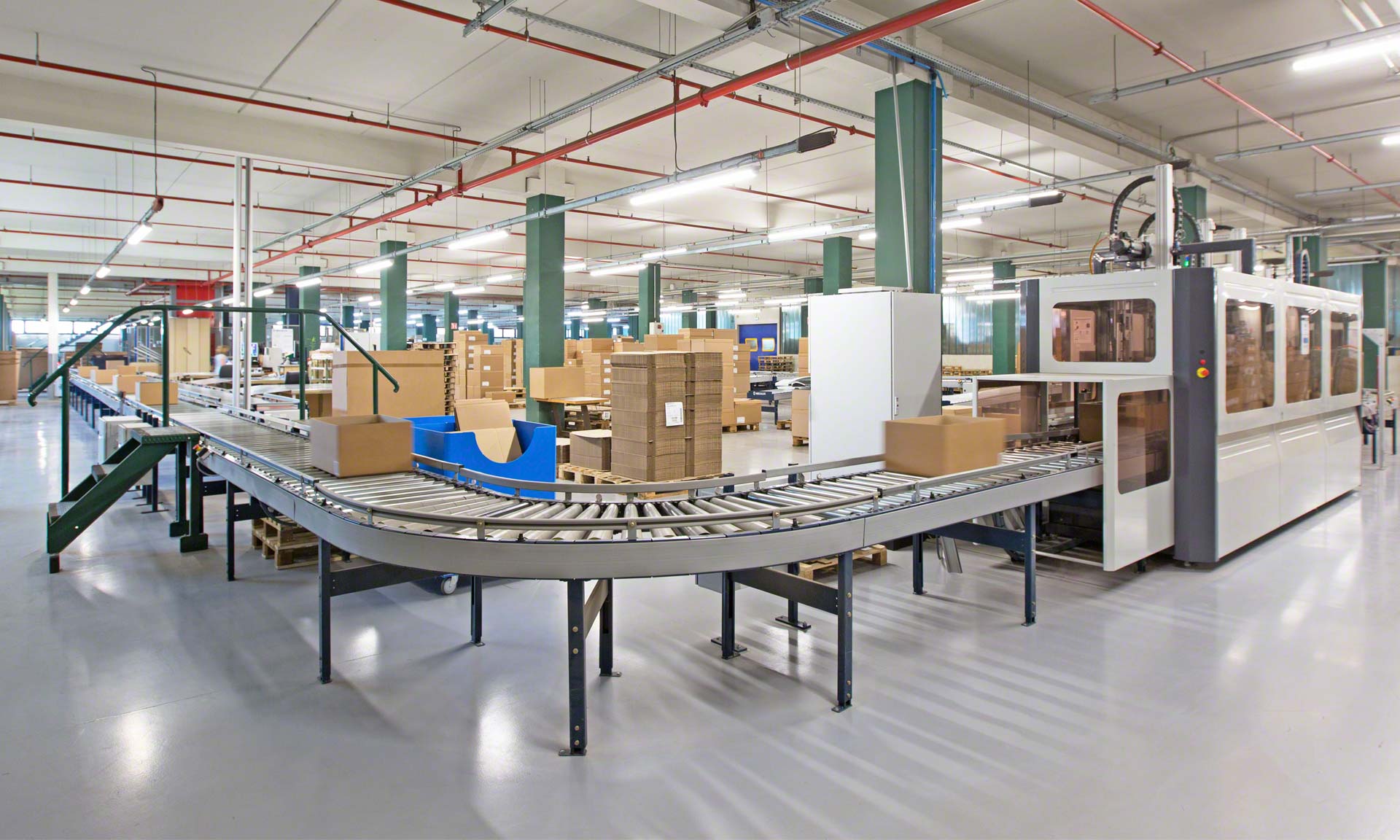
Firm step towards automated omnichannel
Omnichannel warehouse divided into three floors connected automatically
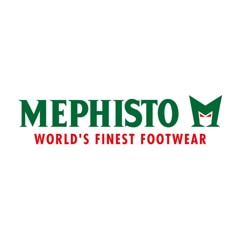
Omnichannel retail has completely transformed warehouse operations and, more specifically, order preparation. To tackle this challenge, footwear manufacturer Mephisto has optimised its logistics centre in Alsace, France, in order to dispatch up to 3,500 orders a day, which are then distributed to its online customers and its 900 physical shops worldwide. Mecalux has installed storage solutions that facilitate the organisation of 35,000 SKUs, in addition to conveyors and lifts to automatically connect the facility’s three floors.
Tradition meets innovation
Founded in 1965 in Sarrebourg, France, Mephisto is a shoe manufacturer with more than 900 stores in countries such as France, the UK, the US, Germany and Italy and more than 18,000 points of sale.
