Level and flatten warehouse flooring is crucial for the proper circulation of handling equipment, for example, in standard drive-in pallet rack facilities. Some of these require a concrete floor to be very level to prevent breakdowns in the machines and, even more importantly, problems in the installation itself.
The most serious problems are in systems with turret trucks (either trilateral or bilateral), due to their great lifting height and speed of operation. With these machines, the levelling of the flooring is an extremely critical factor, since they work with minute clearances in the aisles between the shelves. Any variation in the floor can lead to a tilting of the device which, no matter how small, poses a risk to the entire installation.
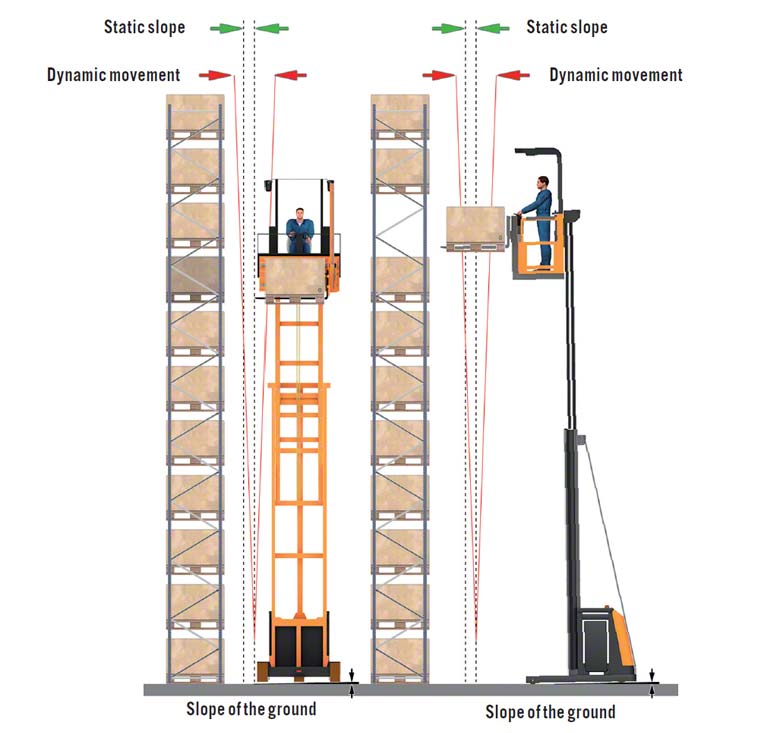
When a very narrow aisle forklift moves over an unlevelled surface, it rocks. In the absence of a suspension system, this immediately transmits the motion to the mast. Given the considerable height of this device, a single millimetre of unevenness at the base can turn into, at great heights, several centimetres of movement, as shown in the illustration above. This may lead to accidents with the loads or shelves being hit, with the danger that this entails.
Deviation will also decisively influence the height positioning of the fork assembly, creating the risk of blows when they are extended to collect or deposit a load.
Because of the above, and to avoid any danger or unfortunate incidents in the future, the floor in a working environment with narrow aisle machines must be extremely level. It is not enough for the construction company to assure that the surface is properly levelled. Experience shows that it is essential to have the relevant certification, and even the table of the sampling performed after completing the flooring.
Checking the levelling of the floor is hard work, requiring great care and the use of very accurate optical instruments. The floor must comply with parameters that vary depending on the storage system used.
Image provided by Pavindus S.A.
Correct floor levelling is vital to avoid breakdowns in handling equipment.
