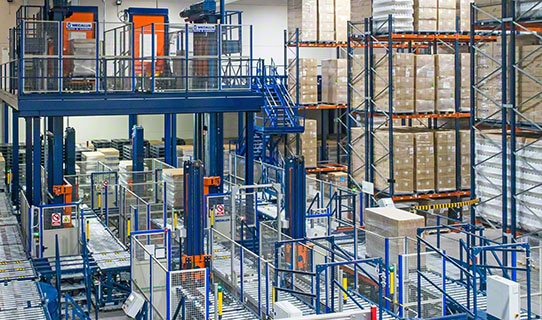
A manual warehouse is automated without disrupting operations
IKEA Components has turned its manual warehouse in Malacky, Slovakia, into an automated one without stopping operations. It has installed trilateral stacker cranes and pallet conveyors in each of the facility’s 12 aisles, in addition to Easy WMS.