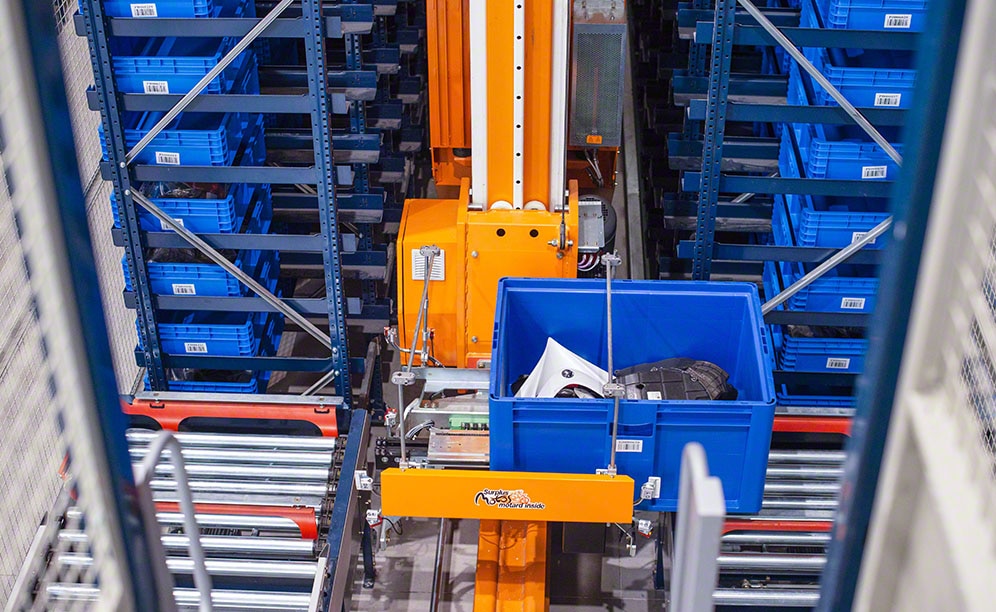
Surplus Motos: automation drives growth
Surplus Motos' new centre has space for 300,000 parts and can recycle up to 10,000 motorcycles a year
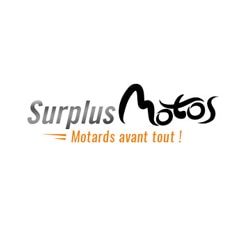
Surplus Motos, a company that sells spare parts for used motorcycles, has set out to optimise its logistics systems and improve its order preparation and inventory management. To do so, it has opened a new 11,500 m2 logistics centre in Gaillac, France. Mecalux has equipped it with an automated warehouse for boxes managed by Easy WMS, in addition to pallet racks and picking shelves. In total, the facility has space for 300,000 parts and can recycle up to 10,000 motorbikes per year.
Recycling and transformation
Headquartered in Gaillac, in southern France, Surplus Motos has been in the business of recycling and marketing motorcycle parts since 2010. After being cleaned, these components can be used as if they were brand new; more importantly, their selling price is 30%-70% more economical.
Thanks to Surplus Motos, customers not only save on the cost of their motorbike, but can also reduce their environmental footprint. By purchasing second-hand parts and promoting recycling, there is no need to manufacture new pieces.
Committed to sustainable development, Surplus Motos has opened a new 11,500 m2 logistics centre that has enabled it to transition into Industry 4.0 and enhance both the working area and storage capacity. With this expansion, the firm has space for 300,000 parts. Moreover, it can recycle up to 10,000 motorcycles a year, five times more than before.
At this plant, the company decontaminates, disassembles and cleans the motorbike components. After assessing and certifying their performance, the parts are photographed in the studio, stored and put on sale.
It was necessary to streamline order preparation in the warehouse, and, to do this, all SKUs had to be properly organised. Therefore, the installation was divided into three sections with different storage systems:
- An automated warehouse for boxes managed by Easy WMS.
- Four narrow aisles with picking shelves on both sides.
- One aisle with pallet racking.
By combining three storage systems in a single space, the firm can distribute goods based on their characteristics and rotation. Thus, for example, small and high-turnover items are deposited in the automated installation for boxes, due to its agile inbound and outbound flows. Meanwhile, larger items (tyres, engines and chassis) are stored on the pallet racks.
All operations in the automated installation for boxes are supervised by Easy WMS, Mecalux’s warehouse management system. This software has a dual role: to update the inventory in real time and guide operators in picking tasks.
Automated warehouse for boxes devoted to picking
This is composed of two 70-metre-long aisles with racking measuring 9.6 m high on both sides. It provides storage for 11,904 boxes overall with a maximum unit weight of 50 kg. In each aisle, a stacker crane inserts and removes boxes from their locations in automatic mode.
Bulkier boxes (600 x 800 x 425 mm) are deposited on the upper levels of the racking, while smaller boxes (400 x 600 x 170 mm) are placed on the lower levels. As these items are smaller, two boxes can be placed in a single location (one behind the other), thereby allowing storage of more products.