Leveling requirements differ depending on whether the installation is class 100, 200, 300, or 400. This class is determined by certain factors that are taken into account in the EN 15620 quality standard. In terms of handling equipment used, storage systems are classified as follows:
Class | Aisle type | Suitable for: |
100 | Very narrow |
Pallet racking unit less than 18 m high, with very narrow aisles and operated by Automated stacker cranes for pallets. |
200 | Very narrow | Pallet racking unit with very narrow aisles, operated by automated stacker cranes for pallets and with an additional system for positioning unit loads. |
300 | Very narrow |
Pallet racking unit with very narrow aisles, operated only by |
300A |
The operator continually moves up and down with the unit load and has manual height positioning. When the driver is at ground level, they have a closed circuit viewing system or the equivalent. |
|
300B |
The operator remains at ground level at all times and does not have indirect viewing devices. |
|
400 | Wide |
Pallet racking unit with narrow aisles, wide enough to allow the forklifts to turn 90º for loading and unloading. |
Narrow |
Pallet racking unit with aisles with less space, which can be used by more specialised forklifts. |
Before analysing floor leveling requirements, it is necessary to explain the difference between floor leveling and flattening, which is shown in the following illustration:
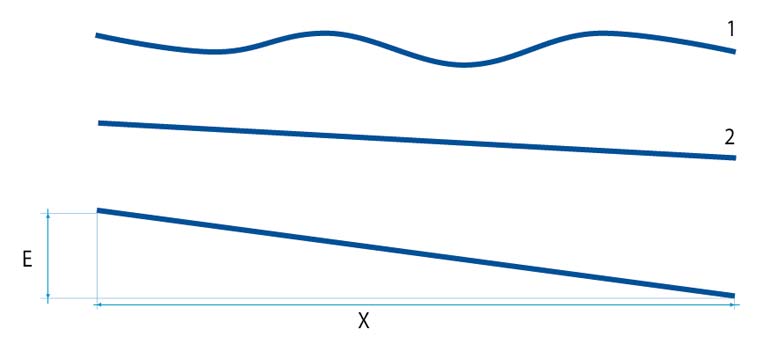
2: Profile of a flat but not levelled floor.
X: Distance between two fixed points on uneven ground (in this example, 3 m).
E: Height difference between the two fixed points 3 m apart.
The term “3-metre grid” when used in the following section refers to a set of points on the surface of the ground, 3 metres from each other in directions perpendicular to the building.
Requirements for a class 400 floor (for wide and narrow aisles)
All points in a 3-metre grid must be within ±15 mm of the horizontal reference. The table below contains the maximum values of E (the height difference between two points), according to the truck used and the height of the top level of the racking unit installed.
Type of forklift | Height of top level | Maximum value of E |
Without sideshift | More than 13 m | 2.25 mm |
Without sideshift | 8 m to 13 m | 3.25 mm |
Without sideshift | Up to 8 m | 4.0 mm |
With side slider | Up to 13 m | 4.0 mm |
Requirements for a class 300 floor (very narrow aisle)
Facilities with forklifts for class 300 (very narrow aisle) must meet very strict leveling requirements. One must bear in mind that a small slope of millimeters in the floor can become centimeters of tilt for the mast of the vehicle, with the associated risk of accidents.
The requirements for proper leveling of the ground in 300 class facilities are specified in the EN 15620 standard. The following table is provided as a summary to show the maximum values of parameter Zslope, which indicates the cross-slope of the aisle between the centers of the front wheels of the truck and E, which represents the height difference between two adjacent points 3 metres apart.
Height of top level | Value of Zslope | Maximum value of E |
More than 13 m | 1.30 mm | 3.25 mm |
8 m to 13 m | 2.0 mm | 3.25 mm |
Up to 8 m | 2.5 mm | 3.25 mm |
All points on the flooring must be within ±15 mm of the horizontal reference.
Requirements for class 100 and 200 floors (very narrow aisle)
For classes 100 and 200, despite being facilities with very narrow aisles, leveling requirements are not as strict as those for class 300 floors, given that the stacker crane does not move on the flooring, but rather on a lower guide rail.
In accordance with EN 15620, the flooring leveling requirements are as follows:
For classes 100 and 200, despite being facilities with very narrow aisles, levelling requirements are not as strict as those for class 300 floors, given that the stacker crane does not move on the flooring, but rather on a lower guide rail.
In accordance with EN 15620, the flooring leveling requirements are as follows:
Aisle length | Levelling with respect to horizontal ref. |
Up to 150 m | +/-1.5 mm |
250 m | +/-20 mm |
For intermediate aisle lengths (between 150 m and 250 m), the data can be interpolated linearly.