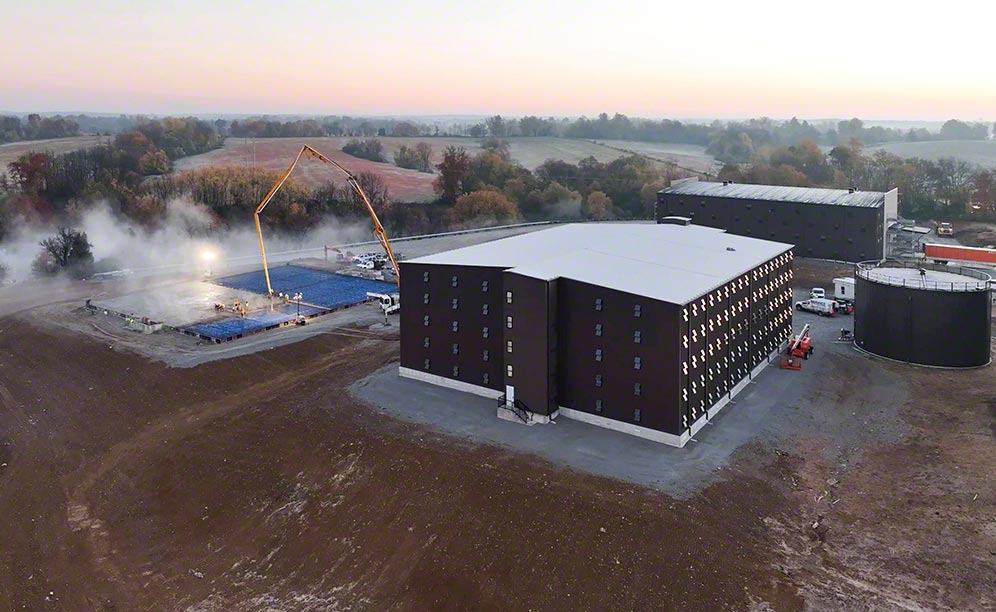
Rabbit Hole Distillery’s warehouse for bourbon whiskey
Ask an expert