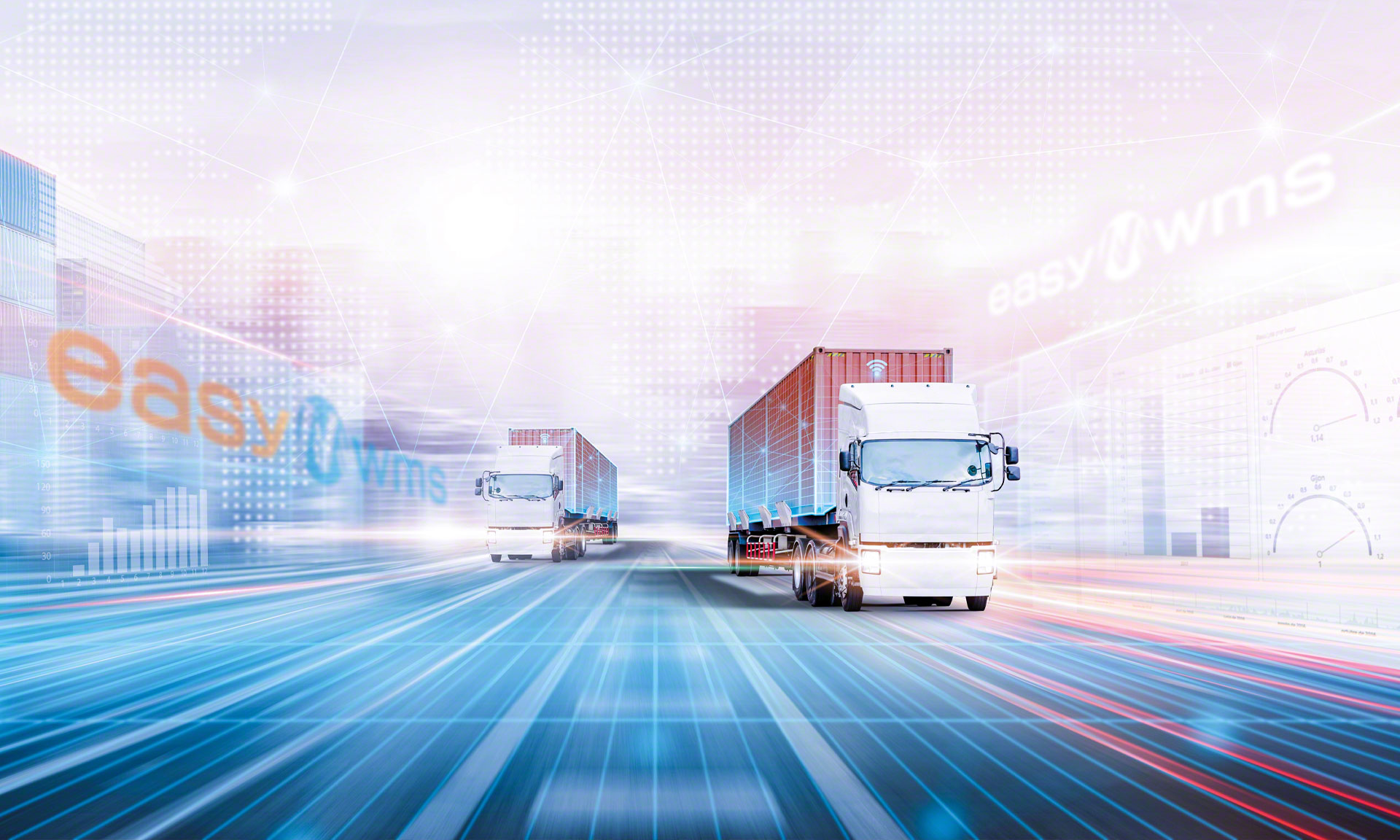
Car-wash product specialist Spare optimises its operations with Easy WMS
Spare, a distributor of products and parts for self-service car washes and industrial cleaning in general, upgrades its warehouse operations with Mecalux’s Easy WMS.
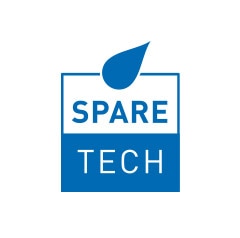
Spare, a distributor of spare parts and high-pressure cleaning equipment, has digitalised its warehouse with Mecalux’s Easy WMS management system. The software organises operations such as goods receipt and order picking to avoid errors in the delivery of products to customers.
Spare: specialist in car wash products
In business since 2003, Spare is a family-run business devoted to the sale of spare parts and high-pressure cleaning equipment. The company’s product portfolio includes over 1,800 items, from turbine-motor vacuum cleaners to reverse osmosis water purification systems and waterproof LED lighting. Spare’s products are used in car wash stations in countries in Europe, the Middle East and Northwest Africa.
