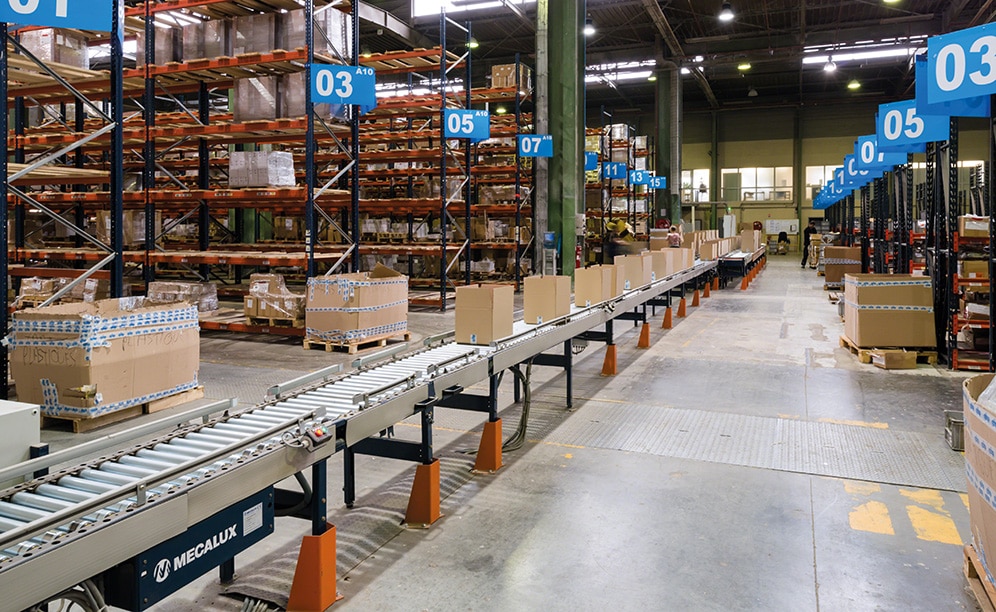
A full conveyor circuit multiplies the picking productivity of DYI goods manufacturer Vynex
The Vynex distribution centre boosts dispatches with conveyor circuits and picking stations
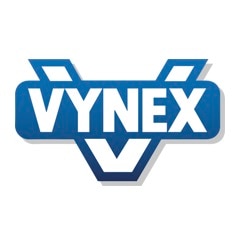
Mecalux has supplied a conveyor circuit in the Vynex distribution centre in the Ardennes region (France). This solution connects all the areas that make up the warehouse, streamlining and maximising picking throughput, the prime operation of this facility.
About Vynex
Vynex is a well-known French hardware brand, which was created in 1920 in the Ardennes region. In the 50s, the company foresaw the popularity DIY would gain with the general public and so created a line specifically for domestic use, while continuing to develop its professional products.
This vision launched Vynex to the front of the pack. Now its products are sold in much of Europe, with plans to expand its market share into more European countries.
Needs and the solution
The new Vynex centre, chiefly dedicated to picking, has over 20,000 SKUs of different sizes, weights and classifications that are stored taking into account their features.
The company needed that its personnel could prepare multiple orders at a time in the most efficient manner possible, as well as increase the number of daily dispatches.
Following an in-depth needs analysis, Mecalux chose to provide a conveyor circuit, which runs through the centre of the warehouse at a speed of 25 m/min, joining all areas. Along the route, there are five picking stations.
This solution provides great flexibility when picking orders because operators do not have to run all over the warehouse to select the products that make up each order but only work in an assigned area.
The end of the circuit culminates in the dispatch area, where orders are classified by routes or destinations before being distributed.
Picking
The picking method selected in this warehouse is based on the "person-to-goods" criterion, i.e., operators move to the shelves using handcarts to manually collect SKUs indicated to them by the warehouse management software (WMS). Picking will shortly be carried out by means of a voice command system to improve the service quality even further.
Reserve pallets are stored in pallet racks located at the beginning of the conveyor circuit. The replenishment of the goods is done during off-peak hours when there is less order picking.
The picking process starts with the manual set up of boxes. The WMS specifies the number and size, taking into account the composition of each picking wave. Vynex's warehouse principally employs two types of boxes: 570 x 370 x 235 mm and 400 x 285 x 235 mm with a maximum weight of 25 kg.