The company was adamant that this installation had to be automated in order to meet two objectives: improvement of operator picking conditions and optimization of the time and space dedicated to storage. It should be noted that 11,904 boxes can be automatically stored in little more than 360 m2.
The warehouse was specifically designed to facilitate and streamline order prep tasks, due to the throughput of the stacker cranes — which can perform 96 combined cycles per hour — and to the two pick stations. At these posts, set up on one side of the racks, operators wait to receive the goods automatically. Then, they extract the products indicated by Easy WMS on a screen and insert them in the corresponding orders, located behind them.
By following instructions from Easy WMS, the possibility of error is drastically lowered. This system accurately shows operators the number of items that need to be extracted from each box and where to deposit them, thus, improving efficiency.
The pick stations also serve as replenishment posts during off-peak hours, that is, when there is less picking work. This prevents interference in either operation.
Pallet racks and shelves for boxes
Next to the automated installation, pallet racks and picking shelves with narrow aisles (1.5 m wide) have been set up.
These racks and shelves were chosen for their versatility, as they can be adapted to boxes and pallets of various sizes.In addition, they offer direct access to the products. This provides considerable flexibility when it comes to goods management and optimal stock control, as each location is designed to hold a SKU.
Operators use wire-guided forklifts to move within the narrow aisles, carrying out storage and picking tasks with ease. To make this possible, a wire has been embedded into the floor, producing a magnetic field that the machine detects and uses as a guide. This system is highly practical, as it prevents impacts to the racking structure, ensuring that the goods are fully protected.
Revamped logistics
Surplus Motos is a company with a passion for motorbikes and a commitment to sustainable development. Its growth has been based on improving processes and leveraging available resources to provide better customer service.
The transformation of its logistics systems has been geared in that vein. The racking spans just about the entire height of the building to provide greater storage capacity, and the firm chose automation to maximise operation productivity, particularly in picking activities.
Having a large, flexible installation has given Surplus Motos wings, not only because it accommodates a huge number of parts, but also because it can cope with the preparation of an increasing number of orders. Ultimately, efficient logistics became the ideal solution for further growth.
Advantages for Surplus Motos
- Agile picking: the warehouse is designed to streamline the preparation of 200 orders per day.
- Larger storage capacity: with this new installation, the company has space for 300,000 parts and can recycle up to 10,000 motorbikes a year.
- Warehouse organisation: all the goods are optimally distributed throughout the installation, taking into account product type, dimensions and demand level. This makes it easier to locate each item at the time a customer requests it.
Automated warehouse for boxes | |
---|---|
Storage capacity: | 11,904 boxes |
Max. box weigh: | 50 kg |
Racking height: | 9.6 m |
Racking length: | 70 m |
Gallery
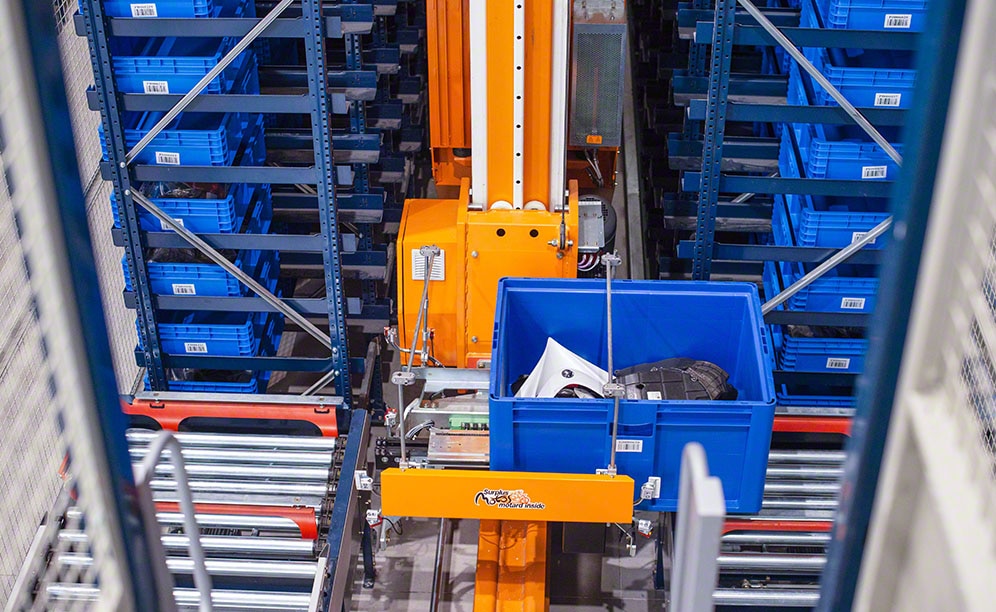
The new Surplus Motos centre is equipped with an automated warehouse for boxes
Ask an expert