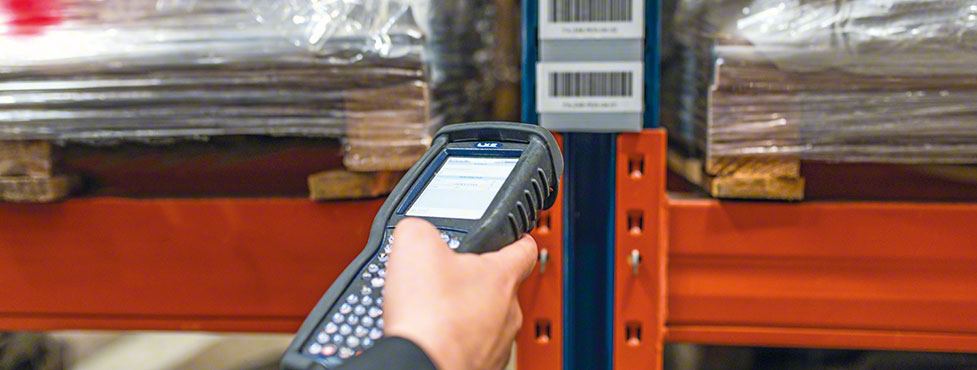
Cimasa gains full traceability and a 25% increase in productivity
The firm devoted to feed, biomass, salt, sugar and substrates has modernised its warehouse with Mecalux's Easy WMS
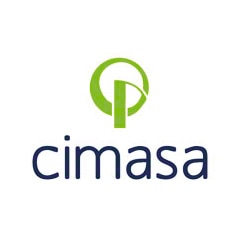
Cimasa, a distributor of animal feed, raw feed materials, biomass, salt, sugar and substrates, has renovated its logistics systems with the aim of boosting its growth. To do this, the firm has opted to install Easy WMS, Mecalux’s warehouse management system, which manages the installation more efficiently and optimises the work of the operators. This system provides traceability and extremely accurate control of all the products, including details such as expiry date, batch number, exact location in real time, monitoring of the different processes, and so on. As a result, the company’s productivity has climbed by 25%.
From feed to biomass and beyond
Cimasa is a business founded in 1963 in the town of La Roda in Albacete, Spain. Its history is characterised by transformation and continuous improvement. Initially, Cimasa produced feed and sold cereal for animals. Over the years, however, it has expanded its product range. It now markets salt, biomass, sugar, substrates and additives that are used in multiple sectors: the hospitality, food, livestock and renewable energy industries, among others.
The company has 20,000 m2 of surface area dedicated to the storage of goods to be subsequently sold. Recently, it has revamped and upgraded its logistics systems to ensure that products are delivered to customers in the best conditions and that they meet safety and hygiene standards. To successfully take on this project, Cimasa got in touch with Mecalux because, in the words of company Manager Francisco Collado, “The staff really inspired confidence in us, apart from the fact that it’s one of the most renowned firms in the logistics sector.”
Pallet racks: speed and versatility
After analysing the particular features of the warehouse in depth, Mecalux installed 9-metre-high pallet racks that can store a total of 2,500 pallets. The racks stand out for their versatility and adaptability to any type of load, weight and volume, enabling Cimasa to easily manage 225 highly varied SKUs.
Likewise, the racks provide direct access to the pallets, facilitating and streamlining storage and order prep tasks. Daily warehouse operations consist of receiving and storing multiple pallets from various manufacturers. Orders are then prepared and sent to customers throughout Spain.
According to Francisco Collado, what the business really needed was to optimise its entire supply chain as well as its product management. He explains, “We wanted to ensure total goods traceability, avoid stockouts and send orders to our customers in record time.”
Cimasa considered the transformation of its installation as an investment in the future. In this vein, the company Manager acknowledges, “We wanted the warehouse to be prepared to face our growth prospects and, in the next few years, help us to prepare more orders using the same resources.”
Obtaining full traceability
Previously, Cimasa used an in-house developed ERP to organise all its business resources, including logistics. The system encompassed several basic features for installations, such as the ability to monitor goods receipt and dispatches.
Nevertheless, the ERP was not specifically designed to manage logistics processes, as it did not include detailed data on locations or warehouse operations.
The company knew it needed a warehouse management system (WMS) to carry out much stricter merchandise monitoring compared to what an ERP could offer. A WMS is specifically centred on warehouse management, as it organises and optimises goods movements and goes a step further in inventory control.
Cimasa chose Easy WMS, the WMS by Mecalux, because it is a system that can be adjusted to the particular characteristics of its business. It can supervise all operations performed in the installation (goods receipt, identification and validation, storage, order prep and dispatch) taking into account the company’s requirements.
Additionally, the WMS by Mecalux has been easily integrated with the company’s ERP. “The two systems are interlinked and transfer data to achieve greater throughput. With Easy WMS, productivity has risen by 25%,” says Cimasa’s Manager.
