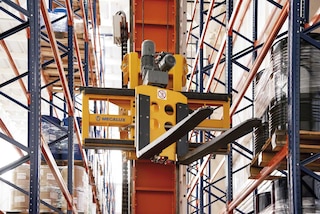
AS/RS warehouse: safe loading and full autonomy
The incorporation of stacker cranes is a common solution when it comes to fully automating logistics operations. Many companies turn to an AS/RS warehouses (Automated Storage and Retrieval System) to ramp up their productivity, with stacker cranes at the core of these types of installations.
This equipment, charged with storing products in their locations automatically, is ideal for providing agile, efficient, error-free service at a lower cost.
Below, we’ll take a look at stacker cranes, examining their characteristics, applications and advantages.
The role of stacker cranes in an AS/RS warehouse
Let’s start with the definition of a stacker crane: it’s a machine devised to automatically store and retrieve goods (mainly, pallets, boxes, containers and even tires). These machines are equipped with a microprocessor, an electric component responsible for processing and executing the instructions of a warehouse management system (such as Easy WMS from Mecalux).
Stacker cranes pick products from one end of an aisle and bring them to the racking location assigned to them, inserting them into the designated slot. In addition, they remove the load from the rack and carry it to the outgoing conveyor or console at the end of the aisle. These two operations as a whole are known in logistics as a combined cycle, that is, when one pallet is deposited, another is extracted during the same stacker crane trip.
These machines represent the evolution of traditional handling equipment, such as narrow aisle forklifts, for example, with operators onboard orchestrating and managing their actions and movements. Stacker cranes with microprocessors, on the other hand, operate with complete autonomy.
How do stacker cranes work in an AS/RS warehouse?
Stacker cranes move along rails and incorporate an extraction system that makes it possible to place the unit loads on the racks (regardless of whether they are single- or double-deep).
They have three different operational modes, based on the specific needs of each installation:
- Automatic. Most stacker cranes operate in this way, in which goods placement and retrieval actions are carried out automatically: the stacker crane is controlled by the PLC (programmable logic controller), a computer in charge of managing all the machinery in an AS/RS warehouse. The stacker crane receives orders from the warehouse management system via a microprocessor or an integrated programmable PLC located in the main control cabinet. The software tasked with coordinating the various PLCs operating in an AS/RS warehouse is known as a warehouse control system (WCS).
- Semi-automatic. This comprises a computer at one end of the aisle run by operators to send instructions to the stacker cranes. The employee enters the coordinates required by the stacker crane to make any type of movement. This mode performs support functions, such as accessing specific locations and re-slotting goods.
- Manual. This modality is used primarily for maintenance and repair tasks. From a cabin, the employee operates the machine by means of hand controls and at a low speed. It should be noted that stacker cranes are integrated with safety systems, for instance, safety cables and maintenance platforms to protect workers using these machines.
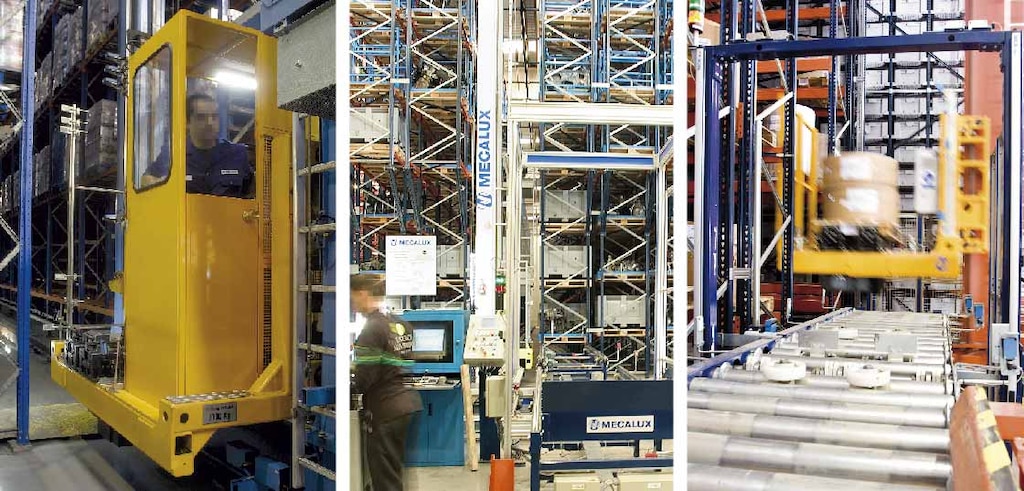
When to install a stacker crane in my AS/RS warehouse
Stacker cranes consist of handling equipment used to automate all types of logistics installations, from existing warehouses to new logistics centres and in both traditional buildings and clad-rack warehouse structures.
