
TB Group optimises its warehouse for protective gloves, safety shoes and workwear
TB Group, a manufacturer of PPE, monitors the status of 8,100 SKUs in real time.
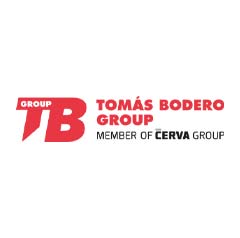
TB Group, a manufacturer of PPE, has digitalised its warehouse in Burgos, Spain, with Mecalux’s Easy WMS software. The company has fine-tuned operations and can monitor its processes more rigorously to make strategic improvement decisions.
TB Group: protective gloves, safety shoes and workwear
Based in Burgos (Spain), TB Group is a company dedicated to the design, manufacture and sale of personal protective equipment (PPE). The business started out making protective gloves. Over time, it expanded its expertise to include the production and marketing of protective solutions, such as safety footwear, for all types of professionals in the industrial sector. TB Group maintains partnerships with internationally renowned brands to develop a wide range of workwear and introduce new models that address customers’ most demanding needs. Founded in 1973, the company is present in over 30 countries worldwide.
CHALLENGES
|
SOLUTIONS
|
BENEFITS
|
---|
The year 2023 marks TB Group’s 50th anniversary in the service of occupational safety and protection. This specialist in mechanical protection gloves, safety shoes and workwear is characterised by its commitment to business transformation and modernisation with the aim of attracting new customers. “From the start, our mission has been to develop solutions that allow industrial sector professionals to face day-to-day risks with the utmost safety,” says Carlos García, Logistics & Warehouse Manager at TB Group.
The supply chain comprises a series of processes that are essential for TB Group to provide efficient service. “We had to overhaul our logistics operations to adapt to business changes. We also wanted real-time assurance that our products were being properly distributed and delivered,” says García.
One of TB Group’s most recent endeavours is the digitisation of its logistics processes. The company recently equipped its 5,600 m² distribution centre (DC) with Mecalux’s Easy WMS warehouse management software to improve all operations. “In the beginning, we were able to control all our receiving, storage, turnover and shipping processes using our ERP system. But as they increased in both volume and complexity, we realised we needed a WMS: a specific, more sophisticated and efficient tool to comprehensively manage processes in our facility,” says García.
Warehouse optimisation
“We decided to incorporate WMS software to enhance operations in our centre and maximise efficiency in inventory control. After weighing several options, we chose Mecalux’s Easy WMS because we felt it was the best software for us. That is, it includes advanced functionalities that would respond to our operational needs,” says García.
When digitalising its facility, one of TB Group’s priorities was to improve stock management. The company’s DC houses more than 8,100 SKUs of different sizes and turnovers. “Organising such diverse PPE and maintaining real-time inventory control is crucial to streamline operations and prevent errors,” says García. Arranging all products strategically results in much smoother processes, boosting efficiency in storage and order picking operations, among others.
The software identifies and tracks all goods, from their arrival at the facility through to their shipment. Operators simply read the barcode on each pallet received with their RF scanners and Easy WMS records the merchandise in the database.
Then, the software assigns each item a position considering variables such as turnover and demand level. “SKUs are managed following the FIFO method: the first in are the first out. With Easy WMS, we make sure we’re organising the goods correctly and without errors,” says García.
With all products recorded and identified in the database, the Mecalux software controls their traceability in real time, determining the exact location of each pallet at any given moment.
Another need TB Group had when digitising its warehouse was to scale up order picking and shipping. Every day, the logistics centre processes and distributes 200 orders sent to customers in many countries, primarily Spain, Portugal, France, Italy, Czechia, Croatia, the UK, Finland and across Latin America.
To prepare each order, Easy WMS generates tasks that are issued to users based on their profiles, authorisation and access levels and location. The system shows them which position to go to and which items to retrieve to complete each order. The software designs pick paths to allow users to travel the shortest possible distances through the facility and can put together orders as efficiently as possible.
“We needed a WMS flexible enough to adjust processes to our customers’ requirements and changes in the DC, such as increases in order, SKU, inventory and demand volumes,” says García. Using the same resources, the system arranges picking tasks to ensure that goods are delivered to customers within the committed time frame.
Digitalised shipping process
Order shipping and delivery are key for TB Group, as these operations directly affect customer satisfaction. “Service level is a priority and non-negotiable for our company, so delivering orders on time and in line with quality standards is a core and distinguishing factor. We also strive to do this at no additional cost,” says García. “We wanted to digitalise the shipping process to facilitate two-way communication with carriers to guarantee delivery according to the terms of sale,” he adds.
TB Group has implemented Multi Carrier Shipping Software, which automates communication between the warehouse and transport agencies. The program organises order packing, labelling and shipping to ensure top-quality service for customers.
Multi Carrier Shipping Software forwards carriers all required delivery information, e.g., the number of parcels to be distributed, their volume and their weight. The delivery agency confirms the operation and sends the necessary data to generate and print the labels and tracking number.
“Our aim is to send information to carriers in a way that’s agile, speedy and automatic. And Multi Carrier Shipping Software offered us that possibility. By no longer transmitting communications and creating delivery notes manually, we’ve leveraged all resources adeptly and shipments are successful,” says García.
Information management and decision-making
“We’ve set out to become a data-driven company. We want to work in a digitalised environment where data helps us organise resources ideally, fine-tune operations and bolster our competitiveness,” says García.
TB Group has installed Supply Chain Analytics Software, an extension of Easy WMS, to segment and structure the vast amount of data generated daily in the facility. “This software enables us to access all the information swiftly and make strategic decisions through KPIs,” says García.
Supply Chain Analytics Software consists of advanced dashboards and graphics with information collected on the various logistics operations performed. The key performance indicators (KPIs) encompass the majority of functionalities to be taken into account in TB Group’s logistics set-up, from receiving and shipping productivity through to picking accuracy.
“We want to be empowered to manage all information on how operations are being executed. Supply Chain Analytics Software’s dashboards provide us with an overview of our processes at a glance. With these data, we can delve deeper into analysing aspects like storage capacity, product turnover and days sales of inventory. Our goal is to make strategic decisions that strengthen our supply chain,” says García.
The program continuously monitors the business. Consequently, TB Group is equipped with real-time knowledge of the state of the warehouse and can make informed decisions, implementing strategic improvements to ramp up productivity.
Logistics in expansion mode
In the face of an ever-evolving supply chain, the most effective approach to optimising operations is to embrace digitalisation. Easy WMS is a scalable software program capable of adapting to changes in TB Group’s DC, such as rising sales and daily orders.
“Our business is currently going through a major transition. Right now, our focus is on developing new product lines, enhancing those already in the market and launching a more modern website to streamline the shopping experience for our customers. All of this will have an impact on TB Group’s logistics processes,” says García.
With Easy WMS, the company will be able to continue serving customers and efficiently manage merchandise movements in the warehouse. Additionally, TB Group will be armed with objective data, which will aid it in fine-tuning operations and adjusting them to meet new business needs.
Easy WMS is a powerful, flexible software program that’s enabled us to organise, analyse and optimise all processes in our centre. Having direct access to all information on everything happening in the warehouse is ideal for decision-making. It allows us to tailor operations to the company’s new requirements.
Ask an expert