How to calculate the ROI of a warehouse, or the return on investment, is another crucial element that needs to be considered when choosing the best storage solution for a company.
Analyzing the cost of an installation and the return on investment is an exercise that can, and must, be included in any project. In most cases it is very simple and warehouse operators or owners can do it themselves. In other cases, the storage solution supplier will need to help its customers with this calculation.
The calculation of ROI consists of deducing the approximate time it will take to get back your initial investment. This calculation must always be performed by comparing at least two scenarios: the current situation compared with the new project (for companies with a warehouse they want to replace) or a comparison of two different solutions (for companies starting from scratch).
When completing the detailed calculation it is essential to consider all investment costs, plus operating costs (direct savings) and estimates of gains to be made in corporate image, customer services, control, etc. (also called indirect savings).
While based on real cases, to make the calculation easier to understand the analysis in this manual has been simplified. Only the largest figures are included, namely civil works (the warehouse building and its annexes), the storage system (racks), handling equipment and its performance and personnel.
To compare two options it is essential to have comparable initial data. In this example, they are as follows:
- A warehouse with a required capacity of 8,000 pallets measuring 800 x 1,200 x 1,450 mm.
- It must be possible to move 700 pallets in and another 700 pallets out each day.
- There is no picking.
- In the first phase will use an 8-hour work day.
- The space available for construction is 100 m long and 60 m wide, within a larger enclosed area.
Here it shows two options to fulfill these needs and limitations. Then, the ROI will be calculated to compare these scenarios. In any case, all costs shown here are approximate in nature, and may vary given when they are calculated and under which circumstance. Amounts are provided here merely to illustrate the calculation.
OPTION 1. PALLET RACKS WITH REACH TRUCKS |
This first option involves a 84 m long by 49 m wide warehouse, with an internal height of 36 ft. It occupies 4,851 m2, with a 19% expansion margin of the occupied surface area, in respect to the total surface area of the plot. This conventional industrial building has 8 loading docks, and a reception and dispatch area of 735 m2. As requested, the facility has a capacity of 8,000 pallets. The number of movements that can be performed by one forklift is 11 pallets in and 11 out per hour (22 in total), so nine forklifts will be required. With these resources, it will take 7.4 working hours per day to reach the 1,400 required movements (700 in and 700 out). If the warehouse runs 24-hour operations, its capacity for growth is 224%. |
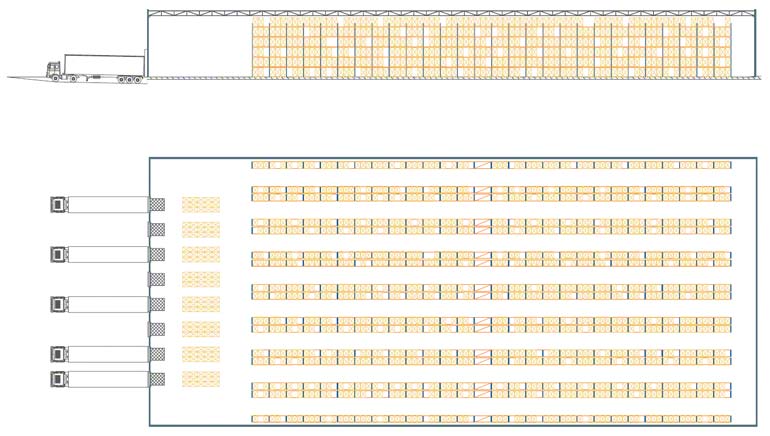
