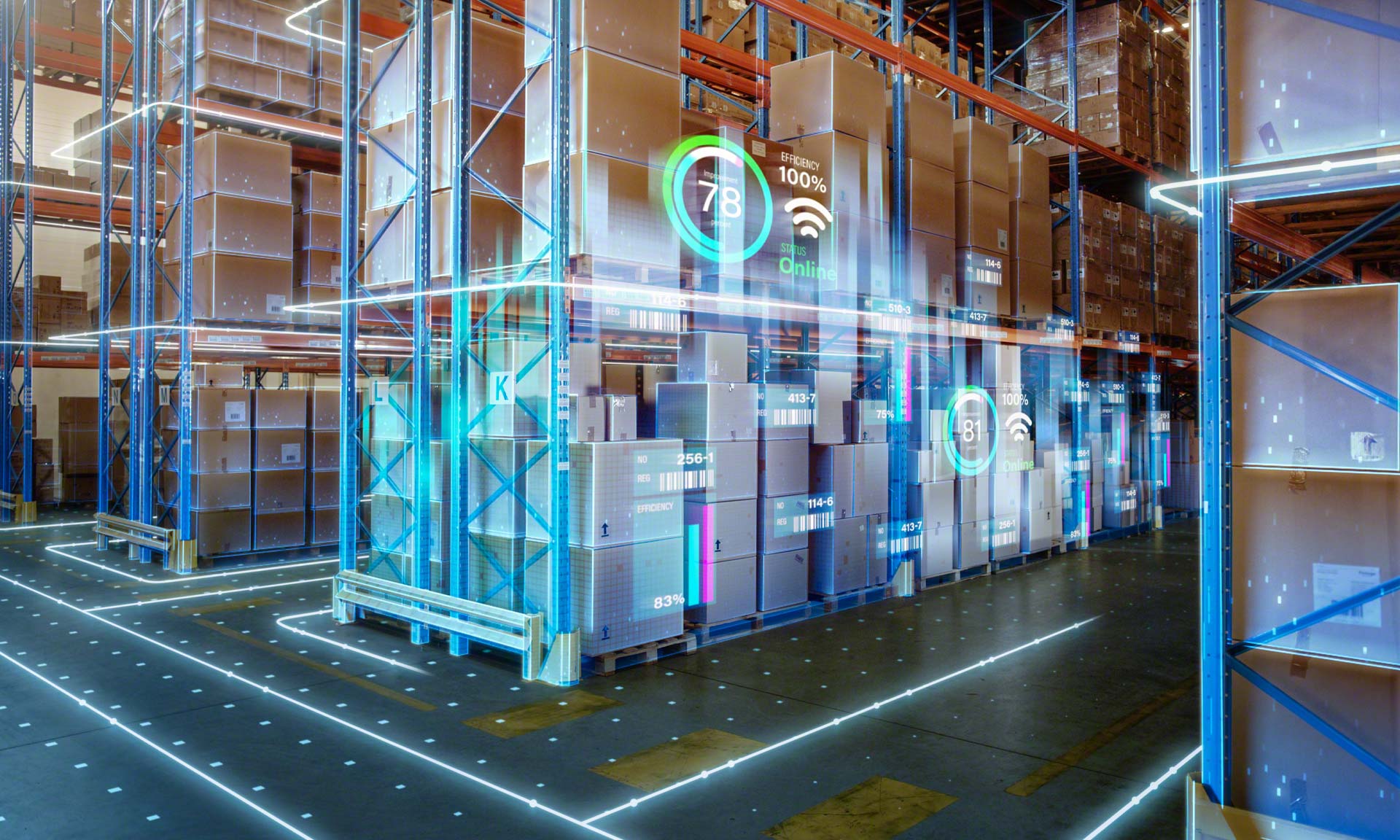
Digital warehouse: speed and real-time information
Sal Vesta has gone from outsourcing its logistics operations to managing them in-house with Mecalux's Easy WMS.
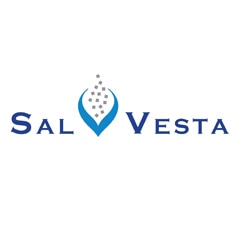
Sal Vesta, a producer of high-purity salt, has implemented Easy WMS warehouse management software from Mecalux in its logistics facility. With this software, the company accurately monitors all its SKUs and has optimised its warehouse operations.
Sal Vesta: on the road to more sustainable mining
Founded in 2017, Sal Vesta is a Spanish company dedicated to the production, packaging and sale of high-purity salt for human and animal consumption as well as for water treatment. Sal Vesta’s production plant in Bages — one of the most significant mining regions on the Iberian Peninsula — was started up with the aim of commercialising salt on the international market.
- Founded in: 2017
- Location: Sant Fruitós de Bages (Spain)
- Annual production: over 165,000 tonnes of salt
- Markets: Spain, southern France, Italy, and Portugal
CHALLENGES
|
SOLUTIONS
|
BENEFITS
|
---|
Sal Vesta has taken control of its business with a view to increasing its competitiveness and strengthening its international presence. To do so, the company has decided to internalise its logistics processes and digitise its facility with Mecalux’s Easy WMS warehouse management system. Prior to this, Sal Vesta had subcontracted its logistics operations to a third-party logistics (3PL) provider, which carried out storage and order picking tasks in the facility. “When outsourcing our logistics activities, the 3PL operators could only manage the products in the warehouse. Even if there was downtime, they weren’t authorised to help their co-workers on the production lines,” says Sal Vesta Plant Manager Guillem Gutiérrez.
