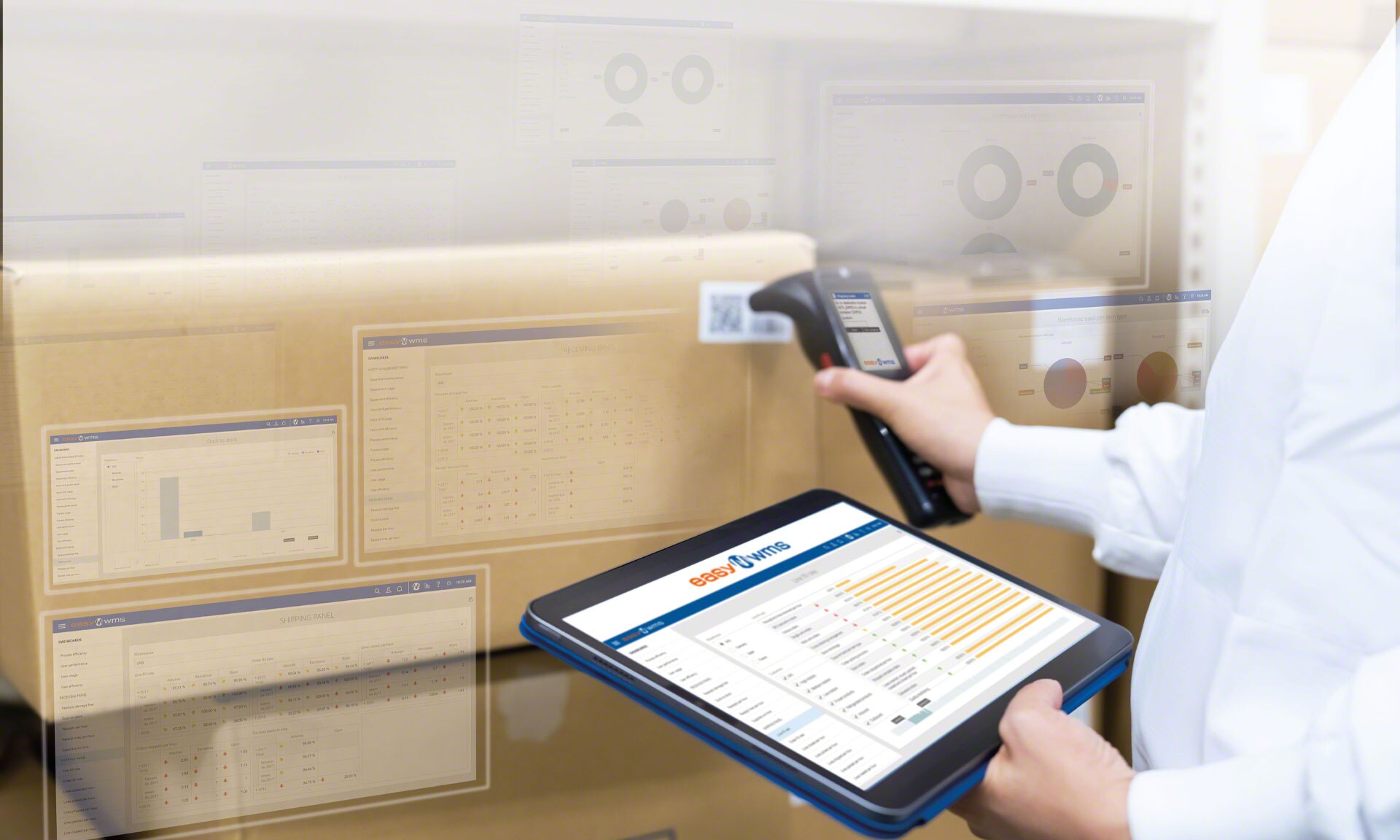
Two digital warehouses for DIY company Unipro Group
Unipro Group digitalises its two facilities in France with Mecalux’s Easy WMS warehouse management software.
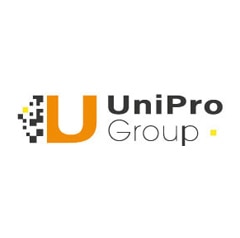
Unipro Group, a retailer of DIY products and solutions for electricians, has digitalised its two warehouses with Mecalux’s Easy WMS software. With this program, the company has an efficient B2B and B2C strategy, meeting its customers’ needs quickly and without errors.
Unipro Group: more than 20 years of experience
Unipro Group is a French company with two subdivisions: Bricolage Direct, specialising in DIY solutions for professionals and private individuals and IICSEN, dedicated to solutions for electricians. The company, operating in the online market, designs and distributes its own brands, which meet quality standards and the needs and expectations of customers.
- Founded in: 1994
- No. of employees: 50+
- International presence: France, Belgium and Italy
CHALLENGES
|
SOLUTIONS
|
BENEFITS
|
---|
Logistics constitutes a major priority for Unipro Group. The company sells DIY products to businesses (B2B) and directly to end customers (B2C). Operating simultaneously with B2B and B2C business models requires extremely strict product control as well as optimised logistics processes to ensure that orders are filled and distributed correctly.
To meet customers’ changing needs, Unipro Group has turned to the latest technological advances. The company has implemented Mecalux’s Easy WMS warehouse management software to foster excellence in its two facilities in France.
Unipro Group has two warehouses in the towns of Yssingeaux and Monistrol-sur-Loire, respectively. Each has a surface area of almost 20,000 m². The facilities house more than 10,000 SKUs of different sizes, characteristics and turnover. They also fill up to 400 daily orders, which are distributed to customers throughout Europe (mainly in France, Belgium and Italy).
