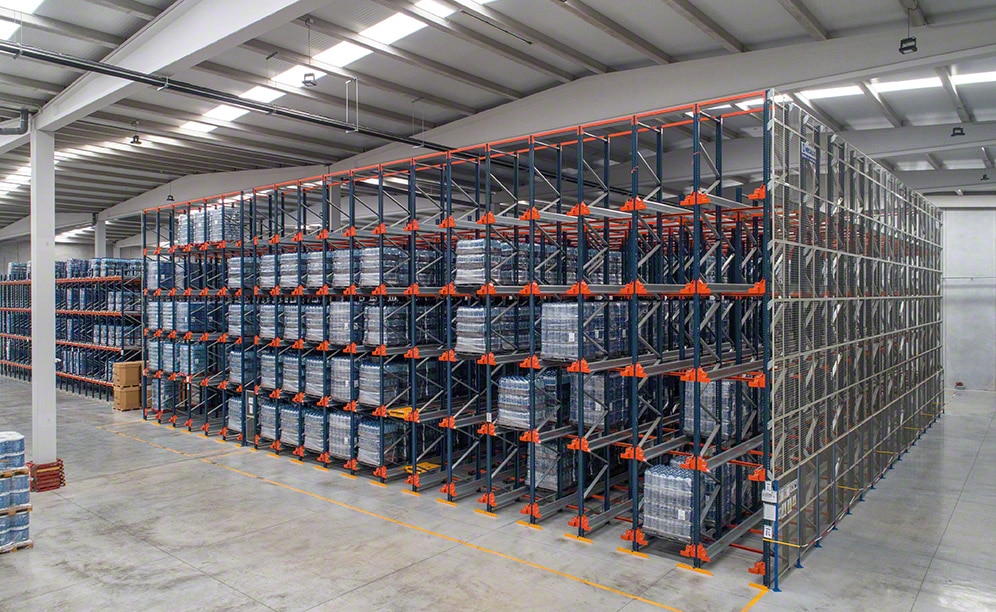
Manantiales del Portell increases the capacity of its water bottling plant
Racks with the Pallet Shuttle system and live rack in the water bottling plant of Manantiales del Portell
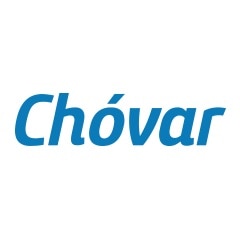
Mecalux has installed the high-density Pallet Shuttle system and live racking in the water bottling plant of Manantiales del Portell, a company who focuses on collecting and bottling water under the brand Aguade Chóvar. The two warehouseing solutions represent a storage capacity that exceeds 4,600 pallets.
About Manantiales del Portell
Manantiales del Portell is a Spanish company that specialised in the intake and bottling of water streaming from water sources in the Sierra Espadan Natural Park. In its bottling plant in Chóvar (Castellón, Spain), it procures, filters and bottles Agua de Chóvar water, an exceptionally pure beverage with a perfect balance of natural minerals and trace elements.
Compact racking: the first choice
Looking to optimise the available area in this bottle water plant fully, Mecalux has installed two compact blocks of racks: one with the Pallet Shuttle system and the other with live racks.
The high-density systems fit the goods Manantiales del Portell sells like a glove, since it deals with homogeneous products –guaranteeing pristine rotation and making sure many pallets are available per SKU. By working with a perishable item, as is the case with bottled water, it is essential that the installed solution could respond to the demands of the FIFO workflows (first in, first out). In other words, the first pallet to enter must be the first to leave.
Pallet Shuttle system
The compact block of racks is operated by two Pallet Shuttles, occupying about 780 m2 of space and containing a storage capacity for 2,850 pallets of 800 x 1,200 mm with a maximum 1,000 kg unitary weight. Standing 10 m tall, the racks have five shelf levels and 95 storage channels overall. Each one of these is able to deep store 30 pallets.
The Pallet Shuttle system, besides maximising available space through the high-density racking, also increases workflows by cutting the time used to slot or extract pallets from the channels. The motorised shuttle is tasked with carrying out in-channel movements, requiring minimal worker involvement.
The semi-automatic Pallet Shuttle system functions as follows:
- The operator inserts the Pallet Shuttle into the corresponding channel by means of a forklift.