To overcome these limitations, Sal Vesta set out to control the entire production and logistics plant to bring down costs and facilitate the flow of goods. “We wanted to enhance synergies between production and logistics, so we decided to take care of all our logistics operations in-house. Now, our warehouse employees spend most of their time managing products. And when necessary, they can lend a hand in production tasks in addition to doing other activities during downtime,” says Gutiérrez.
When Sal Vesta started managing its own logistics operations, it found itself faced with another need: to implement a warehouse management system (WMS). “The 3PL that was in charge of our logistics operations used a management system, but we needed a program that could be tailored to the particular characteristics of our business.
After obtaining information, comparing proposals and asking for references, we decided on Easy WMS from Mecalux,” says Gutiérrez.
Warehouse digitisation
“We were looking for a WMS that could adapt to the specific features of our warehouse. The Mecalux technical team met with us so we could explain in detail exactly what we were looking for in the software,” says Gutiérrez.
After analysing Sal Vesta’s needs and operations, Mecalux designed a software program capable of boosting the company’s supply chain. “One strength of Easy WMS is its robustness and ability to eliminate errors,” says Gutiérrez.
Easy WMS’s usability was a decisive question for Sal Vesta: “The software is extremely intuitive and allows us to easily find all the information we need.” When a new operator is hired, they don’t require any training: they travel through the warehouse with an RF scanner, which gives them detailed instructions on the tasks they have to carry out,” says Gutiérrez. Via the RF scanners, Easy WMS tells operators which pallet to find or where to slot it, among other processes.
“The software is also really effective for managing inventory,” says Gutiérrez. Easy WMS sends the operators instructions on how to take inventory in the warehouse (by zone, counting specific SKUs, in specific aisles, etc.).
“By managing our products efficiently, we’ve eliminated any potential discrepancies between our physical inventory and the inventory recorded in Easy WMS. Now, we know the actual stock we have in real time.”
“One of the things we value most about Easy WMS is its versatility; this software is future-ready. If we ever want to install a new storage system or incorporate a new operation, everything will continue to be controlled and optimised by this WMS,” says Gutiérrez.
“Another advantage of Easy WMS is the fact that it’s online. Being able to connect from anywhere to a VPN network to check on the status of the warehouse is enormously helpful for managing day-to-day operations.
The power of data
Information analysis is a central pillar in Sal Vesta’s strategy for detecting opportunities for improvement. “Our warehouse generates a huge amount of data, for example, the number of goods received and dispatched, on-time deliveries made and the different product characteristics. We wanted a system capable of analysing and displaying all this information to be able to make changes in processes when necessary,” says Gutiérrez.
To foster data-driven decision-making, the company has implemented the Supply Chain Analytics Software module, an extension of Easy WMS specifically designed to provide useful data on the main activities done in the warehouse. With this solution, logistics managers can effect strategic improvements in the facility to raise productivity based on objective information.
This software incorporates dashboards that include the main functionalities to take into account in the warehouse: goods entries and exits, order picking and storage capacity. “Supply Chain Analytics Software supplies us with all the information we need quickly and in a way that’s visually friendly so that we can make decisions in the shortest possible time,” says Gutiérrez.
Advantages of digital logistics
Sal Vesta, which had been outsourcing its logistics operations to a 3PL, now manages all its warehouse processes internally. By supervising all its business processes, the company can more accurately control its goods and ensure it meets customer order delivery times.
With the help of Easy WMS, Sal Vesta has been able to successfully deal with any complexities and market changes, such as those seen with the coronavirus pandemic. “Luckily, we’ve come through it pretty well. In 2020, our results were practically the same as in 2019,” says Gutiérrez.
The company has promoted information culture, which, in this particular case, means obtaining all possible supply chain data to detect improvement opportunities. With Easy WMS, Sal Vesta has also optimised operations, from goods receipt to order dispatch.
Warehouse operations
Sal Vesta’s warehouse stores a variety of SKUs of finished products that are delivered directly to customers. “We sell three types of salt: tablets, used as a water softener for swimming pools and dishwashers; bulk, for businesses in the electrochemical sector; and food grade, for companies in that industry. We distribute these items in 25 kg sacks or in 1,000 kg big bags,” says Gutiérrez.
Every day, the Sal Vesta facility receives 350 pallets from production that are then stored on the racks in line with the FIFO (first in, first out) method. When the time is right, operators remove these loads from their locations and send them to the dispatch zone. They remain in this area until they are finally picked up and distributed by the delivery lorry. Around 350 pallets are shipped from this facility on a daily basis.
“Our logistics operations consist of three movements: from production to the warehouse, from the warehouse to the dispatch zone, and from there to the delivery lorry. Since there’s no complex picking involved, our operations are very agile,” says Gutiérrez.
We’ve got the warehouse management software we really wanted for our business. Easy WMS has been fully adapted to our logistics needs. This system is highly intuitive; it facilitates the work of the operators and enables easy access to information. We’ve also implemented the Supply Chain Analytics Software module to generate reports and visualise KPIs that help us to make better decisions for our facility.
Ask an expert