“We decided to digitalise our logistics operations in order to perform goods receipt, storage and order picking quickly and without mistakes. We had been using another logistics program, but to cope with the increased activity of our business, we needed a more advanced system that could be deployed in the SaaS model,” says Julien Exbrayat, Unipro Group’s Logistics Manager.
SaaS — i.e., software as a service — is the cloud version of Easy WMS. It enables operators in the two facilities to access the functionalities of the system from any web browser or device with an internet connection.
One of the advantages of Easy WMS in the cloud is its multi-location management capacity: Unipro Group can control operations in both warehouses simultaneously and in real time. The software is designed to adjust to the company’s future needs, overseeing any new facilities the business may open using the same program.
“One of our requirements when implementing the Mecalux solution was that it had to integrate with our ERP system,” says Exbrayat. Easy WMS communicates constantly and bidirectionally with Unipro Group’s Microsoft Business Central ERP software. The two systems transfer data and information to increase productivity.
Two optimised warehouses
Easy WMS controls and coordinates all operations taking place in Unipro Group’s two facilities. “The Mecalux software is very intuitive. Our operators have adapted to the system easily, using RF scanners to carry out practically all their tasks,” says Exbrayat. By following the instructions step by step, these workers are much more accurate and can do their work faster and without errors. Every day, the two warehouses receive a multitude of pallets with products primarily from China. Operators read the barcodes with their RF scanners to enter the information in the Easy WMS database. This way, the software verifies with the ERP system that the anticipated items have been received.
By identifying all items the minute they arrive at the facilities, Unipro Group can monitor all movements of goods and control traceability in real time. When replenishing products, Easy WMS organises stock exchanges between the two buildings, preventing mistakes and incomplete shipments.
In addition to perpetual inventory control, the Mecalux software performs stock counts in both warehouses. In this operation, workers conduct a physical inventory of the stock to determine the available products and validate that they are in proper condition. The software tells the operators which locations to go to and which items to count.
More than 2,200 lines a day
Order picking is one of the most demanding processes in Unipro Group’s facilities, which fill up to 400 orders containing over 2,200 lines every day.
The company reorganised its picking tasks to streamline the distribution of its merchandise. “We group the orders to be prepared by criteria such as customer, number of lines in each order and designated carrier. Properly organising this operation using the Mecalux software has boosted our productivity,” says Exbrayat.
Via the RF scanners, each operator receives a detailed list of the orders they must prepare. Easy WMS shows them which aisle to go to, which slot to locate and how many items to remove. The operators scan the barcode on each product for the program to verify that they have picked the right merchandise.
Orders containing many products are typically prepared individually, one by one. In these cases, operators remove the items from the racks and move them directly to the consolidation and shipping area to be distributed to customers.
Most orders are picked in batches. Operators fill several orders on a single run through the warehouse: they remove the products from the racks, place them in a cart and then take them to the consolidation zone, where they are sorted and separated by order.
In Unipro Group’s facilities, operators also typically work by zone, which is an ideal working method when preparing a large volume of diverse orders. The warehouses are divided into storage areas according to different criteria: product type, demand level, storage conditions and quantity of SKUs, for instance. A certain number of operators is assigned to each zone and they pick merchandise located in their area.
B2B and B2C shipments
Every day, the two Unipro Group facilities dispatch 60 pallets and 200 boxes to customers in France, Belgium, Italy and other countries.
“B2B flows are different from B2C: the agencies that distribute B2B orders aren’t the same as those that deliver B2C parcels. It was essential for us to organise order deliveries and avoid errors,” says Exbrayat. The Multi Carrier Shipping Software module — an extension of Easy WMS — organises all shipments.
Once picking is finished, the software sends instructions to operators on how to package the items. For example, it tells them whether to place the goods in one or more packages and generates a label for each order. “Labelling is vital for us. Digitally managing this process saves time and eliminates mistakes when distributing goods,” says Exbrayat. The module knows which agency will deliver the merchandise and prints a personalised label for each parcel. It includes the customer tracking number, among other parameters.
Multi Carrier Shipping Software generates all the necessary documentation for the delivery agencies (namely DPDgroup, Colissimo and Kuehne+Nagel). Thus, when the carriers arrive at the warehouses, they only need to pick up the parcels and continue with their delivery routes.
Digitalised omnichannel logistics
Unipro Group has chosen to digitally transform its supply chain to establish an effective omnichannel strategy and offer error-free B2B and B2C service.
“For us, the digital coordination of the two facilities is crucial for ensuring that our business runs smoothly. Our top priorities are to keep our products in optimal conditions and avoid stockouts that could delay order distribution,” says Exbrayat.
With Easy WMS in the cloud, Unipro Group is equipped with flexible, scalable software capable of adapting to business changes and future growth.
Advantages of Easy WMS in the cloud
- Accessibility: the company can access Easy WMS from any computer or device with an internet connection to consult the status of its warehouse operations.
- Lower initial investment: not requiring its own servers substantially reduces the business’s initial outlay.
- Flexibility: the number of users can be increased to accommodate operations with high seasonality.
- Multi-location management: companies with multiple warehouses can sync inventory between their facilities and control processes comprehensively.
- Automatic updates: with the software in the cloud, the business always has the latest version of Easy WMS.
We’re extremely satisfied with Easy WMS and would recommend it to other companies. The Mecalux software fully adapts to our omnichannel logistics operations. The system has helped us optimise processes such as order picking in our two warehouses. Now, we can devote our time to providing our customers with better service.
Ask an expert