- Founded in: 2003
- International presence: France, Europe, the Middle East and Northwest Africa
CHALLENGES
|
SOLUTIONS
|
BENEFITS
|
---|
“In the last five years, Spare has grown significantly, through market expansion at the international level. As a result, logistics has become one of the central pillars of our business,” says Thierry Darves-Bornoz, General Manager of Spare.
Located in Ivry-sur-Seine (France), Spare’s warehouse has a surface area of just 650 m². However, the space is equipped with three storage systems and houses 1,600 SKUs of different sizes and turnovers. “With such a high level of inventory, our priority is to maintain strict control of stock, avoiding errors in product management and order fulfilment,” says Darves-Bornoz.
In the past, Spare had used a warehouse management system (WMS) to monitor all its goods. Over time, though, it became unable to keep up with the increasing pace of work and rising order volumes. At that point, the company came to the conclusion that it needed a more advanced solution. “We wanted a system that would adapt to the particular characteristics of our logistics processes and help us drive such demanding operations as order picking,” says Darves-Bornoz.
After comparing several options, Spare opted for Mecalux’s Easy WMS warehouse management software. “Mecalux has extensive experience in developing logistics solutions. Its WMS includes functionalities to track stock in real time and offer customers a high level of service. Without a doubt, it was the best option for us,” says Darves-Bornoz.
Easy WMS intervenes in all of Spare’s warehouse processes, from the receipt of the goods until their distribution to self-service car washes. “The installation of Easy WMS was a game-changer for our organisation. Our team learnt how to use it very quickly and was eager to find out about its advantages right from the start,” says Darves-Bornoz.
Optimised operations
In addition to transforming and enhancing Spare’s logistics operations, digitalisation has had a positive effect on the company’s other processes. “Since we installed Easy WMS, all our departments are coordinated and are working more rigorously,” says Darves-Bornoz.
Coordination between Spare’s various departments is essential for providing good service. To ensure smooth two-way communication with the warehouse, Easy WMS has been integrated with Spare’s Sage 100 ERP system. Two of the company’s priorities are for its logistics facility to always have the materials it needs to fill orders and for customers’ products to be distributed without delay. As the two programs interface, when a customer places an order, the ERP system notifies Easy WMS to immediately organise the picking and shipping processes.
To facilitate operations, all of Spare’s goods are properly identified and strategically arranged in the facility. “Identifying the locations with a code has brought us a major advantage: we’ve saved space,” says Darves-Bornoz.
Every day, when the products arrive at the warehouse, operators read their barcodes with RF scanners and Easy WMS assigns them a position. The system incorporates rules and algorithms that consider variables such as SKU type and turnover to decide where to store each product. An optimal put away strategy cuts down on operator travel in the facility when locating the different SKUs.
“Order picking is one of the operations that has benefited the most from installing Easy WMS: operators are much faster. We’ve reduced our order fulfilment times, so now, we can deliver goods to customers with much shorter lead times,” says Darves-Bornoz. The Mecalux software tells operators which location to go to and which items to pick to put together orders. The system generates pick paths to ensure that the operators travel the shortest possible distances and can complete orders more quickly. “By following Easy WMS’s instructions step by step, we’ve minimised errors in picking,” says Darves-Bornoz.
Shipshape shipping
Order shipment and delivery are two operations that directly impact customer satisfaction. “When we contacted Mecalux, we were looking for a digital solution that would eliminate order distribution errors and generate labels for delivery agencies automatically,” says Darves-Bornoz.
Thus, Mecalux implemented Multi Carrier Shipping Software, a digital solution for performing goods packing, labelling and transport operations accurately, speedily and without errors. The software manages two differentiated processes simultaneously:
- Order packing and labelling. The system shows operators which items to pack and whether to do this as a single unit load or multiple ones. Easy WMS systematically creates and prints a label for each parcel. “It was crucial for us to avoid errors in the labelling process,” says Darves-Bornoz.
- Synchronisation between the warehouse and carriers. Multi Carrier Shipping Software automates communication with delivery agencies. The Spare facility can forward the shipping agent all the required information, such as the number of parcels to be distributed and their size. “This software has made our operators’ work much easier. And most significantly, it’s streamlined shipping.”
With Multi Carrier Shipping Software, deliveries are faster and more efficient, minimising cost overruns. The family business has achieved seamless communication between its warehouse and the delivery agencies, ensuring optimal information management.
Advantages of digital logistics
Spare has digitalised its logistics operations with a sophisticated solution capable of adapting to business changes, such as a rise in the number of daily orders. The system has raised warehouse productivity by making operations much smoother and more accurate. Easy WMS has helped the company become more competitive and bolstered its growth.
Spare has optimised its warehouse operations and can now fulfil its customers’ needs with the utmost efficiency. “We’ve achieved the three priorities we set when digitalising our logistics operations: to track processes, save time and eliminate errors,” says Darves-Bornoz. The company’s supply chain has taken a huge leap forward.
Installing Easy WMS has been a very gratifying decision for our business. It would be impossible to work without this software. The system has brought us considerable advantages, from lowering operation execution times to minimising order delivery errors.
Ask an expert