Easy WMS carries out complete traceability of the goods, identifying their source and the various phases through which they go along the entire supply chain. When a product is received, the WMS collects its data and assigns it a location based on its characteristics, batch and best-before date.
Advantages of Easy WMS versus an ERP logistics module
- Level of specialisation. The most notable difference between an ERP and a WMS lies in the degree of specialisation of warehouse management systems; WMS management is much more exhaustive and detailed.
- Specific features. Easy WMS has modules that add special functions to the WMS to address increasingly complex processes and scenarios.
- Flexible integration. The WMS by Mecalux integrates with any type of software, whether an ERP or voice-picking and PTL devices.
- Deployment variety. Easy WMS has two architecture options that can be adjusted to the needs of any company (SaaS and on-premise).
- Customisable system. Easy WMS is more flexible than ERPs in order to adapt to the installation's various operations and obtain greater profitability.
Preparing multi-SKU orders
Every day, dozens of orders are prepared for delivery to Cimasa’s customers. Orders can be made up of full single-SKU pallets or of various multi-SKU units.
Easy WMS is programmed to optimise the picking routes, designing them to ensure that operators travel the minimum possible distances in the warehouse. Moreover, these routes need to take into consideration the dimensions of the goods; thus, workers first pick voluminous items and, then, smaller products.
Once the orders have been completed, they are strapped together and sent to the loading docks, where they wait to be picked up for shipping by the distribution lorry. Although they are finished, the orders remain open up until a few minutes before being dispatched. This means that, if customers request more items, they can be included in the order.
In addition, there are orders that are prepared via cross-docking, that is, with products that have not been stored. Upon receiving and identifying the SKUs, Easy WMS orders this merchandise to be sent directly to the dispatch area. These items form part of incomplete orders or have been requested by customers and need to be dispatched imminently.
A WMS for boosting growth
The Cimasa warehouse is specifically designed to meet customers’ needs without delay. All organisation of goods and tasks is geared towards the same goal: to provide the best possible service.
Warehouse management software is a tool that efficiently supervises an installation’s operations and available resources. In the case of Cimasa, Easy WMS has become the perfect partner for obtaining maximum supply chain competitiveness and improving productivity by 25%. The particular quality that best describes this warehouse is traceability. The WMS knows all the details about the products: their dimensions, batch, weight, characteristics, production and expiry date, inspection controls passed, and so forth. Likewise, it can rigorously monitor all the SKUs throughout the various supply chain processes.
Easy WMS is also set to grow and accompany Cimasa in its expansion plans. This software arranges the work of the operators and can take on increased numbers of orders.
Francisco Collado - Manager at Cimasa
“Our warehouse is must more efficient with Easy WMS, and the traceability is flawless. By controlling the products with such precision, we can rest assured that all processes and checks are being carried out correctly.”
Advantages for cimasa
- Total traceability: the 225 SKUs that make up Cimasa’s catalogue are identified from the moment they arrive at the installation. The WMS controls all the data: weight, characteristics, volume, expiry date, etc.
- Productivity increased by 25%: Easy WMS’s supervision has contributed toward streamlining warehouse operations (goods receipt, order prep and dispatches) and eliminating any possibility of error.
- WMS integrated with the ERP: Cimasa has achieved more accurate management of its installation with the help of Easy WMS. This WMS is integrated with the ERP, working in sync to ensure a much more agile supply chain.
Gallery
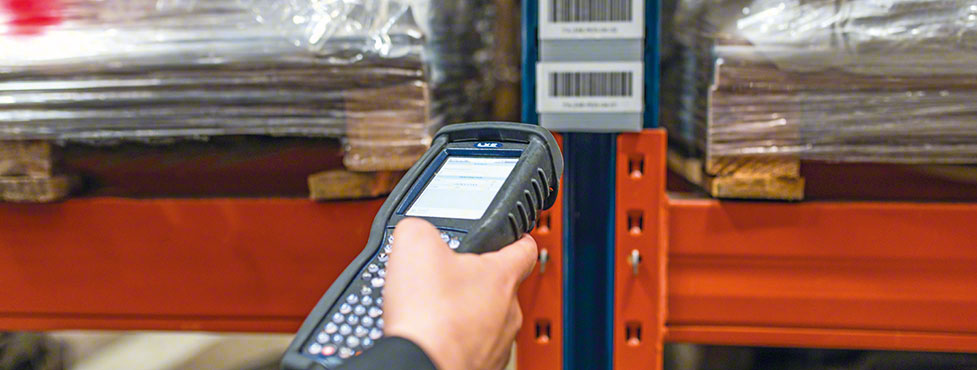
Radiofrequency terminals help to identify Cimasa's goods
Ask an expert