Pallet racks with reach trucks
Costs of this option ($*) | ||
Item | Quantities | Total cost (£) |
Forklift operators | 9 | 216,000 |
Reach trucks | 9 | 315,000 |
Racks | 8,000 positions | 312,000 |
Civil works (warehouse + dispatch) | 4,851 m2 | 1,454,400 |
OPTION 2. BLOCKS OF PALLET RACKS OPERATED BY DOUBLE-DEEP STACKER CRANES |
This second option uses the same space as the first, but only part of this is used to build the warehouse, leaving the rest available for expansion. The height of the warehouse up to the trusses is 24 m, inside an industrial building, as the previous option. The total built area is 2,953 m2, of which 2,218 m2 is the warehouse and 735 m2 used for reception and dispatch. The capacity obtained is 8,000 pallets, as requested. A stacker crane can perform 29 double cycles per hour (29 pallets in and 29 pallets out), so in this case three stacker cranes will be required. With these resources, it will require 8 working hours per day to carry out the number of movements required per day. Operating 24 hours a day, this installation could grow by 200%. The margin for expansion of the warehouse is 51%. |
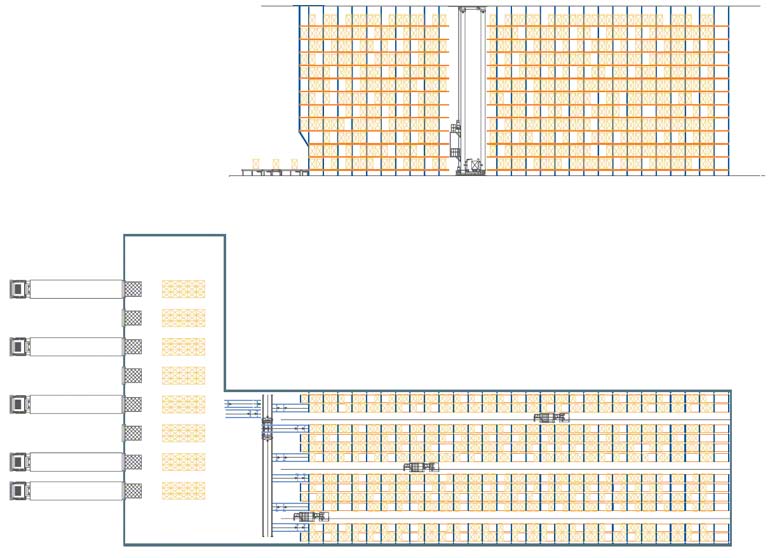
Blocks of pallet racks operated by double-depth automated stacker cranes for pallets.
Costs of this option | ||
Item | Quantities | Total cost (£) |
Forklift operator | 2 | 48,000 |
Stacker cranes | 3 | 855,000 |
Racks | 8,000 positions |
760,000 |
Civil works (warehouse + dispatch) | 2,953 m2 | 1,099,926 |
CALCULATING THE ROI | |||||||
The simple return on investment table is based on the total accumulative amount spent on the installation each year. With this information, and the workflows, one can determine which installation is best for you from a financial point of view. The calculation uses annual spending, taking into account the one time cost of the installation (included once in the first year) and recurring costs, such as personnel, are included each year. |
|||||||
Pallet racks operated by reach trucks (£) | |||||||
Year 1 | Year 2 | Year 3 | Year 4 | Year 5 | Year 6 | Year 7 | |
Amount from previous year | 2,297,400 | 2,513,400 | 2,729,400 | 2,945,400 | 3,476,400 | 3,692,400 | |
Forklift operator | 216,000 | 216,000 | 216,000 | 216,000 | 216,000 | 216,000 | 216,000 |
Forklifts | 315,000 | 315,000 | |||||
Racks | 312,000 | ||||||
Civil works (ware.+disp.) | 1,454,400 | ||||||
Sum total | 2,297,400 | 2,513,400 | 2,729,400 | 3,476,400 | 3,476,400 | 3,692,400 | 3,908,400 |
Automated warehouse with double-depth stacker cranes (£) | |||||||
Year 1 | Year 2 | Year 3 | Year 4 | Year 5 | Year 6 | Year 7 | |
Amount from previous year | 2,672,926 | 2,720,926 | 2,768,926 | 2,816,926 | 2,864,926 | 2,912,926 | |
Forklift operators | 48,000 | 48,000 | 48,000 | 48,000 | 48,000 | 48,000 | 48,000 |
Stacker cranes | 855,000 | ||||||
Racks | 760,000 | ||||||
Civil works (ware.+ disp.) | 1,099,926 | ||||||
Sum total | 2,672,926 | 2,720,926 | 2,768,926 | 2,816,926 | 2,864,926 | 2,912,926 | 2,960,926 |