Picking list: an example applied to the warehouse
A warehouse picking list (also known as a pick list) is a vital document when it comes to optimising order preparation.
Picking is, without a doubt, one of the logistics operations requiring greater organisation and accuracy. Perfecting it is key in order for the supply chain to be competitive and to ensure that orders are delivered without error and within the time agreed upon with the customer.
To do so, operators use a pick list. But what exactly should it contain? Can software be used to optimise it and make it more efficient? We’ll explain it all in this post.
Picking lists defined
A picking list is an internal document containing all the instructions a warehouse operator needs to follow to prepare an order.
Generally, a typical picking list includes shipping data, the location of the products in the warehouse and any other aspect related to order prep, such as the operator picking route. By implementing a warehouse management system (WMS), picking lists can be created automatically and in digital form. It can even be transmitted through voice commands, as we’ll see below.
Ultimately, the purpose of a picking list is for the operator to have all the information necessary for preparing and dispatching products in a safe and controlled manner, thus, preventing typical errors that can occur during order processing.
Picking list contents
The information included in a standard pick list can be structured in three sections. Broadly speaking, it includes the following:
- Picking list information. The upper part contains the name of the company preparing the order, the order number assigned to the picking process, the date, the code or data of the operator in charge of preparing the order, the area of the warehouse where the goods are located, the type of shipment (standard, urgent, fragile, etc.) and the dispatch or shipment number.
- Information on the products to pick. In the centre of the document is the aisle number, rack or shelf where each item can be found, storage level, description of the goods and their internal codes, quantity of units required and number of SKUs left once the items on the picking list have been picked.
- Picking list comments and validation. The lower part of the document has a space for recording any kind of observation (goods in poor condition, broken containers, etc.) and three boxes to be signed, respectively, by the operator that picked the items, the employee that receives them and prepares the order and the person tasked with organising the order dispatch.
Company | Picking list | |||||
---|---|---|---|---|---|---|
Date: 05/21/20 | Operator: No. 24 | Warehouse: 2 | Shipment type: Standard | Dispatch number: 23 | ||
Aisle | Rack | Level | Description | Product code | Quantity | Stock |
5 | D | 1 | Chocolate chip cookies | Item 12 | 1 | 24 |
5 | I | 1 | Tomato sauce | Item 02 | 1 | 17 |
5 | D | 4 | Aftershave | Item 01 | 1 | 22 |
2 | I | 2 | Spaghetti 1 lb | Item 23 | 1 | 15 |
1 | I | 1 | Mac and cheese 7 oz | Item 24 | 1 | 29 |
Comments: Broken packaging in aisle 5, rack I, level 1 | Delivered (signature): ______ |
Received (signature): ______ |
Dispatcher (signature): ______ |
It should be noted that this picking list example can be modified according to the needs of each company. The digital variants of picking lists created by software can, in fact, be much simpler in terms of the information shown with a view to boosting operator productivity.
Types of picking lists
These lists can vary slightly based on several factors, for example, order fulfilment method, number of products contained in each order, movement flow, etc. These are the most common kinds of picking lists:
- Discrete picking list. These show products that make up a single order. The operator has to pick the items pertaining to that order and them move them to the dispatch area.
- Batch picking list. This reflects products for various orders, which the operator gathers on a single run performing batch picking. In this case, before being dispatched, the products have to be brought to a consolidation area, where they are sorted and grouped in their corresponding orders.
The type of picking list is directly related to the different order fulfilment methods.
Picking lists and the importance of a WMS
The picking list can be distributed on printed paper or in digital format. To create an automatic picking list, a warehouse management system (WMS) is a must.
The WMS generates the picking list, either in paper form or digitally. Operators use the printed list or the digital version, by means of radiofrequency scanners or picking assistance devices (voice picking, for instance), to prepare the orders without error and in an agile way.
The WMS, as in the case of Easy WMS from Mecalux, creates the picking list automatically upon receiving the purchase order from the customer. As the WMS knows the location of each product, it shows the operator the aisle and rack number, the storage level, the number of items to pick, etc. When scanners are used instead of paper, the lists appear directly on the operators’ screens and guide them step by step, showing them where to pick each product and in what quantity. Each list is complemented with barcode readers (for scanning the goods, the rack, etc.) that ensure that each action is carried out correctly.
Then, the WMS assigns a number to the container in which the items will be placed until finally being dispatched. Likewise, the WMS offers the possibility to make any manual changes relating to the task, as well as to add pertinent comments.
The software organises and manages order preparation taking into account factors such as the warehouse layout, shipping priority, picking method used and number of operators, among others.