As a general rule, companies consider automating their facilities (completely or partially) when they want to boost the throughput of their installations, improve their level of service and ensure the safety of the goods and operators.
Stacker cranes are especially advisable when managing a large variety of medium- and high-consumption SKUs and when seeking to increase movements (inbound, outbound, or combined cycles/hour).
These machines can be set up in an aisle with single- or double-deep racks on both sides, depending on the storage capacity required. They can also be combined with the Pallet Shuttle system to condense storage space and accommodate a higher number of products.
Stacker cranes are particularly recommended for operating in cold storage warehouses, whether cold or freezer stores. Automation reduces the volume to be cooled and prevents operators from prolonged exposure to low-temperature environments. Stacker cranes can operate uninterruptedly in temperatures as low as -22 °F.
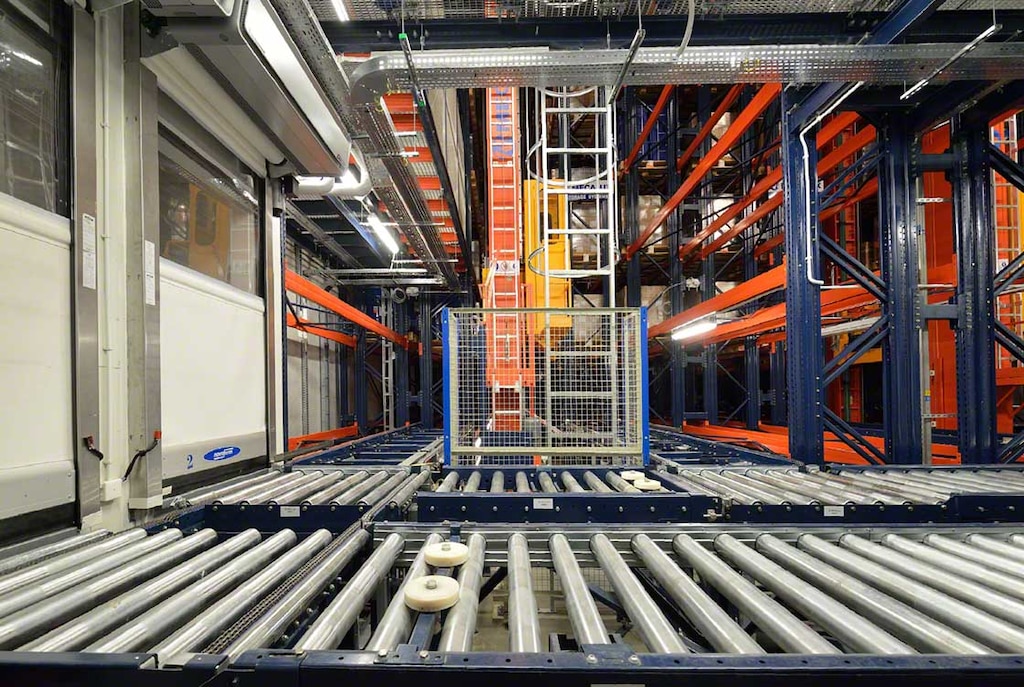
Pros and cons of stacker cranes in an AS/RS warehouse
Stacker cranes comprise a system for handling boxes and pallets that offers the following advantages:
- Space maximisation. This is due to their high-density storage capacity, in terms of both square footage and height (up to 150') and to the fact that they can operate in very narrow aisles (5').
- High level of accessibility to loads Stacker cranes enable quick, direct access to the all the products stored. Pallet entries and exits are carried out through two types of movements: simple (only product entries or exits) or combined (a product is entered into the warehouse and that movement is leveraged to remove another one).
- Real-time inventory. In an AS/RS warehouse run by a stacker crane, it’s essential to have a warehouse management system to accurately monitor the pallets. Real-time inventory lets you know exactly where each item is located at all times. Thus, errors stemming from manual management are eliminated.
- Complete load safety. The goods are handled automatically, without operator intervention, preventing accidents and mistakes.
