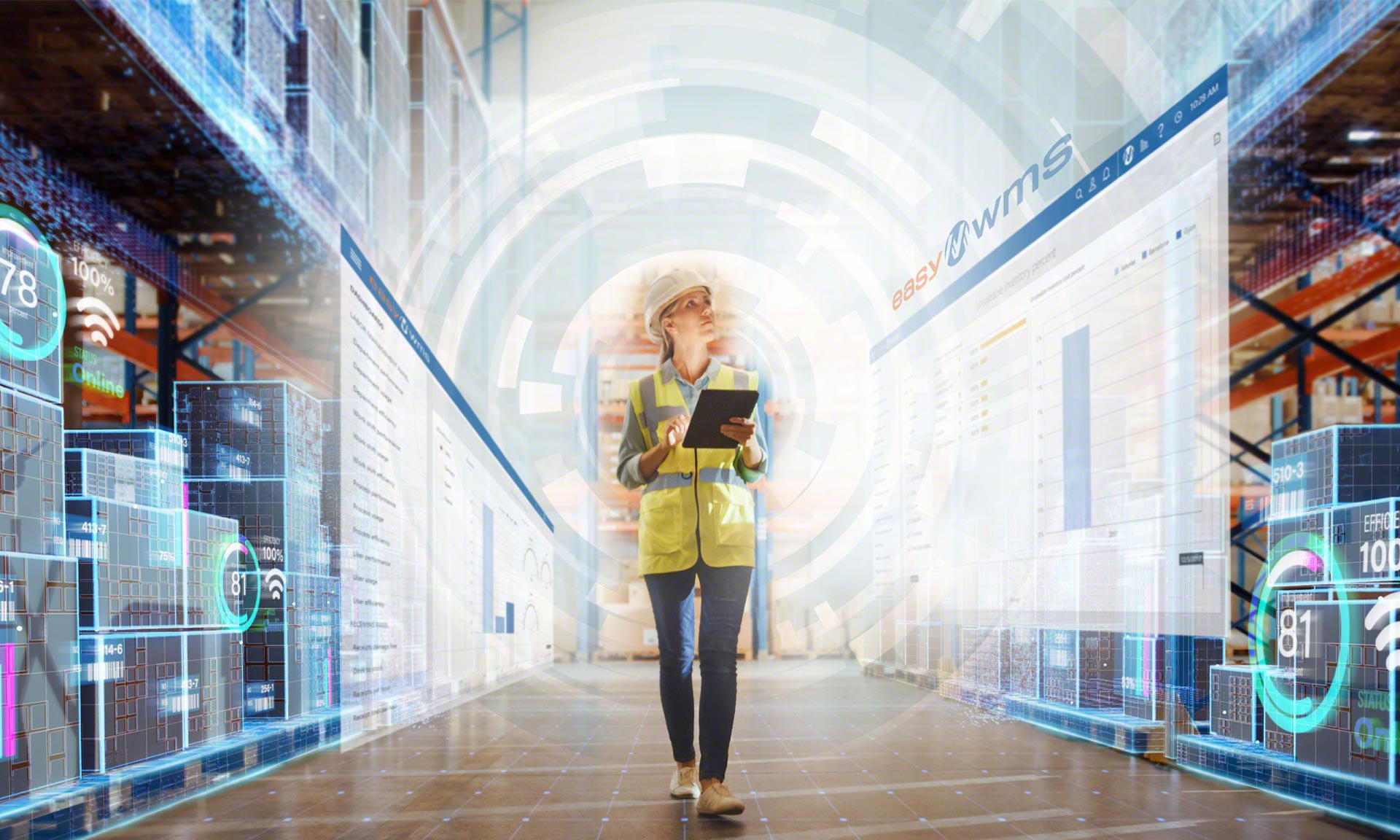
Digitisation transforms the supply chain
Carglass instals Easy WMS in its warehouse in Slovenia and overhauls operations in its nine other facilities
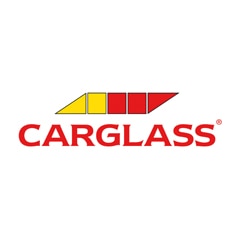
Carglass, which specialises in the repair, replacement and recalibration of car windows, has installed Easy WMS from Mecalux in its warehouse in Slovenia. The company can now accurately monitor its 8,000 SKUs in stock and streamline its storage and order picking tasks.
Belron (Carglass®): the best service for drivers
Carglass, which forms part of the Belron group, is a leading company in the repair, replacement and recalibration of car windows for any brand, model or year of manufacture. Its priority is to resolve its customers’ problems as satisfactorily as possible, repairing vehicle glass instead of replacing it in order to save time and money.