Example of a picking list
Although the essence is the same, the structure and makeup of a picking list can vary according to whether it is created manually or by means of a WMS. Let’s take the example of a discrete picking list for a distribution company:
If the picking list is executed manually, the person responsible for preparing the lists should fill out the document with all the relevant information so that the warehouse operator can efficiently prepare the order. To do this — and if you don’t have a WMS — it’s necessary to know the layout of the facility and the exact location of each item. Likewise, if possible, the list of products should be arranged to make the operator’s route as optimal as possible.
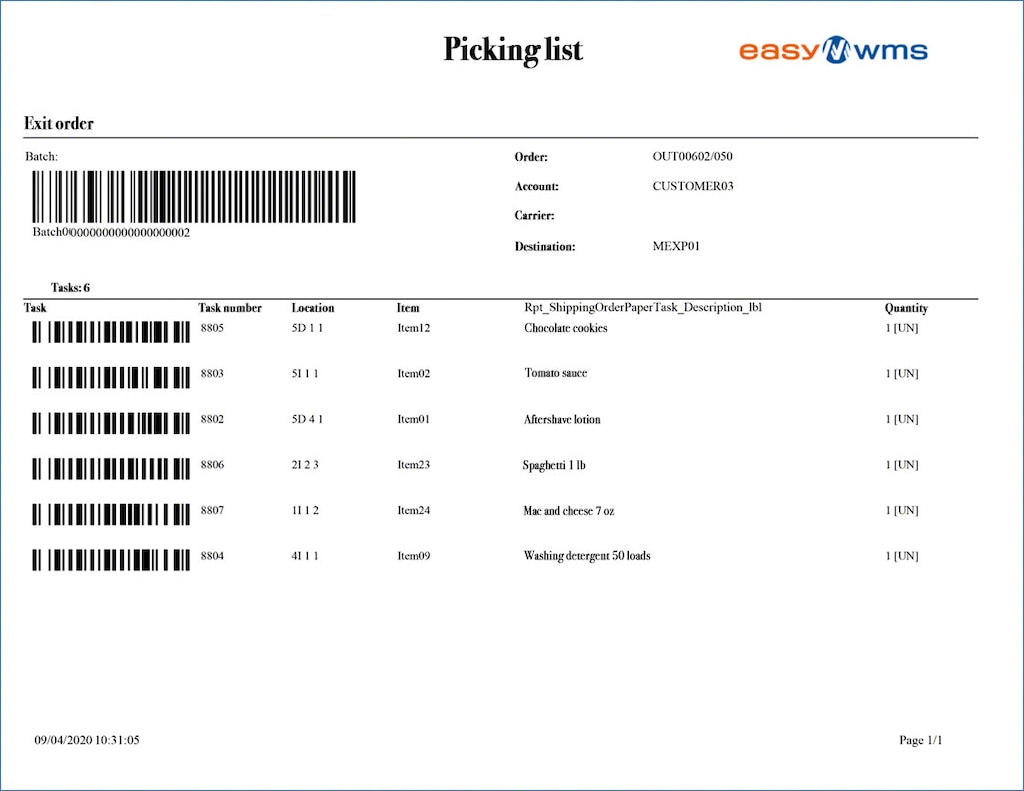
With all this information, the operator will be able to begin picking with the help of order pickers, depositing the items in the unit load that will be used for their subsequent distribution and specifying the number of remaining units available on the racks. Once the route is finished and with all the products ready, the operator makes a note of any observations and delivers the signed picking list to the person charged with preparing the shipment for dispatch.
If you have a WMS, the process involving the creation and execution of the picking list is optimised considerably, and order prep is fast and error-free.
As soon as the customer purchase order is entered, the system automatically generates the picking list. It then lets the operator know that there’s an order to prepare. Aided by a radiofrequency scanner, an order picker and a specific unit load, the worker follows the instructions from the software.
As he/she picks the products, the operator scans the items’ barcodes and confirms that the operation has been performed by means of the radiofrequency scanner. The video below shows how a picking list works in conjunction with a radiofrequency scanner and a WMS.
In the case of Easy WMS, the software also includes the option to print the picking list to help the operator prepare the order.
Picking list: fundamental for an efficient warehouse
In order to have an optimised supply chain working at peak performance, it’s essential for picking operations to be carried out without mistakes and in the shortest time possible. To achieve this, you need to rely on picking lists that facilitate the work of the operators.
If you’re still preparing lists manually and you think the time has come to get more throughput out of your warehouse, get in touch with Mecalux. We’ll show you how a WMS can help you to boost your orders by generating more competitive picking lists.