Five picking stations are installed, four of them grouped together –one in front of the other–, separated by the main conveyor circulating in the centre; and a single strand conveyor, attached to the wall. Each corresponds to a particular number of racks (sector). The number of operators who can work at each station varies, depending on the quantity of orders that need to be prepared.
The stations consist of non-motorised rollers so that operators can manually move the boxes to the most comfortable position.
When personnel have finished their part of the order, they introduce the boxes onto the central conveyor that moves to the next station to continue the process. In the event the order has been completed, it is routed directly to the verification and packaging area.
There the weight is confirmed, the order is checked for completeness and that it contains the correct items. Finally, the boxes are closed, packaged, labelled, and delivery notes and documentation are issued.
In the dispatch area, orders are automatically classified into five channels located in front of the loading docks. Operators distribute the goods on the different pallets, organised by customer or shipping routes.
In each of the channels, monitors are installed providing operators with all the necessary information to sort orders accurately and efficiently.
The conveyors are adapted to the features and distribution of the warehouse. The circuit incorporates straight and curved lines, as well as three open passageways to facilitate access of personnel through hinged conveyor sections. Once operators have crossed through, they put it back into position for the goods to continue moving.
WMS and control unit
The WMS is responsible for organising all of Vynex's warehouse operations and is in constant communication with the Mecalux Galileo control module. This module gives movement orders to the conveyor circuit, directs the boxes to the corresponding stations or areas and finally classifies them into channels.
Advantages for Vynex
- Operational flexibility: the sectoring of the warehouse offers flexibility when picking orders, as each cell is assigned a number of shelves and operators, which varies according to demand.
- Fast picking system: the inclusion of the automatic conveyor circuit maxes out the velocity of the entire operation.
- An integrated warehouse: a conveyor circuit links the different storage areas. Thus, operators do not have to run all over the warehouse to pick orders, achieving top efficiency.
Vynex distribution centre in France | |
---|---|
Storage capacity: | 6,334 pallets |
Picking locations: | 23,618 (6,334 for pallets) |
Orders per day: | 5,000 |
Conveyor length: | 284 m |
Conveyor speed: | 25 m/min |
Gallery
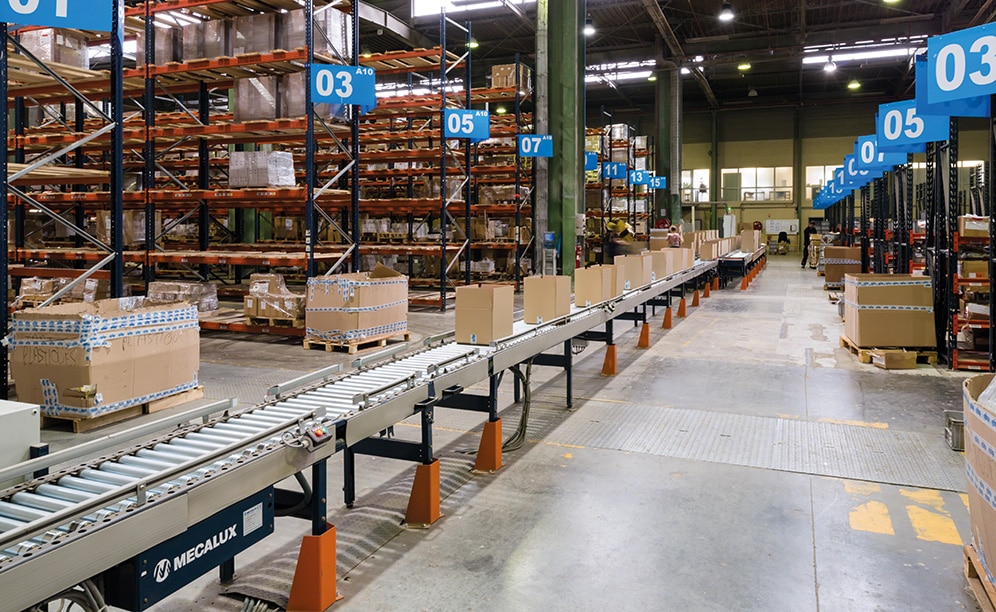
Mecalux chose to provide a conveyor circuit, which runs through the centre of the warehouse at a speed of 25 m/min, joining all areas
Ask an expert