- Founded in 1897 in Cape Town, South Africa
- International presence: 40 countries
- No. of employees: 27,000
- No. of customers per year: 14.9 million
CHALLENGES
|
SOLUTIONS
|
BENEFITS
|
---|
“We wanted to digitise our logistics infrastructure because the number of SKUs just kept growing, and it became difficult to control them all,” says Dejan Šeruga, General Manager at Carglass in Slovenia. The vehicle window repair and replacement company knew that digitising its warehouse was the best way to speed up operations and avoid stockouts.
Carglass has equipped its 600 m² central facility in Celje (Slovenia) with the Easy WMS warehouse management system from Mecalux to control its 8,000 SKUs and optimise all operations. Šeruga says: “Easy WMS orchestrates all the processes, from goods receipt and storage to order preparation and dispatch.”
On the one hand, digitisation through Easy WMS has served to improve warehouse operations. On the other hand, it has motivated the company to reorganise its entire supply chain. “We decided to instal Easy WMS in the Celje facility because, after analysing it, we felt that this should be the central warehouse that would supply the other three as well as our nine repair shops in Slovenia," says Šeruga.
The warehouse is also outfitted with picking shelves designed by Mecalux to house the car windows, which are properly protected and labelled.
Challenges of manual logistics
Previously, Carglass organised all its logistics operations with the help of its VASCO ERP (enterprise resource planning) system. To perform tasks, operators would print a piece of paper specifying the orders to prepare or the SKUs needed to complete each order. However, this way of working had its drawbacks.
For starters, the risk of making mistakes was very high, and this was something the businesses was determined to prevent. The different types of auto glass are very similar, and they are all identified with a very long and complex code. At times, the operators would send the wrong glass part to repair shops, making it necessary to return them and send additional orders. This resulted in delays and in customer complaints.
When it came to managing the goods, the company’s dependence on the operators was absolute. Upon receiving orders, these employees had to jot them down on paper and then enter them into the ERP system. “One disadvantage of manual management was that, if an employee was absent, that could cause service delays,” says Šeruga.
Another issue Carglass wanted to resolve was the lack of organisation in storage and order picking tasks. Items were stored in any location, meaning operators had to walk around the entire building to find the corresponding SKU. “It was a highly unproductive dynamic that generated additional costs,” says Šeruga.
But the real tipping point was inventory control. Šeruga says: “It was a disaster.” Stock imbalances were quite common. For example, items that should have been in stock, theoretically, were missing.
Order dispatch was another critical point for Carglass’s logistics operations. “For every order, we had to print a delivery note specifying the items to be located in the warehouse. Once the orders were finished, the operators would enter into the ERP system the auto glass they’d picked to inform the repair shop of their impending shipment,” says Šeruga.
“We were aware that this was an infeasible way of working in the long term. We reached a critical juncture when we opened our new warehouse in Celje in 2020. The number of SKUs rose quickly, and we realised we would have to abandon manual management of the goods,” says Šeruga. So, Carglass began the search for a warehouse management system (WMS).
Benefits of a digital facility
Carglass contacted technology company Špica to equip its central warehouse with advanced warehouse management software. “This is one of the biggest projects Carglass Slovenia has driven forward in recent years, so we wanted to count on the support of a partner that had the necessary expertise and a proven track record in the sector. We chose Špica because it’s one of our country’s main suppliers of technology solutions for the supply chain. Together, we found the warehouse management system that would best meet our needs. Špica has highly qualified team of experts and excellent references. The whole company was fully dedicated to the project, and together, we managed to find the right warehouse management system,” says Šeruga.
Špica analysed Carglass’s requirements and proposed installing Easy WMS from Mecalux, a WMS capable of accurately controlling the company’s 8,000 SKUs, preventing stockouts and reducing errors. “Easy WMS intervenes in all processes taking place in the facility, from goods receipt and product storage to order picking and the shipment of car windows to repair shops,” says Šeruga.
To supervise and optimise all processes, Easy WMS has been integrated with Carglass’s VASCO ERP system. Both software programs exchange data and information that are essential for managing the warehouse effectively and for ensuring the profitability of all logistics operations performed there. The ERP system, for example, notifies Easy WMS of the orders to prepare so that it can organise the work of the operators.
Another of the most obvious advantages of digitising the Carglass facility is the replacement of paper when carrying out any task. The operators travel about the warehouse using RF (radiofrequency) scanners that receive instructions from Easy WMS. “The RF scanners are very easy to use. Compared to our old way of working, the operators are much quicker and more accurate when doing any of their tasks,” says Šeruga.
