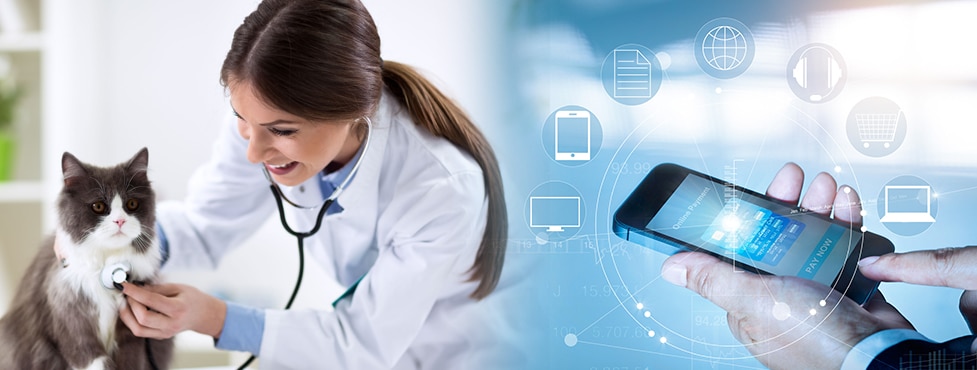
Samaniego upgrades Easy WMS with the Enterprise version
The Enterprise version of Easy WMS has accelerated order prep
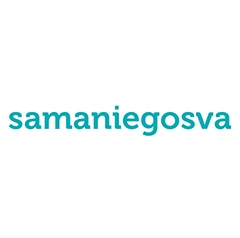
Samaniego, a company specialising in animal health, has revamped the management of its installation in Logroño, Spain. The company has upgraded Easy WMS, the warehouse management system by Mecalux, to the Enterprise version to cope with the rise in sales seen in recent years and enhance the preparation of orders from its online shop. This WMS equips the company with traceability of all its SKUs in stock, which is vital when working with medication.
Evolution and digitisation
Founded in 1988, Samaniego is dedicated to the marketing of products for veterinary clinics and hospitals. The firm works with the major animal health laboratories to provide effective drugs adapted to the needs of every pet.
Samaniego has a 2,000m2 warehouse in Logroño, Spain, where it manages 9,000 extremely varied SKUs, ranging from surgical materials to animal health and food products. It is divided into three areas:
- Ambient temperature zone. This area mainly stores feed and medicine with a high turnover, while biocides are housed in an isolated part.
- Cooled temperature zone (4-15 °C). This section contains medicines that, because of their characteristics, must be kept at a controlled temperature to maintain their properties.
- Vertical warehouse. This is used for small and low-turnover products. Easy WMS has been optimally integrated with this storage system: it not only knows what stock is available, but also organises the work of the operators storing products and preparing orders.
This installation represents the entrepreneurial and evolutionary spirit imbued by Samaniego to a T. From the outset, the company has refashioned itself several times with the aim of adapting to business changes.
Warehouse Manager David García explains that, initially, the goods were managed entirely from memory, without support from any software. “The operators knew, more or less, where each item was located. The warehouse was organised based on the laboratories, so all items from the same lab were placed on the same shelf,” he says.
However, this way of working led to errors, especially as the number of SKUs and orders grew. The firm needed a much more effective system for carrying out storage and order prep tasks.
By implementing the SAP ERP, Samaniego was able to define the locations on the shelves. According to David García, “This was a huge change for us because having an assigned slot for each product served as a guide when preparing orders. But what we really needed was a system that would enhance the work of the operators and enable us to accurately control the goods.”
As the company was looking for software specifically centred on the operational management of the installation, it decided to implement a warehouse management system (WMS). In contrast to an ERP, this software carries out an exhaustive control of all the products and resources of a logistics centre. In addition, it supervises the work done by the operators so as to obtain better results. The WMS manages and optimises all warehouse operations, including goods receipt, location designation, order preparation and dispatch.
After comparing various options, Samaniego chose Easy WMS by Mecalux because, in the words of the Warehouse Manager, “It really inspired confidence in us, in terms of both its features and the support included in the implementation. Not only is it a great WMS — there’s also a lot of good work and maintenance behind it.” To drive this project forward, the company relied on support from the La Rioja Economic Development Agency.
The installation of Easy WMS resulted in improved warehouse organisation. Consequently, Samaniego made its logistics systems more flexible and increased its operational throughput. It now has the ability to offer its customers more satisfactory service.
One of the features of Mecalux’s WMS is its capacity to be integrated with any ERP. In fact, Easy WMS has a standard SAP-certified communication interface that enables easy integration with this ERP; it allows the two systems to exchange data and information essential for managing the warehouse more efficiently.
Why implement a WMS if I already have an ERP?
Every business that wants to carry out efficient, advanced management of its warehouse implements a WMS for the following reasons:
- Degree of specialisation. WMSs are focused on the management of installations and provide much stricter stock control compared to an ERP.
- Inventory management. A WMS uses algorithms to make the most of the available storage capacity.
- Full traceability. The WMS records all processes that each item has gone through across the supply chain.
- Configurable system. Its features can be modified to adapt to market changes and to the particular characteristics of each sector (e-commerce, retail, food, chemicals, etc.).
- Optimised operations. The WMS supervises and improves warehouse operations. It sends clear and precise instructions to workers on how to perform their various tasks more quickly.
- Flexible integration. The warehouse management system integrates with picking support systems (radiofrequency terminals and pick- and put-to-light devices, among others).