- Once the shuttle is in the channel and the pallet already loaded, it moves horizontally till it reaches the first open location, where the shuttle deposits the pallet.
- While the shuttle transfers and deposits the pallet, the operator uses this interval to place another pallet in the channel’s first position. Thus, when the shuttle returns to the front of this lane, it can sequentially repeat the same movement.
When it has finished loading in a channel, the Pallet Shuttle is moved to where it will keep operating. The extraction of merchandise is done through the step described above, but in reverse order.
Frontal stops were installed on each storage lane. Meanwhile, the storage channel entry/exit points contain centralisers that encourage proper unit load positioning and centring.
Live racking
In an approximate 640 m2 area, live rack blocks were enabled. The 92-channel system features 24.8 m deep lanes that hold 20 pallets. The five-level storage block reaches 9.6 m vertically.
Pallets are slotted into the uppermost point of the racks, moving autonomously to the other end, where they wait to be extracted. The slant of the channels facilitates the proper gravity displacements of the pallets. The speed in which they slide over the wheel tracks is controlled via a brake mechanism. The ramp at the lane end halts the pallets progressively.
Workers’ movements are limited, since they only set or retrieve pallets from the assigned locations, while operating a front-loading forklift. Plus, distances to cover are minimal since all SKUs are located in the same aisle.
Advantages for Manantiales del Portell
- More storing power: the Manantiales del Portell warehouse is set up to house more than 4,600 pallets in roughly 1,420 m2.
- Flawless product rotation: the Pallet Shuttle system and the live racks function as per the FIFO criterion (first in, first out), which is highly-suited to storing perishables like bottled water.
- Safety guaranteed: both the Pallet Shuttle and the live warehouse racks have safety devices to protect the structure’s cohesive properties, the goods and the workers.
Live racking | |
---|---|
Storage capacity: | 1,840 pallets |
Pallet size: | 800 x 1,200 mm |
Max. pallet weight: | 1,000 kg |
No. of channels: | 92 |
No. pallets/channel: | 20 |
Racking height: | 9.6 m |
Gallery
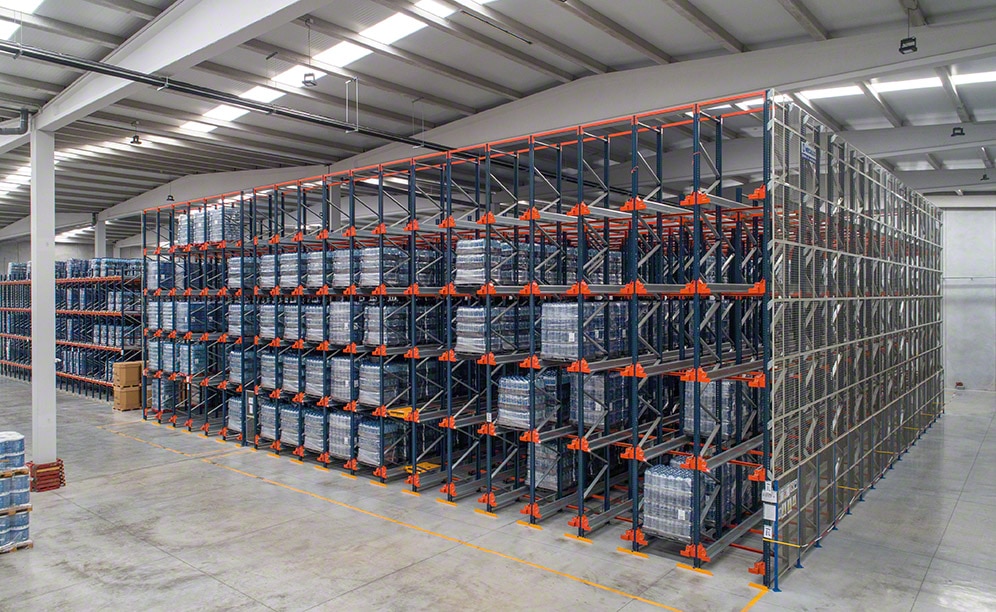
Warehouse of 4,600 pallets with the bottled water of Manantiales del Portell
Ask an expert