Carglass has also seen a notable improvement in warehouse processes, especially stock management. Every day, the facility receives a multitude of pallets from suppliers and Carglass warehouses to be sent to other Carglass facilities in different European countries (namely Germany, Austria, Belgium and Italy, among others). As the pallets arrive, the operators identify each of them by reading the barcode with their RF scanners. Easy WMS then prints a label for each vehicle window part, specifying the serial number, supplier data and the brand. Finally, it assigns each glass part a location taking into account those variables. “With Easy WMS, the receiving process is much faster than before. This has allowed us to save time, which we can now dedicate to other processes,” says Šeruga.
Easy WMS has also facilitated and expedited order preparation and dispatch. The Carglass warehouses and repair shops in Slovenia order the items they need from the central facility. The operators immediately locate the requested car windows and dispatch them as soon as possible. “Order picking is much more dynamic. We no longer lose time preparing the necessary documentation; that is, when a customer orders a car glass part, it’s located and shipped at once. The operators can find the items more easily now,” says Šeruga. Before digitising the warehouse, operators typically had trouble finding the car windows they needed. However, this has not occurred with Easy WMS. “Customer satisfaction has improved,” says Šeruga.
In addition to optimising Carglass’s central facility, Easy WMS has also had a direct impact on the company’s entire supply chain in Slovenia. “We’ve leveraged the digitisation of our central warehouse to make a number of decisions aimed at enhancing our other facilities. We’ve maximised the available space, prioritising order and cleanliness. Plus, we’ve chosen to store only the stock that’s essential for providing service, to train our operators continuously and to renew our fleet of forklifts,” says Šeruga.
Supply chain transformation
“Despite the coronavirus pandemic in 2020, we managed to improve our bottom line compared to 2019. And we want to keep growing in 2021 and beyond. To this end, we’ve applied measures that we hope can help us to provide our customers with better service,” says Šeruga.
The digitisation of the central facility in Celje is the first step to optimising the company’s supply chain. This flexible, user-friendly, highly personalised system has enabled Carglass to enhance its warehouse processes and accurately control all its SKUs in order to ensure speedy order distribution.
The transformation of the Celje facility has underlined the importance of logistics for Carglass. Likewise, Easy WMS has given Carglass more control over all operations. “The software generates reports on everything happening in the warehouse. The information collected allows us to analyse different scenarios and apply strategic improvements,” says Šeruga.
The Mecalux software has improved operations in our central warehouse in Slovenia and bolstered our entire supply chain. Digitisation of the facility has helped to optimise processes and to reduce errors in goods receipt and dispatch. With Easy WMS, we can accurately control the 8,000 SKUs and know exactly how much stock we have in real time.
Gallery
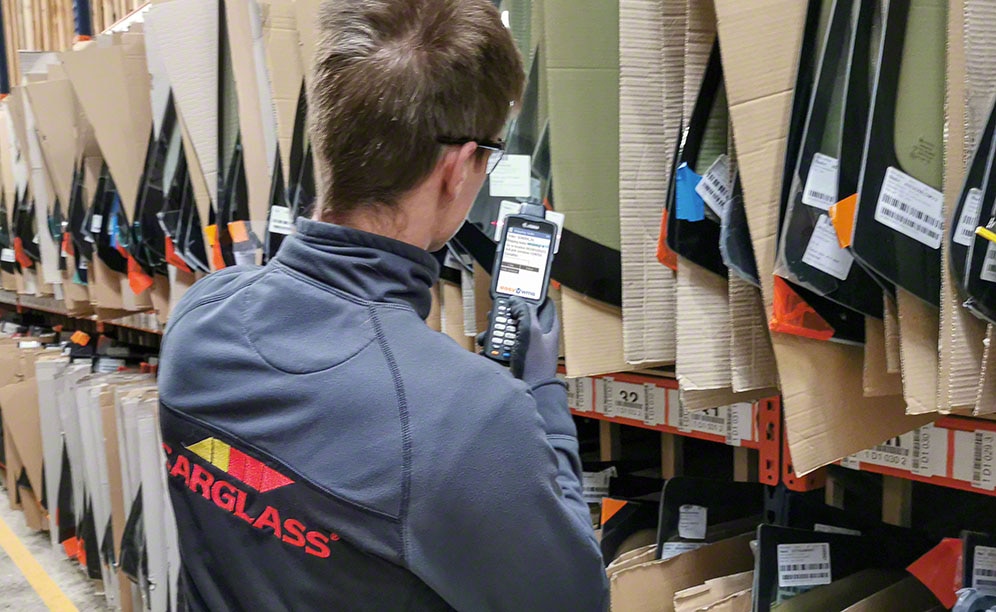
A Carglass operator follows instructions from Easy WMS
Ask an expert