- Full availability and productivity. This automated system can operate continuously 24/7, making it ideal for companies with a high number of movements and intense picking activity.
- Energy efficiency. Stacker cranes incorporate power regenerators, which return to the power grid the energy generated during the descent maneuvers and deceleration of the axis; this translates into an average savings of 15%-20% of the machine’s total energy consumption. The goal is to promote green logistics, which reduces the environmental impact of business activities.
Nevertheless, installing a stacker crane in an AS/RS warehouse poses some drawbacks, mainly:
- Initial investment. Automating a warehouse requires a higher initial outlay compared to that of an installation that’s run manually. However, it’s clear that the return on investment (ROI) is more substantial compared to that of a conventional warehouse. Bear in mind, though, that everything will depend on the specific circumstances.
- A single aisle. To get the most out of a stacker crane, it should only operate in one aisle (in other words, there should be one stacker crane per aisle). Of course, this costs more than using a single stacker crane in multiple aisles. The choice between using one stacker crane per aisle or one machine in various aisles will depend on the turnover of the products and the necessary movements.
- Dependence. In order to operate, stacker cranes need to be equipped with other auxiliary transport systems, namely conveyors. Set up at one end of the aisles, they bring the goods to the stacker crane, which can then deposit the products in their locations.
Productivity and maximum safety
Stacker cranes constitute automatic handling equipment capable of raising the productivity of any logistics installation. These machines move along rails embedded in the floor, inserting and extracting loads into/from their locations by following instructions from the WMS.
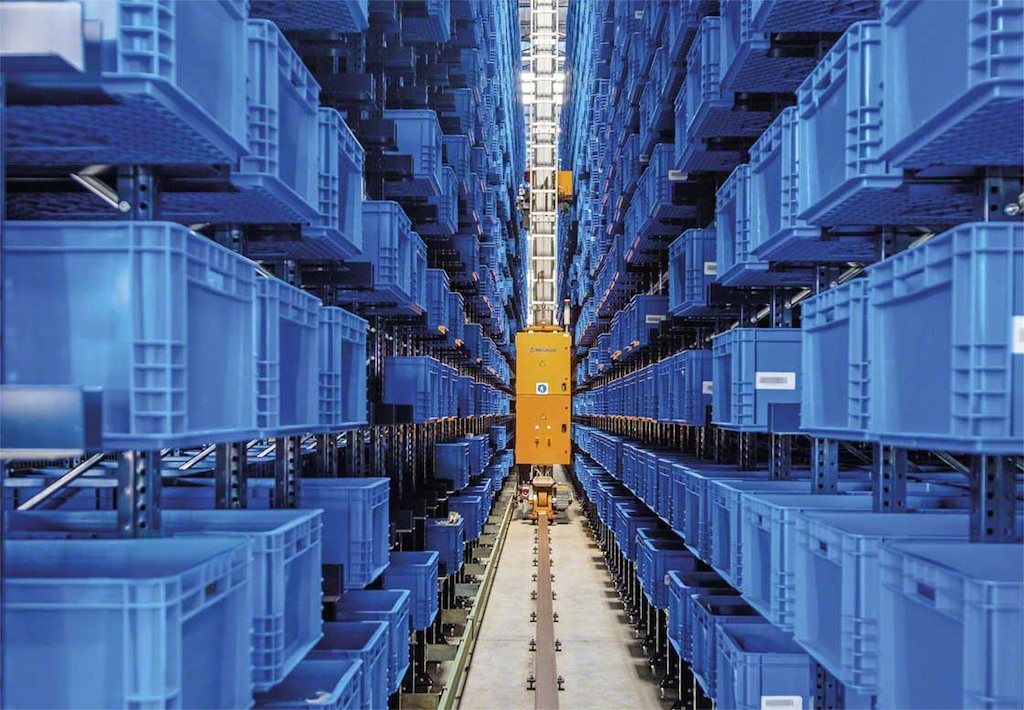
The combination of the stacker crane with the warehouse management system is vital for improving the operation of the facility. The WMS not only organises the movements of the stacker crane, but also controls all product entries and exits.
Mecalux’s stacker cranes have proven efficient in all types of warehouses for businesses in sectors as diverse as the food, automotive, pharmaceutical and chemical industries. If you’d like to take advantage of the features of an AS/RS warehouse, don’t hesitate to get in touch. We’ll fill you in on all of its advantages.