Easy WMS and traceability
“Among all of Easy WMS’s advantages, I would highlight, first and foremost, product control and traceability,” says David García. “Traceability is fundamental for our business, since we market drugs. Imagine, for example, that there’s a health alert requiring the recall of a specific batch from the market. If we don’t remove it quickly, the consequences could be devastating,” he points out.
Traceability is a tool that allows Samaniego to identify and strictly monitor the characteristics of the products (from their components to the packaging used) and all the phases they go through before being delivered to customers.
Easy WMS tracks the goods from the moment they enter the installation. Every day, the warehouse receives around 30 pallets containing drugs from various laboratories in Spain, as well as food from Spain, Denmark and the Netherlands. When an operator identifies a product (with the help of radiofrequency terminals), Easy WMS knows all the information linked to that particular item (volume, weight, expiry date, location, turnover, etc.).
Immediately afterwards, Easy WMS assigns the product a location, taking into account its characteristics and demand level. This way, Easy WMS can take inventory in real time, knowing where each item is located at all times.
This efficient goods control has had a positive effect on the other operations in the installation. “With Easy WMS, we not only know where each item is at any moment; we also carry out replenishment much more effectively,” emphasises the Warehouse Manager.
When the established minimum inventory level is reached, Easy WMS communicates this to Samaniego’s SAP ERP so that more drugs are then ordered from suppliers. This ensures that the installation is always stocked with the minimum amount of goods necessary to meet customer needs and avoid stockouts.
David García - Warehouse Manager at Samaniego
“We upgraded Easy WMS to be able to cope with the rise in sales and revamp our order prep strategy. We’ve been working with Easy WMS for years, and we’re more than satisfied with its results. Knowing the exact location of each product and controlling traceability represent huge progress.”
Preparation of online orders
One of the most ambitious changes the company has taken on over the past few years is the start-up of its online shop. Via Samaniego’s web page, veterinary clinics and specialised shops can place their orders and receive products as expeditiously as possible.
This project has been a tremendous success. In the words of David García, “The percentage of online orders is growing quite a lot; approximately 60% of the orders we prepare in the warehouse are placed through the webpage.”
Nevertheless, the company’s move into the online world also required extra effort from its logistics systems, basically because it had to prepare more orders in less time.
Against this backdrop, Samaniego decided to upgrade Easy WMS, moving from the Pro version to Enterprise to adapt to all these changes. “We were convinced that it would help us cope with the increased sales volume,” affirms David García.
Mecalux’s Enterprise version is designed specifically for warehouses with complex operations and that need to customise the features of their WMS, as in the case of Samaniego. With this solution, the software will be able to adapt to future changes made to the installation and accompany the business in its expansion projects.
The new version of Easy WMS had to boost the warehouse’s main operation: picking. “The WMS divides the orders to be prepared separately in the different areas of the installation,” points out the Warehouse Manager. Easy WMS sends the work orders in a synchronised way to the operators working in the various sections of the installation. The operators walk around the zone assigned to them with a cart, picking the SKUs indicated to them by Easy WMS by means of a radiofrequency terminal.
This has resulted in increased speed and safety in order prep. The company has gone from preparing 144 orders a day (with an average of 750 total lines) to 217 orders made up of a total of 1,500 lines in a single work shift.
Once the orders are finished, they are sent directly to the dispatch area. “We work with multiple carriers, and each dock is assigned to a specific transport agency. Easy WMS knows which agency will distribute each order, so it lets the operator know in advance which dock the parcel will be dispatched from,” notes David García.
Trusted logistics
Samaniego is a company with a strong commitment to service. Its top priority is to supply veterinary clinics with drugs and foodstuffs whenever required. To do so, it must be equipped with an advanced logistics system and pay close attention to picking.
The Enterprise version of Easy WMS has made order prep quicker. By following its instructions, operators can concentrate on finishing the greatest number of orders in the shortest time possible. Consequently, the business has increased the number of orders prepared in the warehouse, especially those placed through the website, which currently comprise 60% of total orders.
Advantages for Samaniego
- Jump to e-commerce: the Enterprise version of Easy WMS helps Samaniego to prepare more orders per day placed via its webpage in less time.
- Inventory traceability: Easy WMS accurately monitors the movements of each of the 9,000 SKUs stored in the installation.
- Integration with the ERP: the WMS by Mecalux is integrated with Samaniego’s SAP ERP in order to boost warehouse productivity.
Gallery
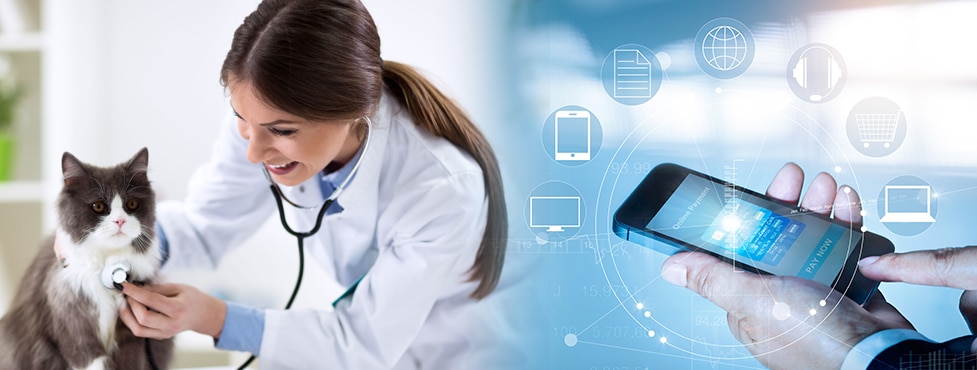
Samaniego has upgraded Easy WMs to the Enterprise version
Ask an expert