With the aim of meeting market demands, the company has decided to take a definitive step into the world of e-commerce. It has recently opened its online shop, where customers can purchase the models of their choice and conveniently receive them at their doorstep. From a logistics point of view, adapting to omnichannel retail when managing 35,000 SKUs involves very demanding operations, with many orders to prepare and deliver in a matter of hours.
In Sarrebourg, the company has a production plant and a 18,000 m² warehouse that it came to outgrow with the increase in production and consolidation of omnichannel sales. Shoes are distributed from this facility to shops and to customers that shop via the Mephisto website.
The company wanted to reorganise its warehouse to foster its B2C strategy. To do so, it contacted Mecalux because, according to Christian Kalch, Industrial and Logistics Manager at Mephisto, it has a wide variety of solutions for any need: “We chose Mecalux because of its professionalism and the excellent price–performance ratio of its automated and manual storage systems. We were also impressed by the presentation Mecalux gave us at its showroom in Barcelona, where we were able to check out the characteristics of the storage systems.”
Three floors connected automatically
To triple the useful storage space and accommodate a larger number of items, Mephisto has divided its warehouse into three work floors:
- Ground floor. This includes the production lines, the receiving area (which receives goods sent by the Sarrebourg production plant and raw materials used to manufacture shoes sent by suppliers), the consolidation zone and a storage area.
- Upper floors (first and second). Here, Mephisto’s 35,000 SKUs are strategically stored by SKU, characteristics and turnover. Most orders are prepared on these floors, following the person-to-goods method: the operators go around the warehouse locating the products required to make up each order.
The three floors are connected to each other by means of pallet and box lifts. The pallet lift moves the pallet automatically to the floor on which it will be stored. The box lift, on the other hand, automatically lowers picked orders to the consolidation area, where they are packed, sealed and labelled.
Designed for picking
Every day, 2,000-3,500 orders are prepared in this facility and dispatched all around the world. The high workload and broad array of products in stock call for an orderly warehouse to prevent mistakes and delays in deliveries.
Therefore, Mecalux has equipped the facility with two solutions that speed up storage and order prep tasks in addition to providing direct access to the goods, facilitating management of the thousands of SKUs. The installation of the two solutions - pallet racks and picking shelves - was carried out without interrupting, at any time, the pace of shoe production or the shipment of orders.
Pallet racks are the most universal system for direct access to each pallet. Mephisto’s racks stand 6.5 m tall and house 1,920 pallets. The company uses them mainly to store palletised goods about to be dispatched to shops, high-turnover products, and reserve merchandise to be placed on the picking shelves.
Meanwhile, the picking shelves measure 2.5 m high and offer direct access to the smaller goods (shoe boxes). Just as with the pallet racks, direct access is fundamental for inserting and removing products easily and quickly. Kalch says, “The two storage solutions have changed the organisation of the entire warehouse and have marked a turning point for our business. Thanks to the optimal distribution of the goods, operators can locate products and put together orders much faster. As a result, we’ve improved our efficiency in order picking.”
Order preparation procedure
Operators are assigned a work area on the two upper floors of the warehouse, where they prepare orders by order grouping. They travel around the warehouse, picking the items that make up the various orders.
To do this, they move up and down the aisles using a cart with eight slots, locating the products they need on the shelves and placing them in the cart. Generally, each location in the cart is allocated to one order.
Once the orders are finished, the operators place them on the box conveyors. These greatly speed up order prep, as operators need not move the boxes to the consolidation area; the conveyor does it autonomously.
If the operators had to prepare one order after another individually, they would require much more time, since most orders include stock from different work areas. For that reason, the order grouping method is extremely efficient in a warehouse such as Mephisto’s.
At the same time, the consolidation area plays a key role. There, the items contained in each order are grouped together to check that the orders have been properly completed and that no items are missing.
Ground floor of the warehouse
Once the orders reach the ground floor, the last processes prior to dispatch are carried out. First, the orders are weighed to verify that they meet the parameters established for their distribution. Next, they head for the personalisation area, where customer requests are implemented, such as adding advertising brochures or placing price labels on the shoe boxes.
The orders are then moved to an automatic sealer and an automatic labeller. This ensures that they are correctly sealed and identified to facilitate their transport.
Finally, the products arrive at the sorting area, where they are grouped by transport route. This zone consists of nine 3-metre exit ramps that operate with the conveyors by means of gravity; that is, they are slightly inclined to allow the boxes to slide to the end of the conveyor.
Each ramp corresponds to a lorry or to a single delivery route. The operators pick the boxes from each ramp and leave them on a pallet, which will be loaded onto the lorry.
Step forward in efficiency
Footwear manufacturer Mephisto has completely revamped its warehouse in France to successfully implement an omnichannel strategy. Orders are sent from this facility to thousands of points of sale and online customers.
To do this, the company has invested in storage solutions that provide direct access to the goods and to automated transport systems that expedite product distribution.
The automated conveyors and lifts together with the pallet racks and picking shelves from Mecalux have helped Mephisto to prepare and dispatch up to 3,500 orders a day.
Moreover, with all these solutions, the company is now able to house a larger number of products: 35,000 SKUs in 18,000 m².
Advantages for Mephisto
- 3,500 orders a day: the proper distribution of the products has had a positive effect on warehouse productivity, streamlining storage and order preparation tasks.
- 35,000 SKUs stored: Mephisto has tripled its useful storage area to maximise its capacity.
- Automatic connection: the three warehouse floors are linked by pallet and box lifts, ensuring safe and speedy goods movements.
Mephisto responds:
Interview with Christian Kalch, Industrial and Logistics Manager at Mephisto
- What were the logistics needs of the Mephisto warehouse?
Our facility was 33 years old and was becoming obsolete in the face of the changes in our business. The minute we decided to bolster our B2C strategy, we realised we had to expand the storage area, redirect flows, speed up operations and ramp up productivity. In short, we were looking for efficiency.
- What led Mephisto to automate goods movements in the warehouse?
Our main priority was to increase agility because we know this is the best way to serve customers and to implement an effective B2C strategy. Thanks to automation in the form of the conveyors and lifts, flows are much quicker, and we’ve significantly reduced operator movements.
-
Mecalux has become an invaluable partner for improving our logistics operations.
- What did the warehouse renovation involve?
We’ve revamped our facility with the aim of modernising our supply chain. Mecalux has installed pallet racks and picking shelves as well as conveyors and lifts that automatically connect the three floors that make up the warehouse. The racks, lifts, and conveyors are made of high-quality materials that guarantee excellent durability. As a result of these solutions, our warehouse has been completely reorganised, and the distribution of our 35,000 SKUs is much more logical. We’re thrilled with our current warehouse; it’s gone above and beyond our expectations.
- What are Mephisto’s future prospects?
Our goal is to serve our customers efficiently, eliminating errors and delays. To do this, we must constantly renew ourselves; we’re not afraid of change. In the future, we’ll definitely be able to further improve our storage and order picking tasks through robotics and automation.
Pallet racks | |
---|---|
Storage capacity: | 1,920 pallets |
Pallet size: | 800 x 1,200 mm |
Max. pallet weight: | 600 kg |
Racking height: | 6.5 m |
Gallery
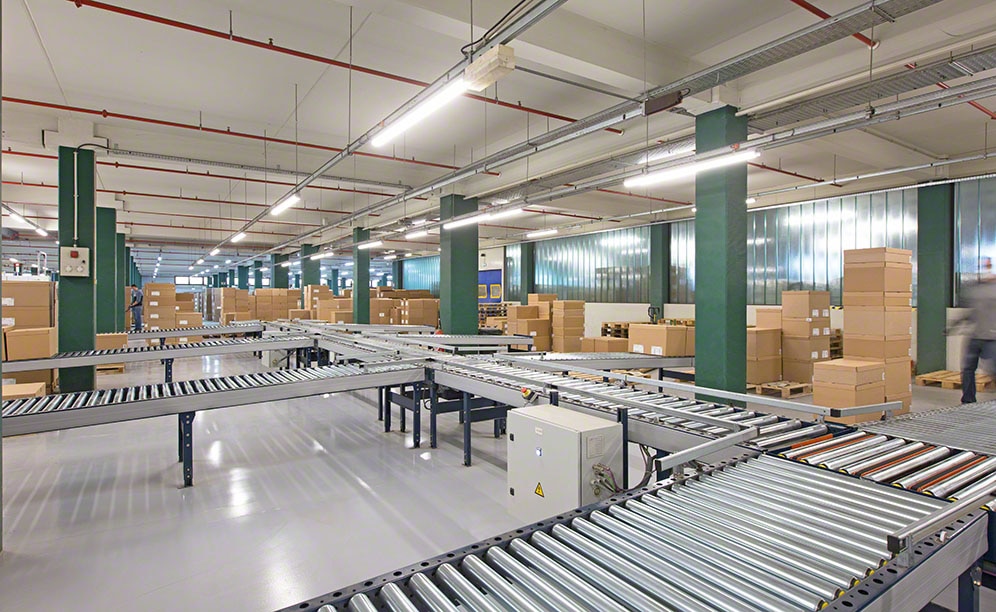
Mephisto's omnichannel warehouse with box conveyors
Ask an expert